Statista (2022 data) estimates that CNC machines account for over 70% of precision machining processes in industrialized nations, with manual machining relegated to niche applications. This is not unexpected at all because of the precision, control way and production quality.
Still, I found some sample orders required manual machining. So this text will start from one of our real cases, and then move to the introduction of both CNC and hand machining. Absolutely, after knowing these, we will list the features, pros and cons for ultimate comparison between CNC machining vs. manual machining. Finally, we mention the combination of CNC and manual methods. And then we show brief answers for frequently asked questions online at the end of this blog. Now let’s dive into it.
One Special Case of Our Orders
Last month, Johnson placed an order with us for high-precision gyroscope rotors, which will be used in their navigation system research project. And we require that their surface roughness Ra should be lower than 0.008μm. After CNC machining in the factory, we heard that the Ra can not reach the standard, though the operator is really careful. So finally, we had to adopt manual polishing to eliminate the residual stress layer from CNC machining through a layer-by-layer material removal approach. This time, the report showed good data on every parameter including the Ra. And Johnson is satisfied with the elements. You see? To some degree, manual machines aren’t useless.
Here, some people may be confused: how much does CNC machining vs. manual machining really count? Great, I think this question is good. And, we have to know what they are before comparison.
What is CNC Machining?
In the early 1950s, a groundbreaking collaboration between Parsons’ research group and MIT’s Servomechanisms Laboratory led to the creation of the world’s first Numerical Control (NC) machine tool prototype. This pioneering system employed digital signals to dictate the precise motion paths of cutting tools. Undoubtedly, this marks a significant leap toward fully automated manufacturing processes. Over the subsequent decade, through relentless technological advancements and iterative improvements, this early NC technology matured into the sophisticated Computer Numerical Control (CNC) machining systems that we see today.
Computer Numerical Control (CNC) machining, abbreviated as CNC machining, is an advanced manufacturing method. As its full name shows, CNC operations are entirely dependent on computer programs in the form of G codes. This contributes to its ability to handle complex geometries and complex designs. No matter CNC milling, CNC turning or drilling, it performs precisely, stably in a cost-effective way, especially when the product quantities are large.
Some people may also hear about 3+2 CNC. It is talking about the CNC multi-axis. In common, its multi-axis can be A and C axis working together. Or, the machine can only have A or C axes. Even, there can be no any A or C axis, just a basic X-Y-Z stage. For example, we refer to CNC machines that “combine three linear axes (X, Y, Z) with two rotational axes (e.g., A, C)” as 3+2 CNC machines or 5-axis CNC machines. And, those “integrating three linear axes (X, Y, Z) with a single rotational axis (e.g., A or C)” are termed 4-axis CNC machines.
In contrast, three-axis CNC machines exclusively feature X, Y, and Z linear axes. These represent the most fundamental and widely used configuration due to their simple structural design and relatively lower cost. So, they are only capable of handling basic component machining tasks, such as common flat surface operations and hole-series machining.
Types of CNC Machining
CNC Milling
CNC milling is a subtractive manufacturing technique that merges the principles of traditional milling with cutting-edge Computer Numerical Control (CNC) automation. This process contains a high-speed rotating cutting tool to precisely carve away material from a solid workpiece—whether metal, plastic, wood, or composite—to produce intricate components and finished products.
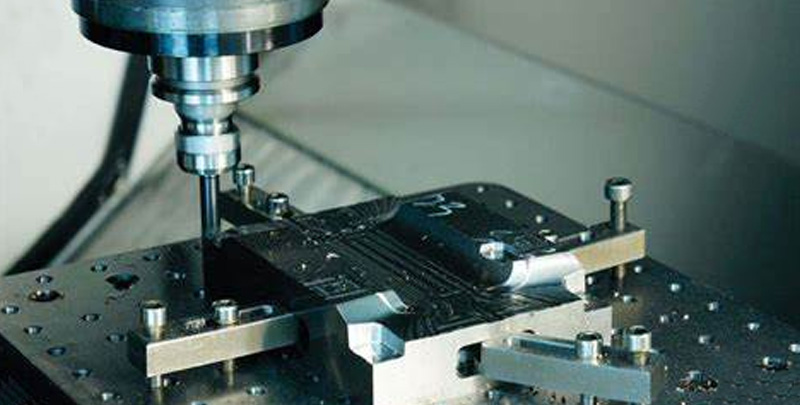
CNC Lathes
Unlike CNC milling used for machining grooves and gears, CNC lathes are primarily designed for manufacturing rotational parts such as shafts, sleeves, disks, and threads. Their working principle involves rotating the workpiece while keeping the cutting tool stationary or moving linearly to perform operations like turning, boring, facing, and threading. So we can easily imagine the reason why it is good at rotational parts.
