CNC machining is a subtractive process that combines software and code with cutting tools to cut extra materials from the blank piece and shape it into desired geometries. it is widely used in a variety of industries due to its precision and speed. To make full of this advanced technology, it is essential to understand a set of design guidelines when designing for CNC machining projects.
CNC Machining Progress
CNC machining is a subtractive manufacturing process that leverages a combination of computerized controls and a variety of cutting tools to rapidly remove layers from a solid block of material, to create a part with desired geometries. At SogaWorks, we provide CNC machining capacities including milling, turning, grinding and more, we can machine both metals and plastics.
CNC milling
CNC Milling is a subtractive machining process that utilizes computer-controlled technology to cut the material from a workpiece and then shape it into a final part. CNC milling processes are versatile and can be utilized in many industries. They are efficient in the creation of parts with complex geometries.
Characteristics of SogaWorks CNC milling services
Maximum part size | 4000 x 1500 x600mm |
Minimum part size | 5 x 5 x 5mm |
Standard tolerance | ±0. 1mm, or tighter tolerance on your request |
Materials | Metals and plastics |
CNC turning
CNC turning is a subtractive machining process that utilizes a cutting tool to remove materials from a rotating workpiece. When the machine moves along the surface of the workpiece, the material is removed to form the desired shape. CNC turning can manufacture different conical, cylindrical, and helical designs.
Characteristics of SogaWorks CNC milling services
Maximum part diameter | 500mm |
Minimum part diameter | 1mm |
Maximum part length | 1500mm |
Standard tolerance | ±0.01 mm |
CNC Machining Design Guidelines
Tolerances
At SogaWorks, We machine your custom parts according to ISO2768 Medium unless otherwise specified. Tighter tolerances can be achievable, we can manufacture parts with a tolerance tighter than ±0.0254mm(±0.001 inches) according to your 2D drawing specifications. However, Unless it is a critical feature, we do not recommend using tighter tolerances, which will increase machining times and costs.
Linear dimensions
Limits for nominal lengths | ISO2768-c | ISO2768-m |
0.5mm to 3mm | ±0.2mm | ±0.1mm |
over 3mm to 6mm | ±0.3mm | ±0.1mm |
over 6mm to 30mm | ±0.5mm | ±0.2mm |
over 30mm to 120mm | ±0.8mm | ±0.3mm |
over 120mm to 400mm | ±1.2mm | ±0.5mm |
over 400mm to 1000mm | ±2mm | ±0.8mm |
over 1000mm to 2000mm | ±3.0mm | ±1.2mm |
over 2000mm to 4000mm | ±4.0mm | ±2.0mm |
Click to download the document ISO 2768 tolerance standard.
Wall thickness
The choice of wall thickness can be tricky, as decreasing wall thickness may lead to the reduction of stiffness of materials, increasing vibration during machining and then decreasing the achievable dimensions. A common rule is to design walls with a thickness of 0.8mm for metals as well as 1.5mm for plastics. The higher dimensions for wall thickness of plastic components to be machined are due to their tendency to shrink and warp.
- Metals: 0.8mm at minimum
- Plastics: 1.5mm at minimum
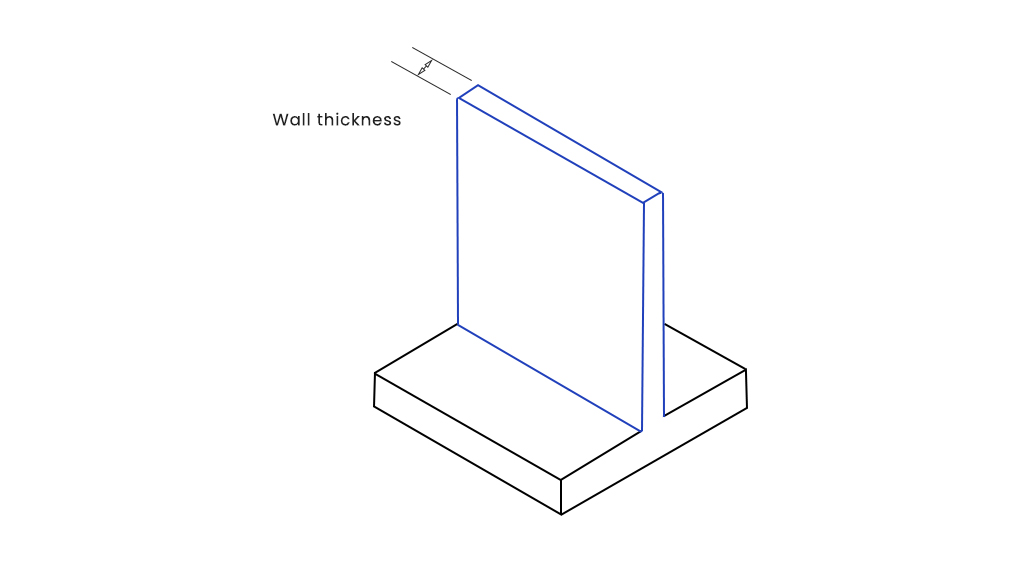
Thread Length
SogaWorks can accommodate and cut metric threads, imperial UNC, and UNF among others. All threads should be marked on your 2D drawings. It is believed in the minds that the longer the thread is, the stronger the connection. However, increasing the length of the thread to 1.5 times the diameter will make a difference to the connection. It is suggested that the design of your thread be using a length of 1.5 times to 3 times larger than the diameter. For threads that are in blind holes, you should add an unthreaded length that is equal to 1.5 times the diameter.
