Aluminum 7075 is a high-strength, heat-treatable alloy, popular for its excellent mechanical properties and strength-to-weight ratio. This alloy consists of a major composition of aluminum, zinc, and small amounts of magnesium and copper. Thus, it has excellent resistance against stress and fatigue. This article will explore its major properties, processing techniques, and applications of aluminum 7075, so readers can have an extended overview regarding the capabilities of this alloy under different industrial settings.
Overview of Aluminum 7075
Aluminum is a heat-treatable alloy that belongs to the 7xxx series of aluminum alloys. It is primarily alloyed with zinc with a content of about 6%. The grade is known for its excellent mechanical properties such as high strength, lightweight, and fatigue resistance. While aluminum 7075 has excellent strength, it can be prone to stress corrosion cracking in certain environments and often requires protective coatings or anodizing to improve its corrosion resistance.
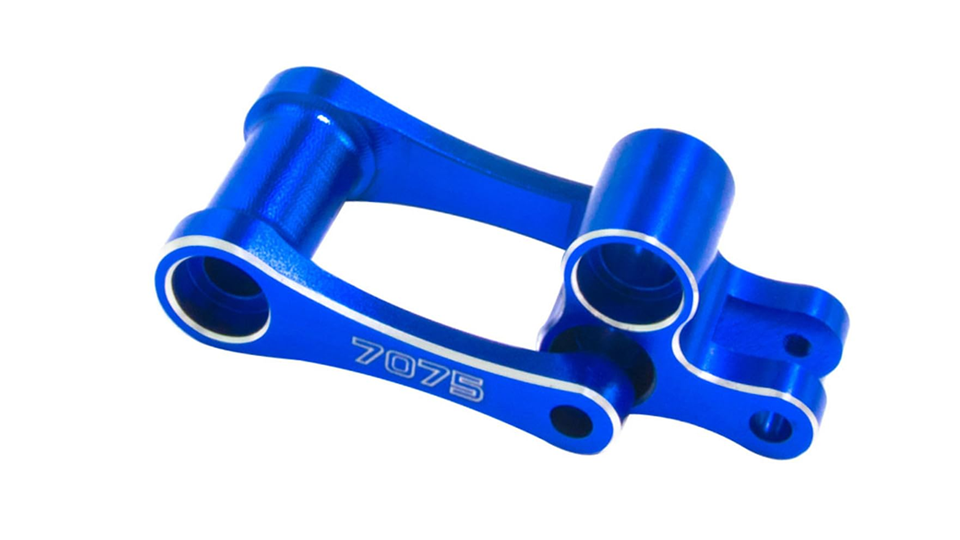
Aluminum 7075 is composed of 5.1–6.1% zinc, 2.1–2.9% magnesium, and 1.2–2.0% copper, along with trace amounts of other elements like chromium, silicon, and manganese.
Table 1. Composition of aluminum 7075 alloys (%)
Al | Zn | Mg | Cu | Cr | Fe | Mn | Ti | Si | |
Remainder | 5.1-6.1 | 2.1-2.9 | 1.2-2.0 | 0.18-0.28 | 0.50 | 0.30 | 0.20 | 0.40 |
Tempers of Aluminum 7075
The commonly used tempers of aluminum 7075 include O-temper, T6, T651, T7, T7351.
7075-O
This is an un-heat-treated 7075 alloy that has a maximum tensile strength of no more than 240 MPa, and a maximum yield strength of no more than 120 Mpa. The material has excellent corrosion resistance and fatigue resistance.
7075-T6
7075-T6 is a solution heat-treated and artificially aged. This material has maximum tensile strength no more than 560 MPa, and maximum yield strength no more than 480 Mpa. This is the most commonly used temper of 7075 aluminum alloy.
7075-T651
7075 -T651 is solution heat-treated, stress relieved, then artificially aged. This material has maximum tensile strength no more than 550 MPa, and maximum yield strength no more than 460 Mpa. The stress relief is accomplished by stretching the metal by an amount that depends on the type of standard wrought product being made (sheet, plate, bar, or forging).
