Type II and Type III are two classes of anodizing process. Anodizing is an electrochemical process used to increase the thickness of the natural oxide layer on parts made of metals like aluminum and titanium. Selecting the right anodizing type impacts a part’s surface hardness, corrosion resistance, aesthetics, and electrical insulation.
Anodizing is a process in which aluminum is placed in an electrolyte solution as an anode and an aluminum oxide film is formed on its surface by electrolytic reaction. The thickness of the anodized film of aluminum can reach tens to hundreds of microns. It has good mechanical properties and corrosion resistance, wear resistance, and weather resistance.
Principle of Anodizing
A chemical reaction occurs at the cathode:
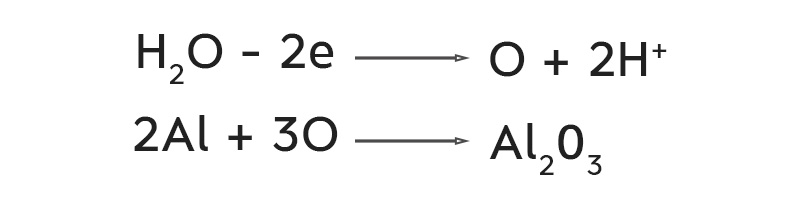
A chemical reaction occurs at the anode:
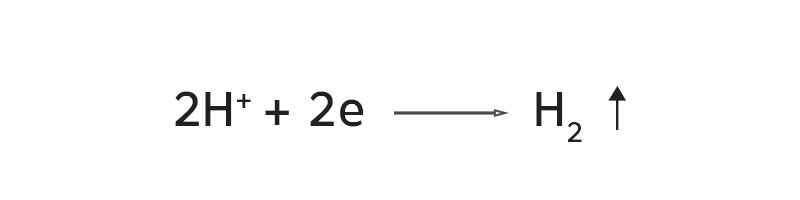
The acid chemically dissolves the aluminum and the formed oxide film, and the reaction is as follows:
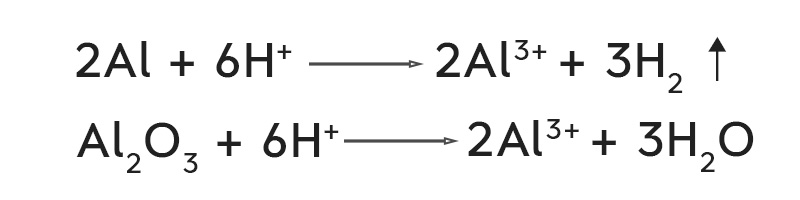
The formation and dissolution of the oxide film occur simultaneously. Initially, the growth of the film is faster than its dissolution, causing the film thickness to increase. As the thickness grows, its electrical resistance increases, which in turn slows the growth rate of the film until the dissolution rate equals the growth rate, at which point the film thickness stabilizes. The process can also be explained by the voltage-time curve during anodizing.
The anodizing voltage-time curve can be divided into three stages:
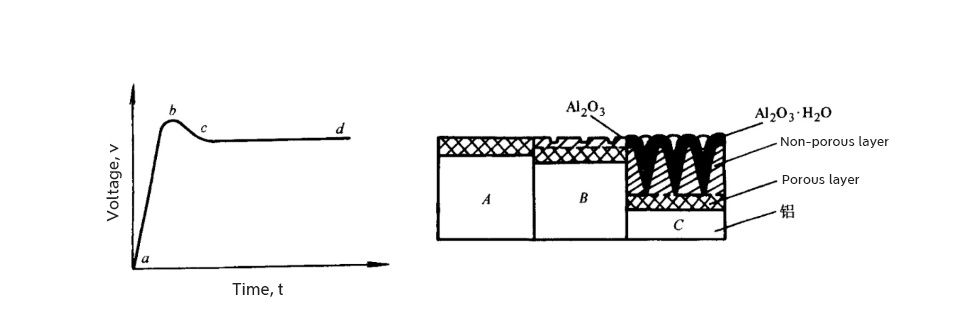
Stage 1: Formation of the Non-Porous Layer – In the segment from point ab, the voltage rises sharply from zero to maximum value within a few seconds. This voltage is called the critical voltage, which indicates the formation of a continuous, non-porous thin film on the anodized surface. The thickness of this non-porous layer is proportional to the forming voltage and inversely proportional to the dissolution rate of the oxide film in the electrolyte.
Stage 2: Formation of the Porous Layer – In the segment from point bc, the voltage drops slightly by 10%–15% after reaching its maximum value, which indicates that the non-porous layer begins to dissolve in the electrolyte, forming a porous layer.
Stage 3: Thickening of the Porous Layer – In the segment from point cd, after about 20 seconds of oxidation, the voltage rises gradually and steadily. This indicates that as the non-porous layer continues to dissolve to form the porous layer, a new non-porous layer is also forming. This means the porous layer continues to thicken, with both film formation and dissolution occurring at the base of each film cell. Once the rate of film formation and dissolution reaches dynamic equilibrium, further oxidation will not increase the thickness of the oxide film.
