The material chosen can influence the performance, lifespan, and efficiency of the final parts. Two metals, brass and stainless steel, have unique characteristics and different applications. This article will compare brass vs. stainless steel concerning several important attributes.
What is Brass?
Brass is an alloy metal of mainly copper (Cu) and zinc (Zn). It normally has good corrosion resistance, excellent machinability, and good electrical conductivity. Brass generally has a yellow-gold color, which makes it quite visually pleasing for applications in decoration. In particular, variations in the alloy composition of copper and zinc bring brass different physical and chemical properties to suit specific industrial needs.
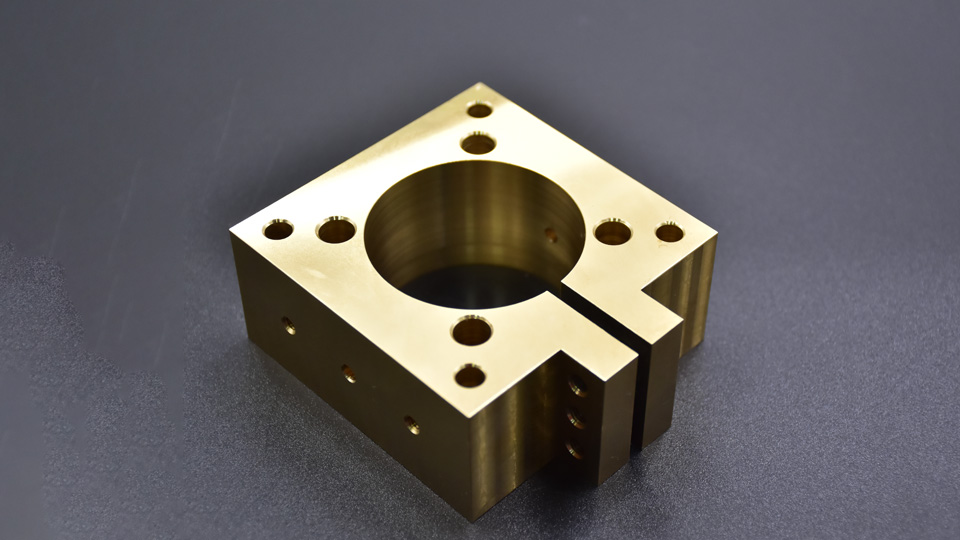
Advantages and disadvantages
- Good Machinability: Brass is easy to cut and shape, suitable for complex designs.
- Good Conductivity: It is well suited for electronic and heat exchange uses.
- Corrosion Resistance: It will develop an oxide layer on the surface, if dry, which is protective.
- Susceptible to Corrosion: Its resistance to corrosion decreases in humid or chlorinated environments hence, causing stress corrosion cracking.
- Low Strength: Brass has very low strength and hardness compared to stainless steel.
Classification and Alloy Grades
Brass can be categorized based on zinc content and other alloying elements. The main types include:
- Brass C26000 (Commercial Brass): General-purpose alloy with good machinability.
- Brass C28000 (Lead Brass): Contains lead, improving machinability for cutting operations.
- Brass C21000 (Lead Copper): Mostly for electrical and heat exchange applications.
What is Stainless Steel?
Stainless steel is an alloy with a minimum of 10.5% chromium content, widely used for its excellent corrosion resistance and strength. The addition of chromium allows the formation of a protective chromium oxide layer on the surface of stainless steel when it comes into contact with moisture and oxygen, which prevents further oxidation of the metal and subsequent corrosion. Based on composition and microstructure, there are several types of stainless steels: austenitic, ferritic, and martensitic stainless steels, each having different strengths, toughness, and corrosion resistance.