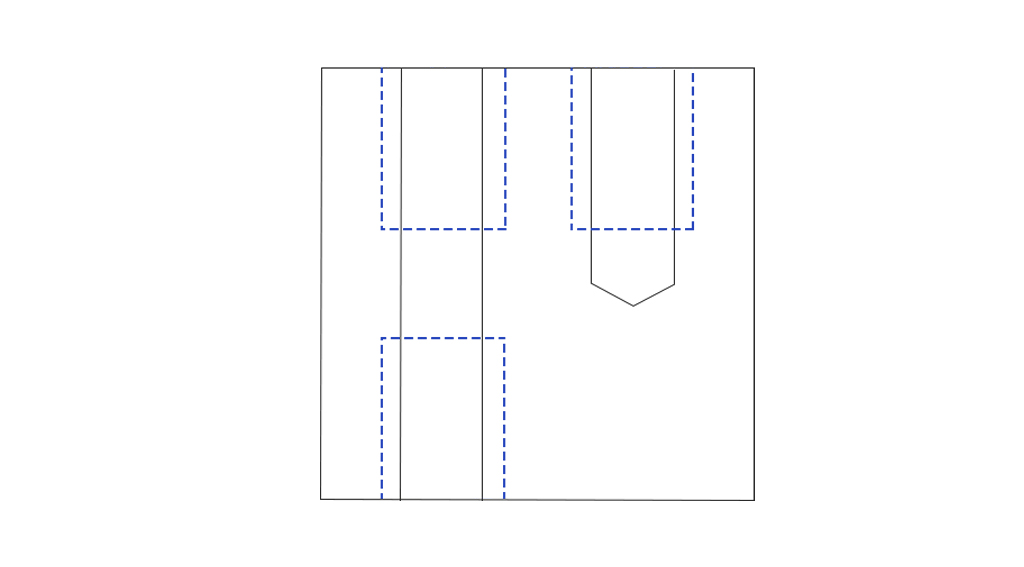
Internal Edges
End mills and other cutting tools utilized in CNC machine machining are usually cylindrical, which leads to a radius within corners that have been machined. Cutting tools with smaller diameters will often reduce the radius, however, it isn’t always possible to create internal vertical corners because of the limitation of tool’s diameter. Additionally, it can lead to more issues, including delays in lead times and increases in costs.
When designing CNC machined parts, it is recommended that the vertical radius is one-third the size of the cavity or greater.