What is Type II anodizing?
Type II anodizing, also known as sulfuric acid anodizing, is a specific class of anodizing process that creates an oxide film with a thickness of 0.00010” and 0.0005” inches on the aluminum surface. The process involves immersing aluminum in a sulphuric acid electrolyte. When a direct current is applied to the electrolyte, oxygen atoms combine with aluminum atoms on the surface of the part to form an oxide film.
Benefits of Type II Anodizing
Type II anodizing provides many benefits, such as improved performance, durability, and visual appeal.
Improved corrosion resistance. Type II anodizing provides a protective oxide layer on the aluminum surface, it can protect aluminum from harsh environments such as moisture, chemicals, and saltwater. This improved corrosion resistance makes anodized aluminum an ideal choice for components exposed to mild or challenging environmental conditions.
Enhanced durability. As the oxide layer is generated by a chemical reaction, unlike paint and coatings, it bonds precisely to the aluminum surface and is not easy to flake off.
Aesthetic appeal. Type II anodizing produces a porous oxide layer, which makes it possible to absorb various colors. The anodized aluminum surface can maintain its color over time. These aesthetically pleasing finishes give designers more flexibility in aesthetics.
What is Type III anodizing?
Type III anodizing, also known as hardcoat anodizing, is another class of anodizing process that is similar to Type II but forms a thicker layer of oxide film. It is done at a lower temperature and higher voltage.
Benefits of Type III Anodizing
Types III anodizing has its advantages for critical components that must work under certain conditions.
Exceptional hardness. The oxide layer formed during Type III anodizing is much harder than Type II. It can reach a hardness of up to 300-500 HV, making it highly resistant to wear, abrasion, and scratching.
Put Your Custom Parts into Production Today!
Greater thermal shock resistance. Thicker oxide films can effectively buffer thermal expansion and contraction caused by temp. Changes and reduces cracking caused by thermal stress.
Good electrical resistance. Aluminum reacts with the acid in the electrolyte and produces aluminum oxide(Al2O3)during the anodizing process. Aluminum oxide is a hard and electrically resistant material. On the other hand, the aluminum oxide produced by Type III is much thicker and denser than Type II. Thus, the anodized aluminum parts have better electrical resistance.
Difference Between Type II and Type III Anodizing
There are several distinctions between Type II and Type III anodizing, some of the distinctions include:
Process parameters. Both anodization methods involve immersing aluminum as the anode in a sulfuric acid solution. The difference is that Type II uses higher temperatures and lower voltages, while Type III uses lower temperatures and higher voltages and produces a thicker oxide layer.
Oxide thickness. Type II anodizing forms a thinner oxide layer that is corrosion resistant, while Type III anodizing produces a thicker and denser oxide layer that improves hardness, wear resistance, and electrical insulation properties.
Corrosion resistance. Type III anodizing forms a much thicker and denser oxide layer than Type II, providing significantly improved corrosion resistance. The thicker oxide is like a barrier against aggressive chemicals, high humidity, and abrasive elements, which means Type III anodized aluminum has better corrosion resistance.
Hardness. Type III anodizing forms a much harder layer, significantly enhancing the hardness of the aluminum surface. This layer can reach hardness levels of 350-550 HV.
Dimension and tolerance. Type II anodizing typically adds only a thin coating thickness resulting in minimal dimensional change, Type III anodizing adds a thicker coating with greater dimensional change that may require adjustments to the design and tolerances.
Price. Type III anodizing is generally more expensive than Type II because it requires lower temperatures and higher voltages. This results in a thicker oxide layer formation and takes longer.
Below is a table showing the main distinctions between Type II and Type III anodizing.
Properties | Type II | Type III |
Process parameters | higher temp. lower voltage | lower temp. higher voltage |
Layer thickness, μm | 8-12 | 25-120 |
Hardness, HV | 250-350 | 350-550 |
Durability | Good | Excellent |
corrosion resistance | Good | Excellent |
Electrical resistance | Moderate | Good |
Price | Lower | Higher |
Conclusion
There are distinct advantages to both Type II and Type III anodizing. Type II anodizing exhibits special suitability in applications requiring adequate corrosion resistance, generally in less severe environments. On the other hand, Type III anodizing is ideal for more demanding situations, offering improved corrosion resistance and increased hardness. The difference between these two classes of anodizing process can be vital in choosing the right treatment for aluminum parts to enhance their performance and extend their lifespan.
At Sogaworks, we specialize in delivering high-quality, precision CNC machining services from China and anodizing services tailored to satisfy the needs of our clients. We offer a comprehensive range of surface finishing services, including Type II and Type III anodizing. With our advanced equipment and expert engineers, we deliver durable, reliable, and cost-effective solutions for customers in various industries.