Aluminum stamping is a process that transforms blanks into desired shapes using dies and punches, making use of a unique metal fabrication technique. And it plays an extremely vital role in manufacturing precise parts and components. So aluminum metal stamping is critical in industries that need precision and durability, such as aerospace, automotive, and electronics.
In this article, I’ll share my thoughts and experiences to help you understand why aluminum stamping is essential in production. In addition, you will also find all the other information you are searching for right here, such as the types, benefits, applications, and common problems of aluminum metal stamping.
Therefore, if you need custom aluminum stamping services, please don’t hesitate and contact us. We are fully prepared to meet all of your stamping requirements with both flexibility and precision.
Definition: What is Aluminum Metal Stamping?
As a metalwork technique, aluminum stamping uses a stamping die and a press to put pressure on an aluminum sheet or bar, which makes it bend and change shape so that the desired final shape and size can be achieved. This manufacturing process is usually carried out in a cold state; hence it is also known as cold stamping. Aluminum metal stamping usually uses the raw material of sheet or strip; hence it is also known as aluminum sheet stamping.
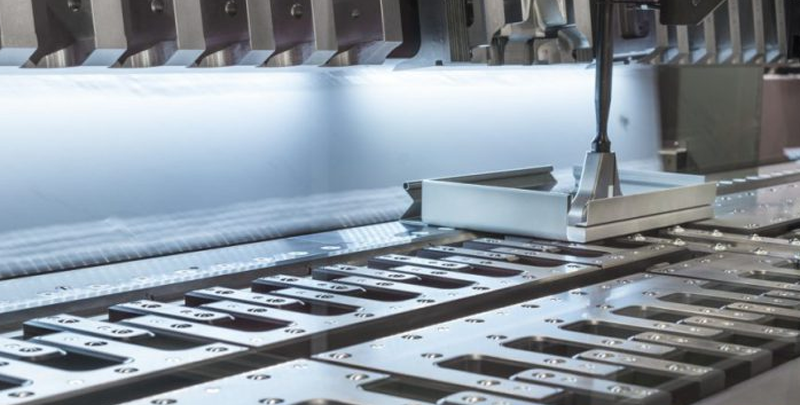
While aluminum sheet metal stamping refers specifically to the process of stamping as applied to aluminum sheet. The term places more emphasis on the fact that the starting material is in the form of a flat sheet.
Types of Metal Stamping Process
Metal stamping refers to a wide range of industrial techniques. You may use these stamping techniques to shape aluminum sheet metal into any shape. The primary processes for stamping aluminum are listed below.
Blanking
The blanking aluminum stamping process involves cutting a section from an aluminum sheet using metal stamping tooling (dies).
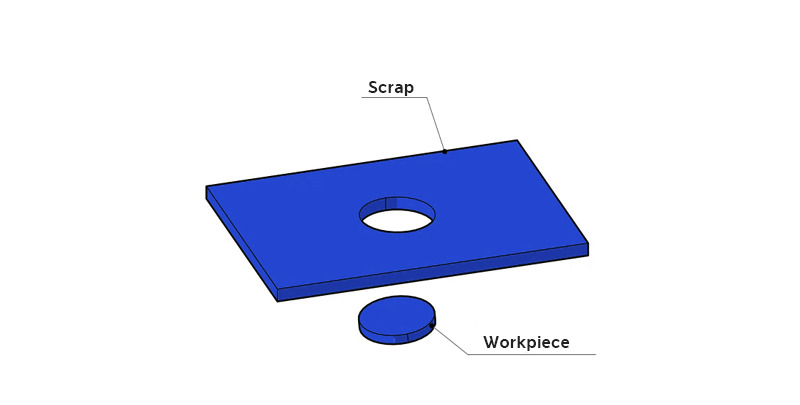
Characteristics
- Removes a section of the aluminum sheet to form the desired shape.
- Similar to punching but typically removes a complete part from the sheet.
Applications: Manufacturing of flat parts for automotive, aerospace, and electronics industries.
Piercing
The piercing aluminum metal stamping process uses punches and dies to create holes or notches in aluminum sheets.