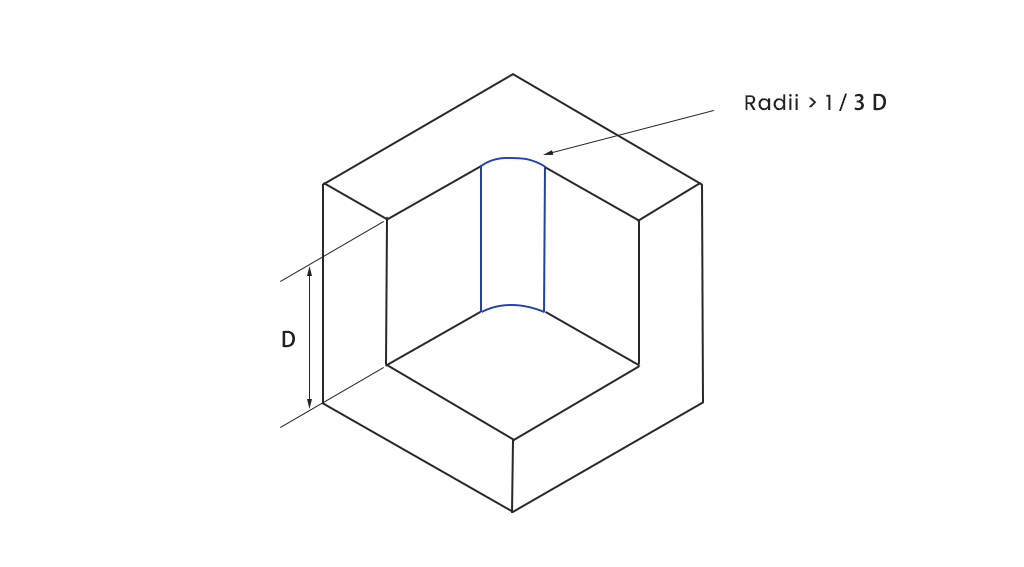
Cavities
End mill tools are equipped with a limited cutting length, which is typically 3-4 times the diameter. Deflection of the tool and vibrations increase when the cavities have a higher depth-to-width ratio. Therefore, we suggest restricting the depth to 4 times the length to guarantee good results. Deeper holes(up to 10 times the diameter) are available but they will cost more.
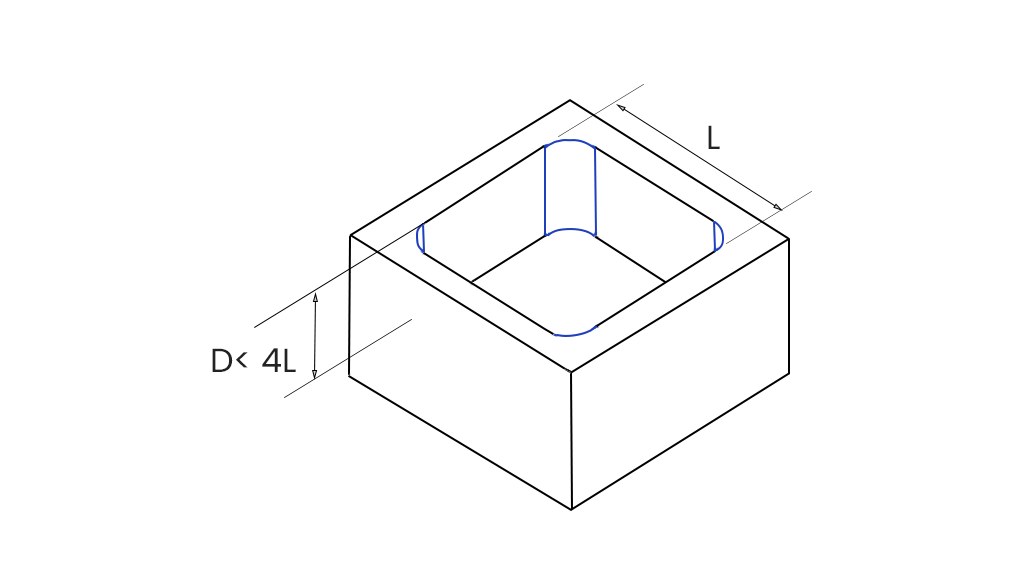
Hole
Holes can be machined using an end mill or a drill bit tool. Using a standard size for holes with less than 20mm diameter is recommended. The deeper hole (up to 10x the size) is also possible however we suggest limiting your depth up to 4 times the diameter.
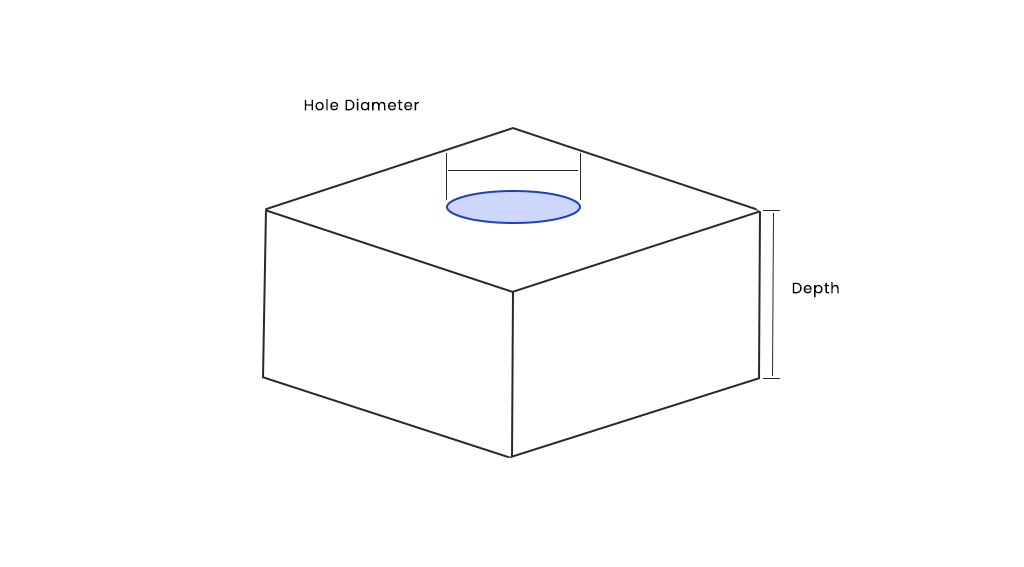
Text
If text is required, choose the engraving instead of embossing. Because engraving takes less material.