7075-T7
7075-T7 is a solution heat-treated and stabilized by artificial averaging. This material has a maximum tensile strength of no more than 500 MPa and a maximum yield strength of no more than 410 Mpa. It has the second-highest ductility compared to the other variants of 7075 aluminum.
7075-T7351
7075-T7351 is solution heat-treated, stress-relieved, and then stabilized by artificial averaging. This material has maximum tensile strength no more than 510 MPa, and maximum yield strength no more than 410 Mpa.
Table 2. Mechanical properties of aluminum 7075 alloy
Temper | Tensile strength, MPa | Yield strength, MPa | Elongation, % | Hardness, HB |
7075-O | 240 | 120 | 12 | 59 |
7075-T6 | 560 | 480 | 8 | 150 |
7075-T651 | 550 | 460 | 8 | 150 |
7075-T7 | 500 | 410 | 9 | N/A |
7075-T7351 | 510 | 410 | 7.5 | 140 |
Properties of Aluminum 7075
Aluminum 7075 is a high-performance alloy known for its good mechanical properties, particularly its strength-to-weight ratio, which makes it an ideal choice for demanding industries such as aerospace and automotive. To truly understand why 7075 is so highly regarded, it’s important to examine its key material properties in more detail.
Tensile Strength: 560 MPa
Tensile strength is the greatest possible stress a material can endure while being stretched or pulled before breaking. In this respect, aluminum 7075 has a tensile strength of 560 MPa—that is to say, it can withstand high forces before failure. This tensile strength level makes 7075 aluminum ideal for applications where resistance to high forces, without stretching or breaking, is needed, like the structural components of airplanes and other military equipment.
Yield Strength: 480 MPa
Yield strength is the stress at which material begins to deform plastically, meaning that it will no longer return to its original shape once the stress is removed. The yield strength of 7075 aluminum is 480 MPa. This is one of the most critical properties, as it sets the maximum loading that the material can withstand without permanently bending or warping.
From a practical standpoint, this high yield strength makes 7075 aluminum an excellent material for components that need to keep their shape when subjected to heavy loads, like aircraft wings, fuselage frames, and other structural elements in aerospace engineering.
Hardness: 150 HB
Hardness refers to resistance to indentation, abrasion, or scratching. The hardness of aluminum 7075 is rated at 150 HB (Brinell hardness). This property would be of most interest in parts that are going to be subjected to wear and tear, or whose surface must be resilient enough to withstand damage on the surface.
Generally speaking, with the increase in hardness, the wear resistance increases, but it also becomes more and more difficult to machine. So, regarding the 7075, it will excel in areas such as gears, tooling, and high-wear parts used in machinery, aerospace, and military applications.
Density: 2.85 g/cm³
Density is defined as the mass of a material per unit volume. The density of aluminum 7075 is 2.85 g/cm³, which puts it on the lower end in comparison to some other materials, such as steel or titanium. This helps the alloy stay lean and mean in terms of weight, which is very important when weight is everyone’s concern with priorities.
Electrical Conductivity: 33% IACS
Electrical conductivity is the ability of a material to conduct electric current. The 7075 aluminum has electrical conductivity at 33% IACS—International Annealed Copper Standard. This would imply that the 7075 is somehow less conductive than pure aluminum, which has a conductivity of about 60% IACS.
Thermal Conductivity: 130 W/m·K
Thermal conductivity describes a material’s ability to conduct heat, for aluminum 7075, this value is 130 W/m·K. Although it is only about half the value of pure aluminum at 235 W/m·K thermal conductivity, it still allows 7075 to perform adequately in most applications where an important transfer of heat takes place.
