Titanium and its alloys are known to us for their high strength, durability and corrosion resistance. It is widely used in the aerospace and medical industry. We have benefited a lot from titanium parts, but there are still many limitations in titanium CNC machining. This article will discuss what is titanium, common titanium alloys, and titanium CNC machining.
What is Titanium?
Titanium is a metal element. The atomic number of titanium in the periodic table of elements is 22 (4th period, NB group). It has a silver-white metallic luster and has many excellent properties such as high melting point, low density, high strength, and good flexibility. It is important for industrial materials.
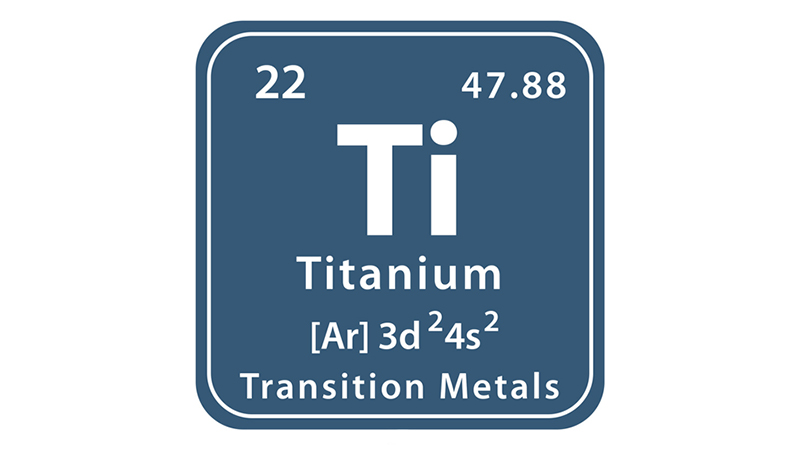
Commercially Pure Titanium
Commercially pure titanium contains a minimum of 99% pure titanium. Four commercially pure types of titanium, namely Grades 1 – 4.
Grade 1: The softest and most ductile of these grades. It possesses the greatest formability, excellent corrosion resistance, and high impact toughness.
Grade 2: It shares many of the same qualities as Grade 1 titanium, but it is slightly stronger.
Grade 3: It is stronger than Grades 1 and 2, similar in ductility, and only slightly less formable.
Grade 4: The strongest of the four grades. It possesses corrosion resistance, good formability, and weldability.
Mechanical properties of commercially pure titanium
Property | Grade 1 | Grade 2 | Grade 3 | Grade 4 |
Tensile Strength (MPa) | 240 | 345 | 450 | 550 |
Yield Strength (MPa) | 310 | 450 | 550 | 655 |
Elongation at break(%) | 24 | 20 | 18 | 15 |
Titanium Alloys
Titanium has two phases, namely the α phase and the β phase. According to the different matrix structures obtained under room temperature conditions, titanium alloys can be divided into the following three categories: titanium α, titanium β, and titanium a-β.
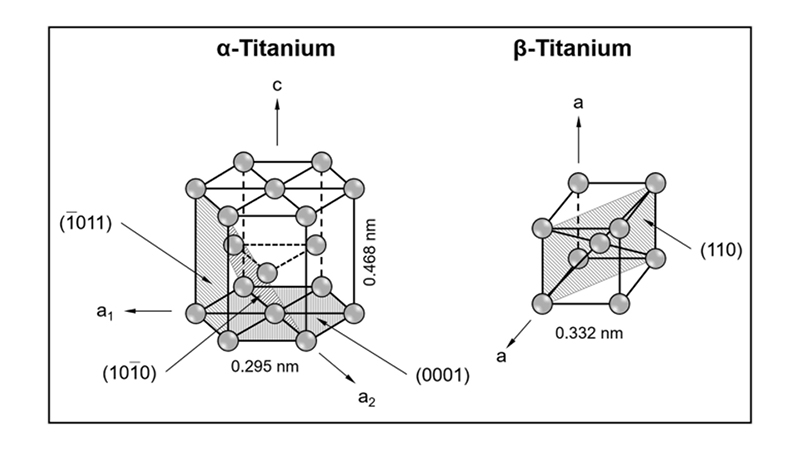
Examples of titanium
Catagory | Examples |
Titanium α | Commercially pure titanium(Grade 1 – 4) Ti-5Al-2.5Sn (Grade 6) Ti-0.2Pd(Grade 7) |
Titanium β | Ti-5Mo-5V-8Cr-2Al Ti-10Mo-8V-1Fe-3.5Al Ti-32Mo |
Titanium a-β | Ti-6Al-4V (Grade 5) Ti-4Al-4Mo-4Sn-0.5Si |
Why is Titanium Difficult To Process?