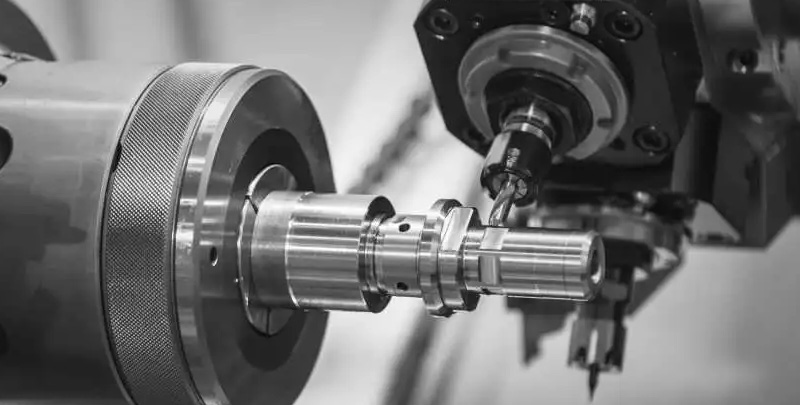
Additionally, CNC lathes generally cost less than CNC milling machines. Due to their multi-axis machining capabilities and complex motion control, they achieve relatively higher production efficiency. Combined with their high machining accuracy, CNC lathes are perfect for high-precision manufacturing of traditional cylindrical and conical components.
EDM
However, not all the components are as regular as disks and threads. So how complex, ultra-hard components like aerospace nozzles or turbine blades are crafted with such perfection? Meet Electrical Discharge Machining (EDM) works. It is a fascinating non-contact machining process that meticulously shapes materials using carefully controlled electrical sparks. Hardened steel, tungsten carbide, or exotic alloys—EDM fearlessly carves delicate cooling holes in jet engine blades, crafts labyrinthine cavities for injection molds, or pierces oddly shaped fuel nozzles for spacecraft. Therefore, it’s perfect for complex geometries, thin walls, and ultra-precise (±0.005mm) parts without mechanical stress.
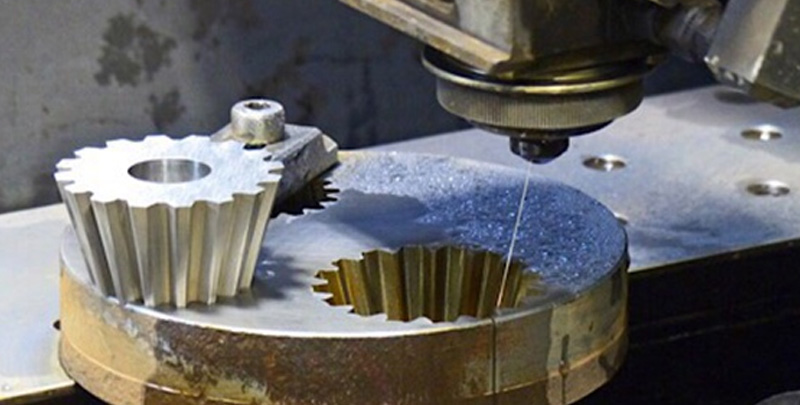
Comparison Among CNC Milling, Lathes and EDM
CNC milling , Lathes and EDM are CNC machining which is based on computing. And we make a conclusive table for your clarifying.