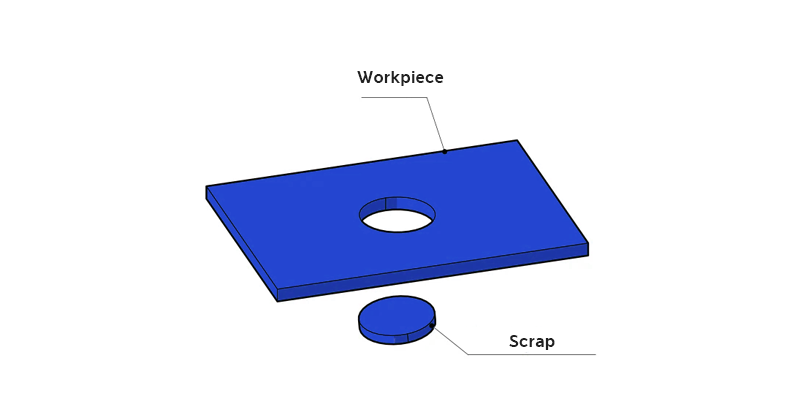
Characteristics
- Creates holes or notches.
- A metal sheet is punched to form a shape, often for mounting or assembly purposes.
Applications: Creating holes for fasteners in automotive, appliance, and structural components.
Coining
The coining aluminum stamping is a bending technique where the aluminum sheet is placed between a punch and die, and force is applied to form a shape.
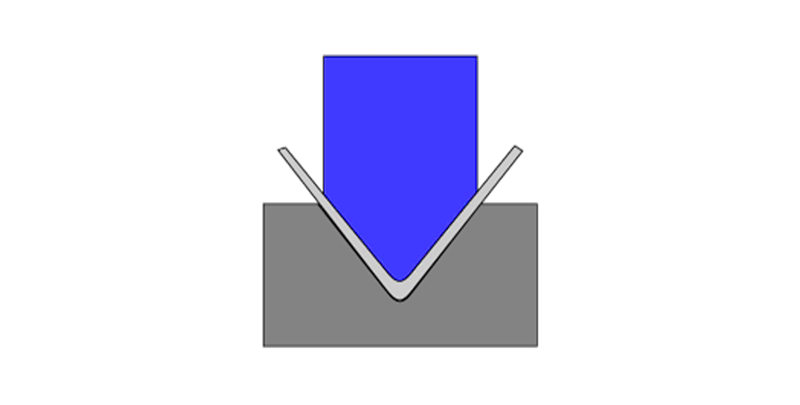
Characteristics
- The aluminum sheet is stamped between punch and die.
- Can form shapes like L, V, or U depending on the requirements.
- Typically used for fine details.
Applications: Precision components in electronics, appliances, or automotive parts.
Deep Drawing
The deep drawing aluminum metal stamping involves pushing aluminum into a cavity to form deep depressions in the material, typically under tensile force.
Characteristics
- Forms deep parts, often used for shaping containers or hollow objects.
- Stretching of the material can be a challenge and must be managed.
Applications: Manufacturing of deep-drawn parts such as cans, containers, or automotive body parts.
Embossing
The embossing aluminum stamping process involves forming a raised or recessed pattern on the aluminum surface by pressing tooling with the desired design.
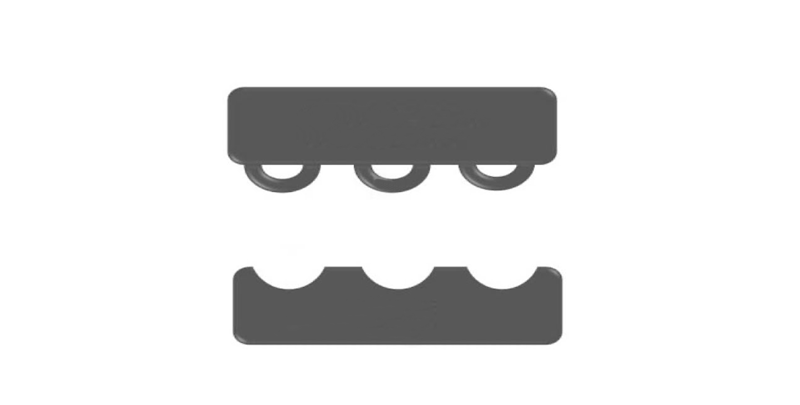
Characteristics
- Used to create designs or patterns on aluminum surfaces.
- Commonly used for decorative purposes or branding (nameplates).