It is suggested to use Sans Serif fonts of at minimum 20 points to avoid small, undesirable characteristics.
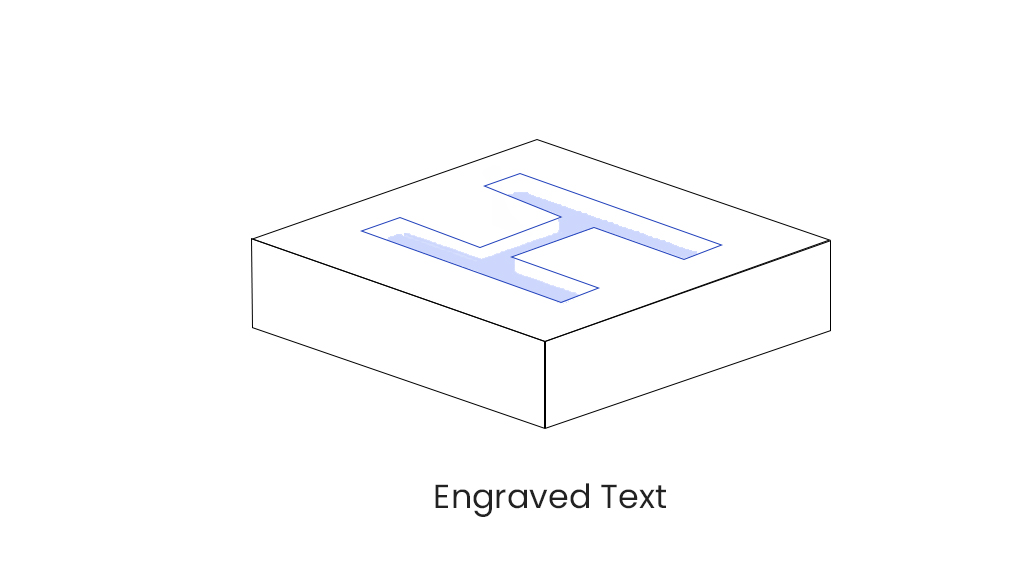
Summary of design guidelines
Wall thickness | Metals: 0.8mm at minimum Plastics: 1.5mm at minimum |
Thread Length | 1.5x to 3x hole diameter |
Internal Edges | ⅓ times cavity depth or larger |
Cavities | Limit depth to 4x its length |
Holes | Limit depth to 4x its diameter |
Text | Engraved preferred, font size 20 or larger |
Cost Reduction CNC Design Tips
CNC-machined parts are used extensively in diverse industries because of their high precision, speed and effectiveness. But, it usually costs more than other processes, such as 3D printing. This chapter offers some design tips that will assist in reducing the total costs of your CNC-machined parts.
- Remove the deep Pockets. The process of eliminating deep pockets involves the removal of more materials. Additionally, special tools can be utilized to achieve an exact depth. This means longer machining times and higher prices. Thus, reducing the depth of pockets.
- Limited Tighter Tolerances. The greater the precision greater the price. Limit tolerances to the extent that is required (such as in the case of critical functions) and leave the remainder of the model within a tolerance standard.
- Choose engraved over embossed. Engraved details often require less material to remove than embossed ones and, overall lower costs.
Start Your CNC Machined Projects
SogaWorks is an expert in CNC machining, we provide precision CNC machining services including CNC milling and turning and more. We offer a wide range of materials, from high-quality metals to top-notch plastics. Our experienced team and state-of-the-art machining capabilities enable us to deliver high precision and quality to customers. To get an instant quote, upload your models on our instant quoting platform.