CNC Milling | CNC Lathe | EDM | |
Production Efficiency | High | High | Low to Moderate |
Precision | ±0.005 mm | ±0.005 mm | ±0.002 mm |
Machine Cost | Medium to High | Medium | High |
Scrap Rate | Moderate | Low (consistent turning) | Low |
Material Compatibility | Metals, plastics, and composites | Metals, plastics | Conductive materials |
Best Suited Parts | 3D contours, pockets, slots | Rotational/symmetrical parts | Intricate details, hardened materials |
What is Manual Machining?
Largely different from CNC machining, manual machining is a crafting process that involves shaping raw materials, such as metals, into desired dimensions and forms through hand-operated tools like lathes, drill presses, and portable milling machines. Commonly, it serves as an extension of artisanal craftsmanship, blending human creativity with specialized equipment. For instance, crafting custom-fitted aircraft engine components with intricate tolerances exemplifies manual machining’s irreplaceable value.
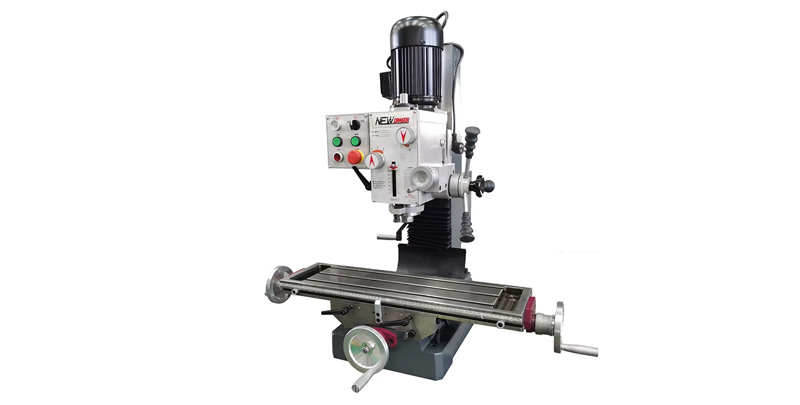
Case Study Between CNC Machining Vs. Manual Machining
In the following part, we tracked the CNC machining and hand machining processes of two similar gear shafts for an agricultural machine. And we reviewed the differences and advantages and disadvantages of the two from multiple perspectives.
Manual Machining for Agricultural Gear Shafts
Process Review
The operators select medium-carbon steel (1045 steel) as raw material and cut it into the proper length by a power hacksaw and a horizontal bandsaw. Meanwhile, he calculated key parameters with a slide rule. As my record showed, he should use the formula to get the Pitch Diameter (D) and then align the module value on the slide rule’s C scale with the number of teeth on the D scale. Also, he had to calculate the cutting speed (V) and set \( D \) on the slide rule’s outer scale against RPM on the inner scale. Only after finishing the calculation can he start the lathe.
Well, then he should mount the workpiece in a 3-jaw chuck and perform rough turning to remove excess material. That sounds difficult. Then he should also use carbide tooling for finish turning to achieve a 0.05 mm tolerance.
Gear cutting still involves manual tools, a milling machine. Installation, index calculation and index plate adjustment are all done by his hands.
Finally, he hardened the gear teeth via induction hardening to achieve 50–55 HRC.
Our Review Table
Issue | Score/Value |
Surface Roughness | 8/10 |
Produce Speed(Pics/Hour) | 2 |
Operator Experience(Years) | 12 |
Operator Proficiency Leve | 9/10 |
Final Result Test
Para. | Standard | Test Result | Pass/Fail |
Surface Roughness (Ra) | ≤1.6 μm | 1.8 μm | Fail |
Rockwell Hardness Test (HRC) | 50–55 | 52 | Pass |
External Diameter Tolerance | ±0.05 mm | +0.03 mm | Pass |
Cumulative Pitch Error | ≤0.02 mm | 0.015 mm | Pass |
Coaxiality Error | ≤0.01 mm | 0.008 mm | Pass |
CNC Machining for Agricultural Gear Shafts
Process Review
When it comes to CNC machining process, it would be more automatic. The operator first used SolidWorks and AutoCAD to design the gear shaft, defining parameters, including module (m), number of teeth (z), pressure angle (α), and helix angle (β). At the same time, he calculated the geometry including pitch diameter, root diameter and cutting depth. Then use a gear parameter calculator or formulas to verify dimensions.