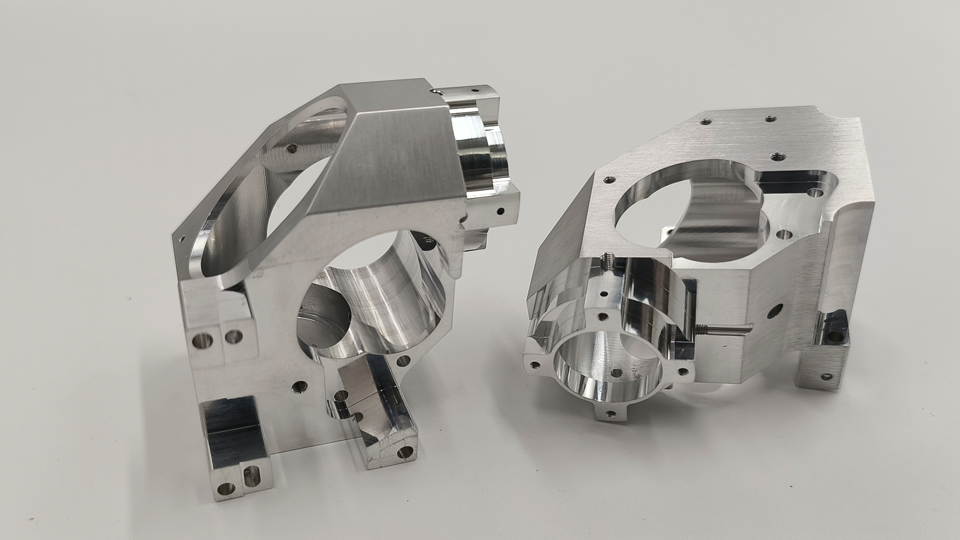
Advantages and disadvantages
- Excellent Corrosion Resistance: The addition of chromium allows stainless steel to form a thin protective layer in humid and oxygen-rich environments.
- High strength and hardness: This material is much stronger compared to brass and can withstand heavy loads.
- High-Temperature Resistance: It has high-temperature resistance since it has a relatively high melting point.
- Poor Machinability: Compared to brass, stainless steel is hard to machine and may require special tools.
- High Cost: Prices of alloying elements like chromium and nickel make stainless steel relatively costly.
Classification and Alloy Grades
- Stainless steel may be categorized into several classes based on their composition and microstructure.
- Austenitic Stainless Steel (e.g., 18-8 and 316): Offers good toughness and corrosion resistance for a wide range of applications.
- Ferritic Stainless Steel (e.g., 430): A magnetic material with moderate corrosion resistance, often used in kitchen equipment.
- Martensitic Stainless Steel (e.g., 410): High strength and wear resistance but with lower corrosion resistance; typical applications include knives and tools.
Read more: Types of Stainless Steel: Austenite vs. Martensite vs. Ferrite
Brass vs. Stainless Steel: Property Comparison
The table shows differences in composite and properties between brass vs. stainless steel.
Property | Brass | Stainless Steel |
Composition | Copper and Zinc (Cu-Zn) | Iron, Chromium, Nickel, etc. |
Tensile Strength (MPa) | 340-470 | 500-1100 |
Yield Strength (MPa) | 125-310 | 210-820 |
Density (g/cm³) | 8.5 | 8.0 |
Thermal Conductivity (W/m-K) | 115 | 15-25 |
Machinability, % | 100% | 40%-75% |
Electrical Conductivity (10^6 S/m) | 15.9 | 1.32 |
Melting Point (°C) | 900-940 | 1400-1530 |
Cost | Moderate | Higher |
Magnetism | Non-magnetic | Varies by type (some are magnetic) |
Corrosion Resistance | Good | Excellent |
Brass vs. Stainless Steel: Composition
Brass is principally an alloy of copper and zinc, with other elements (such as tin and lead) possibly added to improve machinability. Stainless steel, by contrast, contains iron, chromium, nickel, and other alloying elements, the variations in composition allow stainless steel to display different characteristics in differing applications. Knowing these compositions can help with the selection of the right materials at the design stage.