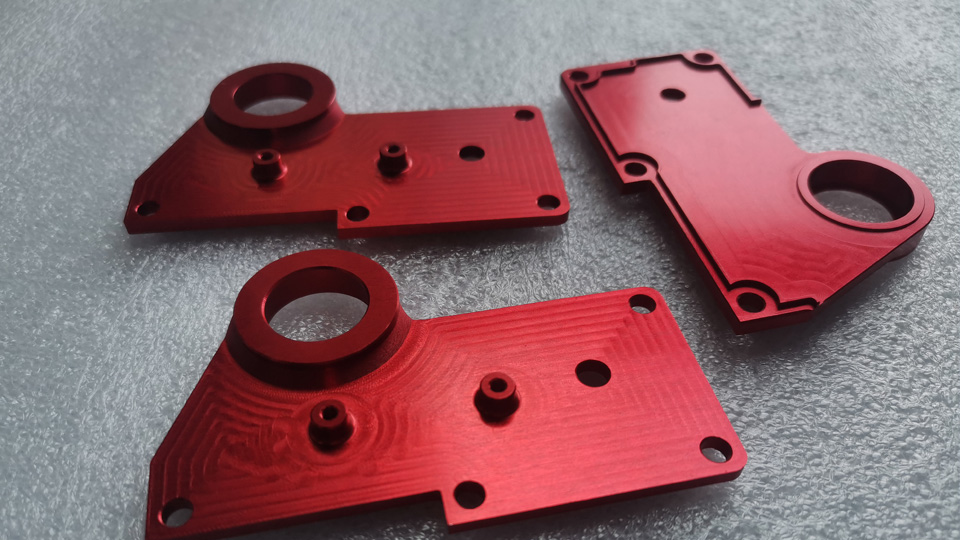
Thermal expansion: 23 µm/m·K
Thermal expansion is the process of the material growing in size as it gains heat. The coefficient of thermal expansion for aluminum 7075 has been reported to be 23 µm/m·K, meaning that for every meter, the length will expand 23 microns as the temperature is increased by 1°C. This represents fairly low thermal expansion; therefore, temperature changes do not disrupt the dimensional stability of 7075 aluminum.
Elastic Modulus: 70 GPa
Elastic modulus, often referred to as the modulus of elasticity, is a measure of a material’s stiffness or its resistance to deformation when under stress. The elastic modulus for aluminum 7075 is 70 GPa. This would imply that the alloy is fairly stiff since there is a very small tendency for deformation under applied loads. 7075 aluminum has a high elastic modulus, making it particularly suitable in applications where dimensional stability and low deflection are realized. The stiffness of the 7075 may be capitalized upon to great advantage in such members as aircraft wings and structural beams of high-performance machinery, ensuring that these retain their shape and strength under heavy loads or stresses.
Melting Point: 480°C
The melting point is the temperature at which a material would transform from being in a solid state to a liquid. The melting temperature of aluminum 7075 is 480°C, which is rather high. It can thus perfectly apply to conditions wherein it is subjected to extreme temperature exposure without losing its integrity.
Weldability: Poor
Aluminum 7075 has very poor weldability, its high strength, combined with its composition of Zinc and copper, results very easily in cracking during the welding process itself. Specific techniques, such as preheating controlled cooling, and particular filler materials, are used in order to achieve reliable welding. Therefore, aluminum 7075 is not normally selected for any application that mandatorily involves welding; instead, other kinds of joining are resorted to, such as bolting, riveting, or adhesive bonding.
However, Aluminum 7075 can exhibit good weldability with the proper techniques.
The most common method is Gas Tungsten Arc Welding (GTAW), which offers high-quality welds.
Gas Metal Arc Welding (GMAW) is also viable, but care must be taken to minimize heat input and prevent heat cracks during the welding process.
Resistant spot welding with a truncated electrode is highly effective for joining 7075, but the welding interfaces must be thoroughly cleaned to ensure a strong bond.
Friction Stir Welding (FSW) produces high-quality solid-state welds at all temperatures of 7075 aluminum.
Corrosion Resistance: General
The general corrosion resistance of Aluminum 7075 is relatively lower compared to some other aluminum alloys, such as aluminum 6061. However, its major weakness relates to the susceptibility of this alloy to stress corrosion cracking under conditions that could be considered quite extreme—for instance, when in a marine environment or under strongly acidic conditions. To get around this, aluminum 7075 is usually anodized or given protective coatings that make it resistant to corrosion.