The next step is the key process, CAM programming & toolpath simulation. That means the operators generate G-code by CAM software and input the parameters. After that, CNC machining started.
From working holding to rough turning, to gear hobbing, grinding and quality inspection, it seems quicker than manual machining.
Our Review Table
Issue | Score/Value |
Surface Roughness | 8/10 |
Produce Speed(Pics/Hour) | 5 |
Operator Experience(Years) | 5 |
Operator Proficiency Leve | 9/10 |
Final Result Test
Para. | Standard | Test Result | Pass/Fail |
Surface Roughness (Ra) | ≤1.6 μm | 0.8 μm | Pass |
Rockwell Hardness Test (HRC) | 58-62 | 60 | Pass |
Tooth Profile accuracy | ±0.02mm | +0.015mm | Pass |
Tooth Tip Radial Runout | ≤0.03mm | 0.002 mm | Pass |
Module Uniformity | m=3±0.01 | m=3.005 | Pass |
Comparison Between CNC Machining vs. Manual Machining
We also summed up the features comparison after reviewing the above two cases.
Precision, Repeatability, and Quality Assurance
As our expectation, CNC machining is in high precision and repeatability. No wonder the final product of CNC did better in Ra than that of manual machining. If we think deeply, it is that the nature of CNC operations ensures minimal deviation from design specifications, with computer-controlled movements eliminating human error.
Production Scale and Cost Efficiency
From the review table, one-person-labour can produce 5 pieces per hour. Just because it needs minimal human intervention during the process according to our observation. Conversely, manual machining is optimized for low-to-medium production volumes. As my record, one-person-labor can only produce 2 pieces per hour. Thus, CNC machines suit mass production with low labour cost and less time, while the manual way is suitable for one or two samples making.
Skill Sets and Operational Requirements
CNC operators know more about computing and automation manufacturing, while the manual operators are skilled at hands-on techniques.
The CNC operator in our review is good at setting integrating programming, technical troubleshooting, and machine operation. He has five years of experience in this job.
And, the operator manual machining is sophisticated in cutting tools, material properties, and hands-on techniques. Further, he can interpret technical drawings, select appropriate tools, and manually control cutting parameters, a process that relies on intuitive judgment honed through 12 years of experience.
Quality Risk Mitigation and Adaptability
CNC’s inherent repeatability reduces quality risks in high-consistency applications, such as medical device manufacturing, where uniformity is non-negotiable. The absence of operator-to-operator variability ensures each cycle adheres strictly to programmed parameters, minimizing defects.
Manual machining, however, necessitates proactive quality control to offset its variability. For example, tool wear or slight hand tremors may introduce deviations, necessitating post-process inspections.
Disadvantages and Advantages of CNC machining vs. Manual Machining
From the above review, we further make a conclusion about the pros and cons of CNC machining vs. Manual machining as follows.
CNC Machining | Manual Machining | |
Interchangeability & Precision of Finished Products | High | Requires Custom Pairing |
Production Efficiency | High | Low |
Applicable Materials | Metals/Plastics/Composite Materials | Metals/ABS/Woods/G10 |
Waste Generation | Less | More |
Labor Costs | Low | High |
Operational Safety | High | Low |
Maintenance Difficulty | High | Low |
Machine Costs | High | Low |
Real-time Adjustments | Difficult | Easy |
Best Suited For | Mass Production | Single/Small Batch Production |
Advantages of CNC Machining
1. Production Speed
CNC machines have never been tired. It can work without any break time as long as computing and the preparation are ready. This saves lots of time to produce more products. Secondly, due to its automation, one operator is allowed to look after several machines to produce several products at the same time. This is the other key reason for its good production speed.
2. Repeatability
Repeatability brings products with high precision and good interchangeability. Since the action of CNC machining strongly relies on computing code, it can not introduce any error differing from the code direction. Besides, the final product is completely the same as each other, so users can replace the component with another one in the same batch.
