Powder Coating Service
We offer powder coating services to achieve a tough, long-lasting finish with various color selections.
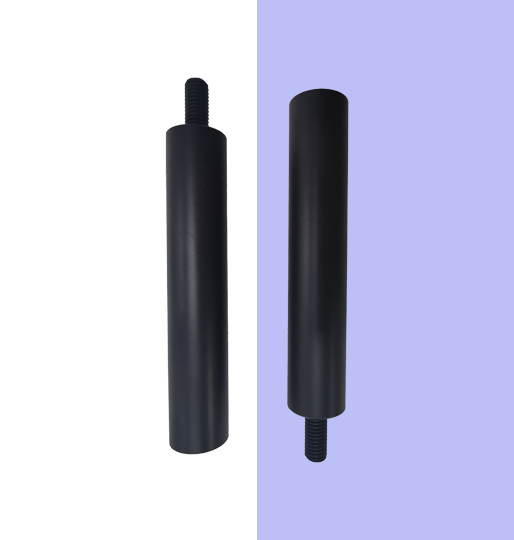
Powder Coating Specification
A completely dry powder paint, a polycarbonate or thermoset polymer, is electrostatically applied to a metal substrate. Unlike conventional liquid paint, powder coating doesn’t require any solvent to hold the binder and filler of the paint in a liquid suspension.
Materials |
Colors |
Glossiness |
Thickness |
Surface Texture |
Metals |
White, Black, RAL and Pantone |
Matte, Glossy |
50μm to 150μm |
Flat/Texture |
---|
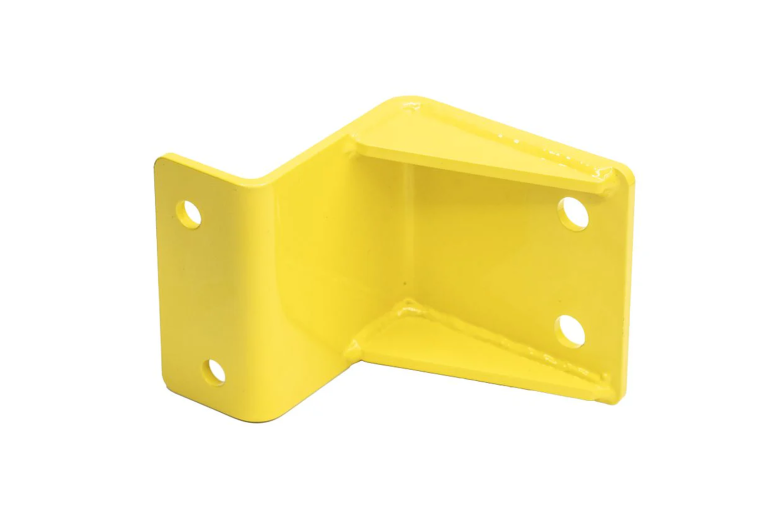
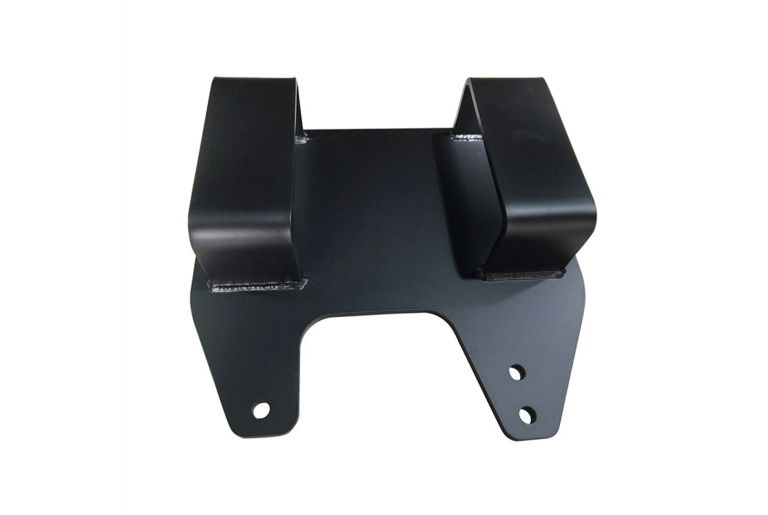
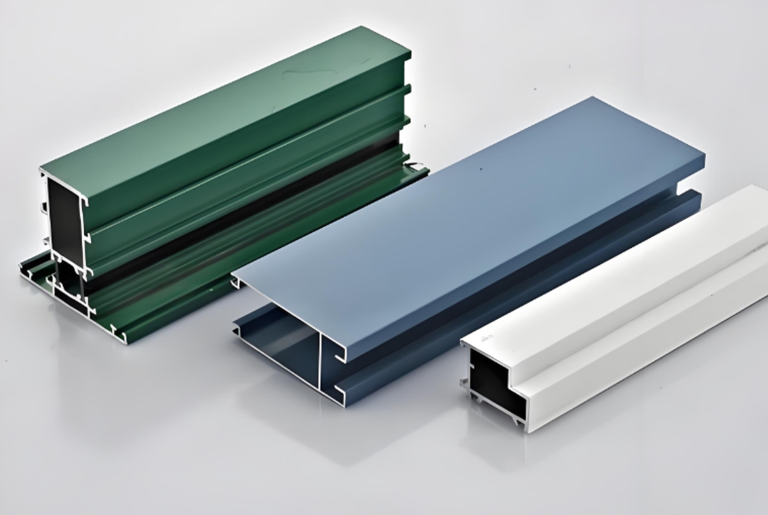
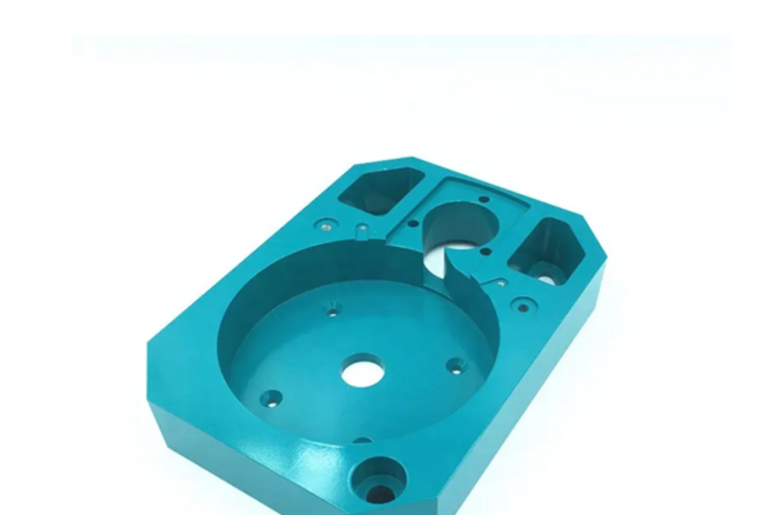
Advantages
- It produces a tough, long-lasting finish
- Available in a wide range of colors and finishes
- It is solvent-free and emits negligible volatile organic compounds (VOCs)
- Provides adequate protection against rust and corrosion Enhances the lifespan of metal parts
Notes
- Tiny features/edges are prone to powder buildup
- For special usage scenarios, please specify. (e.g., outdoor, chemical exposure, corrosive immersion, etc.)
Powder Coating Finish
Powder coating is an advanced surface treatment process where a dry powder is applied onto the metal surface using resins, pigments, and other additives.
The applied powder is electrostatically charged and is usually sprayed onto a pre-prepared surface-more often, metal-but it can also be applied to several other materials, including plastic or wood. The parts are then subjected to an oven, in which the heat melts and fuses the powder at high temperatures to make a very smooth and highly durable coating, thus protecting the material from corrosion, UV rays, and general wear and tear.

- Powder finishing entails putting on hold parts by means of a "jig" or "rack." This will leave marks on your part where powder finishing wasn't feasible. If there are areas where you can not approve "jig" marks, please bear in mind to consist of a technical drawing showing these locations.