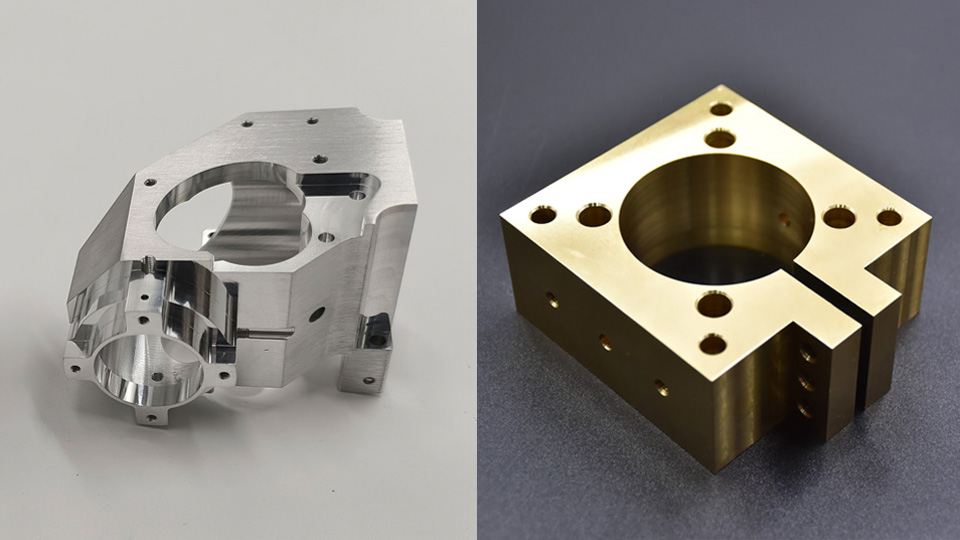
Brass vs. Stainless Steel: Corrosion Resistance
Brass generally shows good corrosion resistance, but its performance varies in different environments. When exposed to air, a thin layer of oxide can be formed on brass, which helps to prevent further oxidation. In humid or acid environments, however, brass may corrode, especially in the presence of chlorides, which may cause stress corrosion cracking.
Stainless steel has excellent corrosion resistance, and this is mainly due to the composition of chromium. this element enables stainless steel to form a dense chromium oxide layer that protects oxygen and moisture from coming into contact with the metallic substrate, hence preventing rust and corrosion. This protective layer is self-healing, if some minor scratches or damages occur, the material quickly restores itself. Stainless steel performs well in such aggressive environments as marine settings, chemical plants, and humid climates by being able to resist the corrosive action of many chemicals, including acids, bases, and chlorides.
Brass vs. Stainless Steel: Strength
Tensile strength defines the amount of “pull” a material can withstand. The higher the tensile strength, the greater the load a material can carry without rupture. Stainless steel has a tensile strength of 500-1100 MPa, much stronger than brass with a tensile strength of 340-470 MPa. This makes stainless steel ideal for high-stress applications, such as in construction and heavy-duty machinery. The higher tensile strength allows for thinner materials under the same load, reducing overall weight with enhanced flexibility.

Yield strength is the amount of stress required to cause a material to start deforming plastically. Brass has a relatively lower yield strength, 125-310 MPa. That means it will deform under large loads. In contrast, stainless steel has a higher yield strength in the range of 210 to 820 MPa. It could retain its shape and endure stronger conditions. This makes stainless steel ideal for strict structural requirements, specifically in support frameworks of skyscrapers or pressure vessels.
Brass vs. Stainless Steel: Durability
In general, stainless steel is considered to have superior durability and longevity compared to brass due to its excellent corrosion resistance from chromium content, greater strength and toughness, and minimal maintenance requirements. While brass is composed primarily of copper and zinc, is more susceptible to tarnishing and corrosion, especially in humid or outdoor environments, it may require more upkeep to maintain its appearance. Stainless steel excels in challenging conditions. The choice between the two materials should be guided by the specific needs of the application and the environmental factors involved.
Brass vs. Stainless steel: Weight
At 8.5 g/cm³, brass has a higher density compared to stainless steel with a density of 8.0 g/cm³. While being a little heavier, this weight factor brings stability to a brass component in some instances. In addition, due to its density, brass enhances heat transfer when applied in certain aspects of heat exchangers.
Make Your Idea Take Shape!
Brass vs. Stainless Steel: Thermal Conductivity
Thermal conductivity measures how well a material conducts heat. Brass performs well in this regard (115 W/m-K), making it ideal for heat exchangers, electronic components, and kitchen appliances. Stainless steel, with lower thermal conductivity (15-25 W/m-K), limits its thermal management capabilities in high-temperature applications. However, this low thermal conductivity can help retain heat, making stainless steel suitable for insulation or heat source contact parts.