3. Lower Labor Cost
Several CNC machining processes can be operated by only one person at the same time. That means it saves several times in labor costs.
4. Complex Designs
The CAD (Computer-Aided Design)/CAM (Computer-Aided Manufacturing) software of CNC machines enables manufacturers to produce complex designs, including multi-axis contours and curves.
Disadvantages of CNC Machining
1. High Initial Costs
The initial investment in CNC machines is higher because both the equipment and installation costs are high. A CNC machine is large and contains lots of automatic parts. Even the machine has to carry high-tech modules to grasp the code. Usually, only professional personnel can install this large and complex machine, leading to an installation fee.
2. High Maintenance Cost
Although the possibility of failure when using these machines is lower, if a failure occurs, only highly skilled professionals can solve the problem. And, the installation fee is also required.
3. Programming Skills
Because CNC machines rely on specific codes, you need a skilled programmer to create and set up the codes. They should be well educated through professional training.
Advantages of Manual Machining
1. Lower Cost
The initial investment cost of manual machines is lower. Without high-tech, the tool and machines of hand machining are not so expensive. Due to its affordability, manual machines are suitable for small manufacturers with limited budgets.
2. No Need for Programming
If there is no worker doing well in programming, hand machining is perfect for the situation.
3. Easy Maintenance
Because of the simple construction of the manual machining tool, it is easier to maintain in case of any fault tool. Also, the maintenance cost would be cheap.
4. Better Customizability
Manual milling machines are usually used for one-time projects. Because it is handled by human instead of code direction, these machines have great flexibility and adaptability in the production process.
Disadvantages of Manual Machining
1. Slow Production Speed
Manual machining requires more human labour. One operator can only take care of one product. They should control the precision by hand. This takes a lot of time and energy. And, humans need to not only take breaks during work but also take leave during traditional holidays. During this time, this is no production in the manual machining workshop.
2. High Error Rate Due to Human Factors
Due to the high reliance on operators, manual machines lack precision. In other words, it is possible to produce unqualified final products. And the risk of rework would be higher.
3. High Dependence on Labor Skills
The operator should be sophisticated in manual technique, which closely affects the efficiency and product quality. However, learning these necessary skills requires not only knowledge training but also years of practical experience. That’s not an easy thing.
How About the Hybrid of CNC Machining and Manual Machining?
The Hybrid of CNC machining and manual work means using computer-controlled machines for precision tasks while adding human skills for finishing or adjustments, creating a balanced approach to manufacturing. For example, a CNC machine cuts a metal part with high accuracy, then a worker manually polishes its edges for smoothness, and finally, they inspect and tweak details like holes or threads to ensure perfection.
This hybrid method works well in custom projects like crafting intricate jewelry, where CNC creates the base shape and artisans add hand-engraved patterns, or in repairing vintage car engines by machining new parts with CNC and manually fitting them to old components. Additionally, it’s ideal for prototyping gadgets, combining fast CNC production of plastic casings with manual assembly of tiny electronic parts, saving time while maintaining quality and flexibility.
Conclusion
In the end, I would like to give 70% importance to CNC machining and 30% to manual machining.
FAQs
1. Where Should We Use Manual Machining?
Manual machining is ideal when CNC machines are busy with urgent small batches. Also, it’s essential for specialized tasks beyond standard CNC setups, such as slant bed configurations requiring unique tool angles.
2. What Factors Should We Consider Before Choosing CNC or Manual Machining?
When choosing between CNC and manual machining, consider part complexity, budget, volume, and time: CNC excels for intricate designs, tight tolerances, and large batches despite higher upfront costs, while manual suits simple geometries, low volumes, and limited budgets but demands more labor and time. Prioritize precision and efficiency for complex, high-volume projects with CNC, whereas manual offers flexibility for simpler, small-scale tasks. If you are still not sure how to choose CNC or manual machining, please feel free to contact us.
3. What Are the Applications of CNC Machining Vs. Manual Machining?
CNC machining is ideal for high-volume production like automotive parts, precise prototyping, and rapid tooling with tough materials. And, manual machining suits small projects, artistic customization, and urgent repairs due to its flexibility and no coding needs.