Table 3. Properties of Aluminum 7075 alloys(T6)
Properties | Value |
Tensile strength, MPa | 560 |
Tensile strength, MPa | 480 |
Hardness, HB | 150 |
Density, g/cm3 | 2.85 |
Electrical conductivity, IACS | 33 |
Thermal Conductivity, W/m-K | 130 |
Thermal Expansion, µm/m-K | 23 |
Elastic modulus, GPa | 70 |
Melting point, ℃ | 480 |
Weldability | Poor |
Corrosion resistance | General |
The price of Aluminum is 7075
There are quite a few factors contributing to the price of 7075 aluminum: market demand, production cost, supplier, and material specifications. The price is generally higher than other aluminum-based alloys because this is a high-strength alloy, and it includes a complex production process.
The general price of a 7075 aluminum alloy sheet is about $10-20 per kg, depending on size, thickness, surface treatment, and purchase quantity.
The price of a 7075 aluminum alloy round bar is about $12-22 per kg; detailed quotations should be based on the diameter of a bar and according to the supplier.
Make Your Idea Take Shape!
If it’s 7075-T6, it will surely be costlier due to the strengthening of heat treatment that enhances the material properties. Commonly, 7075-T6 alloy will cost about 5-15% higher than the regular 7075 aluminum alloy.
Advantages of Aluminum 7075
Aluminum 7075 has the advantages of high strength with good fatigue resistance, especially appropriate for those applications which require a high-performance material. Some examples are the aerospace and military industries. A high content of zinc provides significant strengthening by precipitation hardening in 7075, while the relatively high content of chromium enhances the ductility and toughness of the alloy by reducing crystal growth.
However, 7075 aluminum has some disadvantages, like corrosion resistance, rated average against other categories of aluminum alloys, for instance, the 2000 series. Furthermore, this alloy is poorly weldable and, therefore, fabricated, where it is highly sensitive to welding techniques and processing conditions. Considering these disadvantages, the excellent strength-to-weight ratio coupled with the resistance to fatigue of this alloy makes it a choice in very demanding applications where performance cannot be compromised.
Machining Processes for Aluminum 7075
7075 aluminum alloy has good machinability, but because of the high intensity and hardness, the choice of machining methods and parameters must be well considered to avoid defects such as tool wear, heat generation, and material distortion.
Precision parts can be manufactured in 7075 aluminum by traditional cutting methods such as milling, turning, and drilling. Given the material’s high strength, sharp, high-quality cutting tools need to be used, and the optimization of cutting speeds and feeds should be used along with coolant usage to minimize the generation of heat. Surface finishing techniques, like anodizing, are also frequently used to enhance its resistance to corrosion and pleasing appearance.
For complex geometries, 7075 aluminum can also be successfully processed using CNC machining, which enables high precision and good repeatability. In some instances, electrical discharge machining(EDM)may be a non-traditional method to produce an intricate shape. Correct tooling coupled with good heat management and adherence to machining best practices enables the alloy to retain its mechanical properties to achieve surface finish and good dimensional accuracy.
Applications of Aluminum 7075
Aluminum 7075 is widely used in many industrial applications due to its excellent mechanical properties. It is used most in the aerospace industries, where it acts as material for structural parts such as aircraft wings, fuselages, and landing gear. The alloy also has many uses in military equipment, including vehicle parts, the hulls of boats, cycling frames, and the highest-end sporting gear, due to its combination of strength and low mass. Another important use for 7075 aluminum is in the precision machining of highly stressed parts for automotive, industrial machinery, and tooling applications where performance and longevity are critical.
Conclusion
Aluminum 7075 is thought to be a preferable choice due to its outstanding strength and durability. However, both its machinability and welding characteristics need to be properly selected in order to get the best results during production. The properties of 7075 can be tailor-made using different heat treatment processes, surface treatments, and machining techniques to meet specific performance criteria. While its cost and associated processing difficulties may limit its application in some fields, the advantages of performance under high-performance conditions in the aerospace and precision engineering industries continue to outweigh the disadvantages.