Titanium alloy has the advantages of being lightweight and high strength. However, the difficulty of processing titanium alloy has always troubled engineers and technicians.
Low heat conductivity. Most titanium alloys have extremely low thermal conductivity, which is only 1/7 of steel, 1/16 of aluminum, and 1/25 of copper. Therefore, the heat generated during cutting materials is not easy to dissipate and is concentrated in the cutting area. This can easily lead to rapid wear and cracking of the tool and generate chip accumulation, shortening the tool’s life.
Elastic deformation of titanium. The elastic modulus of titanium alloy is relatively low. For example, the elastic modulus of TC4 is only 110 GPa, while that of 45 steel is 210 GPa, and that of 303, 304, 316, and other stainless steels is also around 200 GPa. When machining titanium alloy, elastic deformation is easy to occur, especially when machining thin-walled or annular parts.
Vibration. The elasticity of titanium alloys may be beneficial from part performance, but it becomes the main cause of vibration during cutting. The vibration generated by machining titanium alloys is 10 times that of steel. Since the cutting heat is concentrated in the cutting part, it will produce zigzag chips, causing cutting power fluctuations.
Titanium CNC Machining Process
Titanium alloy is one of the most challenging metals to machine due to its great strength and poor heat conduction. Regardless, you can CNC machining titanium using a multitude of processes.
CNC Milling
CNC milling creates the desired shape from a workpiece by removing material using rotary tools. It is important to consider the various properties of titanium and take the appropriate measures to mill titanium workpieces. The high strength and hardness of titanium require tough milling tools, such as those made from carbide and hardened steel.
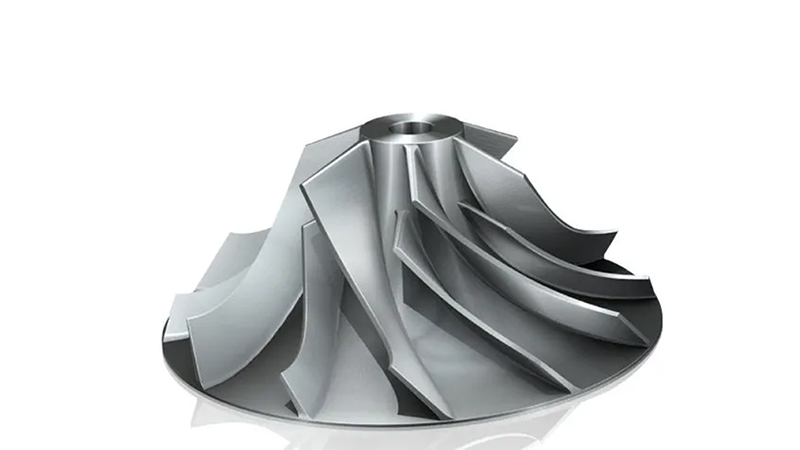
CNC Turning
CNC turning creates the desired shape from a workpiece by rotating it on a spindle to form precise cylindrical shapes. Good cutting performance can be achieved when turning titanium alloys with high-speed steel or tungsten carbide tools. Carbide tools are sensitive to vibration and therefore require a rigid fixture.