Brass vs. Stainless Steel: Machinability
Brass has very good machinability (100%) in cutting, shaping, and processing to meet requirements under diversified design specifications. This feature makes brass perfect in precision components such as gears and shafts. On the contrary, stainless steel has lower machinability (40-75%) and needs special tools and techniques for processing. Such a difference requires close consideration of the manufacturing cost and processing difficulties when choosing materials. Both materials are common materials for CNC machining.
Brass vs. Stainless Steel: Electrical Conductivity
In terms of electrical conductivity, brass noticeably outperforms stainless steel: 15.9 × 106 S/m versus 1.32 × 106 S/m. The electrical conductivity of brass is nearly 15 times of stainless steel. This makes brass preferable for electrical contacts and connectors where low resistance is vital. When it comes to corrosion resistance, stainless steel has no peer, but its relatively lower conductivity may limit its application in electrical circuits.
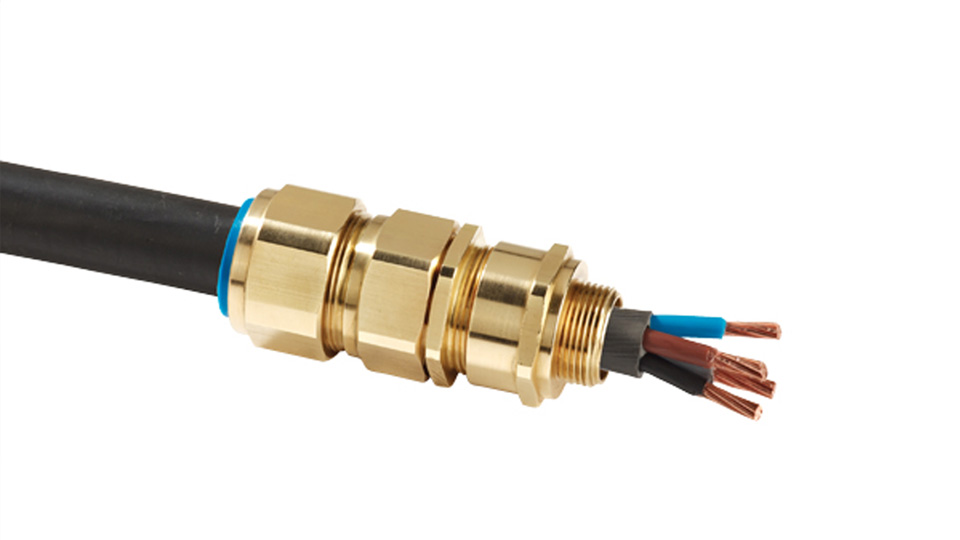
Brass vs. Stainless Steel: Melting Point
Brass will melt between 900-940°C, while stainless steel can withstand much higher temperatures of 1400-1530°C. The increased melting point of stainless steel helps to maintain structural integrity in high-temperature setups. It is suitable for working under high-heat applications such as boilers, reactors, and high-temperature piping. This characteristic also enhances stainless steel’s performance in welding and thermal processing.
Brass vs. Stainless Steel: Price
Brass is moderately priced, on the other hand, stainless steel will generally be more expensive due to the higher cost of alloying elements, such as chromium and nickel, and complex production processes. Although higher costs can weigh heavily on project budgets, the qualities of stainless steel make it a high-ROI investment for applications that demand strength and corrosion resistance.
Brass vs. Stainless Steel: Magnetism
Brass is non-magnetic and hence can be used in environments where magnetic interference must be avoided. The magnetism of stainless steel depends upon the type; for example, ferritic stainless steel is usually magnetic, and most austenitic and martensite stainless steel is non-magnetic. This property is very relevant to electrical and electronic applications.
Conclusion
The comparison between brass and stainless steel, concerning properties, is as follows: brass is an alloy of copper and zinc, containing good machinability and electrical conductivity, though lower strength and susceptibility to corrode easily, hence requiring more maintenance under moist conditions. On the other hand, stainless steel contains at least 10.5% chromium for better resistance to corrosion and higher strength; thus, it is more suitable for demanding environments and requires less maintenance, though it is harder to machine and generally more expensive.
The choice between brass and stainless steel is to be made bearing in mind application-specific requirements, which include environmental conditions, strength needs, and budget considerations. Knowing these properties helps one make informed decisions for optimum performance.