Application: Decorative components, nameplates, logos, and branding in electronics and signage.
Flanging
The flanging aluminum metal stamping process uses specialized tooling to create flanges or flares on the aluminum surface.
Characteristics
- Creates an outward bend (flare) or inward bend (flange) on the edges of aluminum parts.
- Important for joining or sealing parts together.
Application: Applications requiring joining or sealing, such as ducts, automotive parts, or frames.
Aluminum Alloy for Metal Stamping
Metal stamping employs a wide range of metals and alloys to create high-performance components with remarkable accuracy and repeatability. There are a range of metals suitable for metal stamping process, including aluminum, copper, brass, nickel, titanium, steel, stainless steel, and so on. This part will guide you on why to choose aluminum alloys as the metal stamping materials and take you to have an allover look at the aluminum grades for metal stamping.
The Reason to Choose Aluminum Alloy for Metal Stamping
Choosing the appropriate material is critical to obtaining the intended performance and lifetime of the stamped item. We choose the suitable metal based on the part’s needs, which include strength, durability, and corrosion resistance. Other considerations include the part’s intended application, operational environment, and cost limits. So why do we choose aluminum?
As we all know, aluminum is lightweight but sturdy, corrosion-resistant, and possesses high thermal and electrical conductivity. With these characteristics, aluminum is an ideal material for a wide range of applications, from complex electronic components to durable automotive parts.
Lightweight, yet Strong
Aluminum has an outstanding strength-to-weight ratio, which is one of its most notable characteristics. This means that aluminum components are strong enough to endure significant stress and strain while remaining light enough to contribute to product weight reduction.
This feature is critical in industries such as aerospace and automotive, where weight reduction can contribute to increased performance and fuel efficiency.
Malleable and Formable
Aluminum is highly malleable, which means it can easily form into a variety of shapes without breaking. This feature is very useful in stamping procedures, allowing for the creation of complex parts with detailed designs.
Conductivity
Aluminum is a powerful heat and electricity conductor, making it a suitable material for electrical components and heat exchangers. Aluminum’s use in the food and beverage business stems from its non-toxic properties.
Corrosion Resistance
Aluminum naturally creates a protective oxide covering, making it extremely corrosion resistant. This feature is extremely useful in areas where moisture, chemicals, or salt are prevalent, ensuring the longevity and durability of aluminum parts.
Make Your Idea Take Shape!
Grades of Aluminum Used for Metal Stamping
There are a lot of aluminum alloy grades suitable for metal stamping. The decision will be based on your individual application requirements. Most aluminum grades are ideal for any metal stamping operation. To comprehend aluminum grades for any metal stamping, please see the table below.
Aluminum Alloy Grade | Main Alloying Element | Description |
1xxx | 99% pure aluminum | This kind of aluminum alloy is commercially pure aluminum with excellent corrosion resistance and high workability. |
2xxx | Copper | High-strength alloys are often used in aerospace and military applications. |
3xxx | Manganese | Good corrosion resistance and formability, commonly used in roofing, siding, and cooking utensils. |
4xxx | Silicon | Welding, brazing, and the manufacture of aluminum alloys all use low-melting-point alloys. |
5xxx | Magnesium | It is known for its excellent corrosion resistance, especially in marine environments; it is commonly used in boats, tanks, and automotive applications. |
6xxx | Magnesium and silicon | Versatile alloys, with outstanding corrosion resistance, high strength, and excellent weldability, are used in structural applications. |
7xxx | Zinc | Aerospace, military, and sports equipment use high-strength alloys. |
8xxx | Other elements | It consists of various elements and is typically used for specialized applications such as packaging and electrical applications. |
The table above does not suggest that these are the only alloying metals/nonmetals in aluminum grades. Of course, there are more metal elements.
Normally, the “xxx” represent numbers. For example, in the 5xxx family, we may find aluminum 5052, which is suitable for metal stamping.