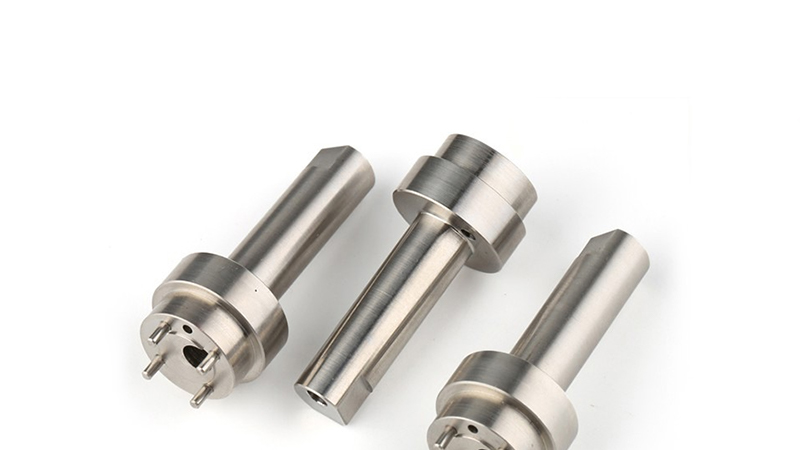
Waterjet Cutting
Water jet cutting uses highly pressurized water to cut and does not generate high temperatures, so it will not cause material property changes due to thermal stress or deformation. However, when the titanium metal plate is thicker, the surface finish after processing is lower, and additional post-processing is required to achieve a higher surface finish.

Tips for Machining Titanium Parts
Titanium alloy has been proven to have high strength, durability and corrosion resistance. It is widely used in aerospace prototyping applications. Despite this, there are still some difficulties in machining titanium alloy; therefore, special considerations are required to ensure efficient and safe machining.
Choose the right cutting tools: Use cutting tools designed specifically for titanium, such as carbide or diamond-coated tools. These tools have a higher heat resistance and can withstand the high cutting forces required for titanium machining.
Optimize cutting parameters: Adjust cutting parameters such as speed, feed and depth of cut to minimize heat generation and prevent work hardening. Generally, slower cutting speeds and higher feed rates are recommended when machining titanium.
Use coolant: Use a high-pressure coolant system to dissipate heat and reduce tool wear. Coolant can also help prevent work hardening by reducing the temperature of the cutting edge.
Setup rigidity: Make sure your machine, workpiece and tool setup are as rigid as possible to minimize vibration and tool deflection. This can be achieved through proper fixtures, tool selection and machine maintenance.
Minimize tool engagement: Use techniques such as trochoidal milling or high-efficiency milling to minimize tool engagement and reduce heat generation. These techniques involve using a small radial depth of cut while maintaining a constant chip thickness, which allows for faster feed rates and better thermal management.
Surface Finishes For Titanium Parts
Titanium still has some shortcomings, such as low wear resistance, oxidation at high temperatures, and more. To further improve the wear and oxidation resistance or other characteristics of titanium, it must undergo a few surface finishes. Most surface finish options can be applied to titanium. The following lists some of the common surface finishes for this metal:
Bead blasting: using fine particles shot at high speed to clean and texture the titanium surface, giving it a smooth, matte finish.
Anodizing: Increasing the thickness of the natural oxide layer on titanium, offering enhanced corrosion resistance and additional vibrant colors.
Powder coating: applying a dry, powdery substance to the titanium surface to form a durable, protective layer.
Polishing: smoothing the titanium surface to a shiny, mirror-like finish.
Chroming: Coating titanium with a thin layer of chromium with a shiny, reflective surface.
Brushing: Creating fine, parallel lines on the titanium surface and offering a textured finish.
Titanium CNC Machining Service at SogaWorks
SogaWorks is an expert in rapid prototyping services, we have strong expertise in titanium CNC machining service. We provide high-quality CNC titanium machining parts at affordable prices. With 5-axis CNC machining capabilities and high-precision machine tools, our team of engineers is ready to accept and process your projects in the shortest time, thus reducing the time to get your product on the market.