- Remember to indicate in your CAD file whether you want specific part areas to be masked or plugged. As material is applied to the surface during powder coating, all threaded and reamed holes or other critical-to-function surfaces are plugged or masked as standard.
- Tolerances are met before the coating finish. We recommend that you ask for clarifications about masking as needed.
- Powder coating polymers are usually insulative and offer poor electrical conductivity.
Powder Coating Design Considerations
Can powder coating be applied to all metals?
Powder coating is most often applied to steel, aluminum, and iron, although most metals can accept the powder coating. For optimal adhesion, the substrate must be clean of contaminants. It may not work well on materials such as plastic or wood.
Is powder coating environmentally friendly?
Yes, powder coating is a lot more eco-friendly compared to most conventional liquid coatings. It contains no solvent or chemical components within it, and the excess can be recycled for more eco-friendly finishing. Moreover, it also tends to emit less volatile organic compound fumes, which are believed to be bad for the environment.
Is powder coating more durable than anodizing?
While both provide very good durability, the purpose is different for each of them in their application. Powder coating provides a harder layer, which is extremely resistant to scratches, fading, and corrosion, while the anodizing process deals more with the development of an oxide corrosion-resistant layer in materials such as aluminum. The decision will depend upon your application and specific needs about performance. For more detailed comparison, read our blog: Finishing Showdown: Anodizing vs Powder Coating
Does powder coating provide a smooth finish?
Yes, powder coating gives a finish that is uniform and smooth with no streaks or brush marks. The electrostatic process ensures a very even cover, enhancing both the appearance and durability of the coated surface.