In general, several aluminum alloys are available for stamping. The specific needs of each application will determine the choice. Let’s look at some common aluminum grades you can use for metal stamping:
Aluminum Alloy | Characteristics | Application |
2024 Aluminum | – High strength – Excellent fatigue resistance – Good machinability – Poor corrosion resistance (typically requires coating) – Heat-treatable for added strength | – Aerospace components (aircraft wings, fuselage) – Military and defense applications – High-stress parts |
5052 Aluminum | – High strength among non-heat-treated alloys – Excellent fatigue resistance – Excellent corrosion resistance, especially in saltwater – Good workability | – Marine environments (boats, ships) – Automotive parts – Aircraft fuel tanks – Pressure vessels |
6061 Aluminum | – Heat-treatable – Excellent corrosion resistance – Good weldability – Versatile – Easily formable | – Structural applications (bridges, buildings) – Aerospace components – Automotive parts – Marine vessels |
6063 Aluminum | – Good strength – Excellent corrosion resistance – Excellent workability – Ideal for anodizing – Fairly excellent formability and weldability | – Architectural applications (window frames, doors) – Extrusions for structural purposes – Decorative uses |
7075 Aluminum | – High strength (one of the strongest aluminum alloys) – Excellent fatigue resistance – High resistance to stress corrosion cracking – Heat-treatable for strength | – Aerospace (aircraft structures, spacecraft) – Military applications (gun parts, ammunition) – Sports equipment |
Industries Using Aluminum Stamping Parts
Today, tons of industries rely on aluminum-stamping parts for a variety of applications. You can find stamped aluminum parts in many industries, including automotive, aerospace, medical, maritime, lighting, construction, electrical, and electronics.
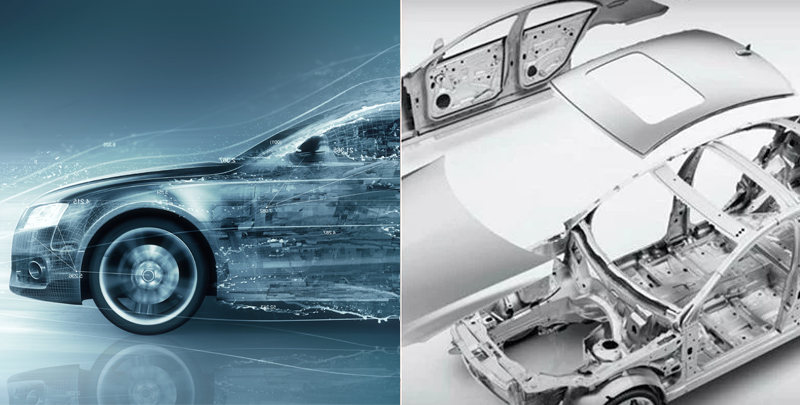
Aerospace Industry
In aircraft, weight is an important consideration. Aluminum’s lightweight properties, along with its strength, make it suitable for aviation components. Aluminum stamping elements, from the fuselage to the wings and internal mechanics, contribute to a lighter aircraft, improving fuel efficiency and performance.
Automotive Industry
The automotive industry is continually looking for methods to improve efficiency and safety. Automobile frames, panels, and engine components use aluminum-stamped parts. They give the necessary strength without adding weight, resulting in improved fuel economy and lower emissions. Automotive parts use aluminum stamping to create metal brackets for fender assemblies, door panels, airbags, instruments, and more.
Electronics
Aluminum’s outstanding electrical conductivity and heat dissipation properties make it ideal for electronic components. From electrical device housings to computer heat sinks, aluminum stamping provides performance and longevity in the electronics industry.
Medical equipment
Precision is essential in medical equipment; therefore aluminum stamping is critical. Surgical tools, diagnostic devices, and patient-handling equipment use lightweight, corrosion-resistant aluminum parts where hygiene and dependability are crucial.
Construction and architecture
Builders and architects use aluminum stamping to create components like frames, panels, and structural supports. Its corrosion resistance and visual appeal make it a popular choice for modern architectural designs.
Food and beverage industry
Aluminum’s non-toxic properties and corrosion resistance make it ideal for food and beverage containers and equipment. Its capacity to retain warmth is also useful in cooking and storage applications.
Conclusion
Aluminum stamping is a versatile metal production technology that incorporates numerous operations and techniques. The finest thing is that you may produce hundreds of parts based on your production requirements.
For firms and manufacturers trying to stay ahead, adopting aluminum metal stamping is a wise decision. If you’re ready to explore the possibilities that aluminum stamping has to offer, now is the time to take action. SogaWorks, as one of the most reliable aluminum stamping parts manufacturers, will assist you in achieving high-quality, precision-stamped aluminum components. Please contact us if you have any questions.