Overview of Sheet Metal Bending
Bending is a process used to deform metal using force and bend it in the desired direction to create a specific shape. It is done using rolling machines and press brakes. There are several types of rolling machines, and they can roll sheet metal into different shapes within certain ranges.
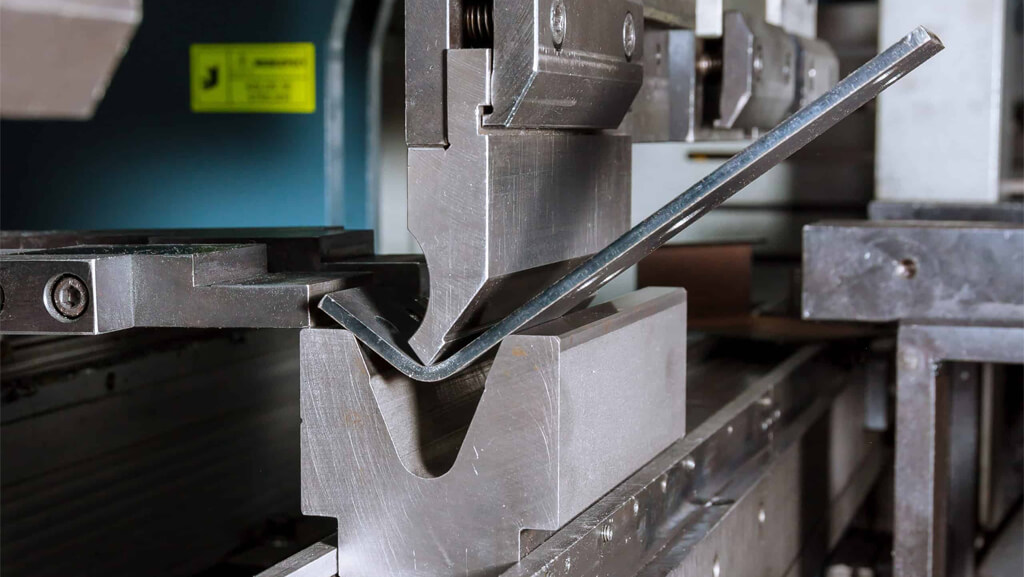
There are various sheet bending methods:
- V-bending: This is where the bending tool provides the force needed to bend the metal material (placed on top of the V-die) at the desired angles. This technique can bend steel plates with no change in their positions.
- Roll bending: This technique bends steel sheets into curved forms or rolls. It employs the press brake and a hydraulic press and three rollers to achieve that desired curve. It is ideal for cones, tubes and other hollow-shaped materials.
- U-bending: This process of bending is similar to the v-bending. The only difference is that it utilizes an U-die and the final parts are U-shaped.
- Rotary bending: This technique bends metals to create sharp edges. It is an excellent option for bend angles that are greater than 90°.
- Wipe bending: It uses a die to measure the radius of the sheet’s bend.
Bending is best for materials that are malleable, but not hard or brittle. It is a good choice for spring and mild steels, aluminum 5052 and copper.
Sheet Metal Bending Design Guidelines
In order to achieve better manufacturing results, You should consider the following factors when designing sheet metal parts.
Tolerance
Sheet metal fabrication tolerances refer to the acceptable deviations of sheet metal part features required for accurate and consistent installation and integration.
For sheet metal parts, we use ISO 2768-c to ensure that geometric and dimensional elements are properly controlled.
Dimension Detail | Tolerance |
Hole sizes | ±0.005″ |
Edge to edge, single surface | ±0.010″ |
Edge to hole, single surface | ±0.010″ |
Hole to hole, single surface | ±0.005″ |
Bend to edge / hole, single surface | ±0.015″ |
Bend to bend | ±0.020″ |
Edge to feature, multiple surface | ±0.030″ |
Over formed part, multiple surface | ±0.030″ |
Bend angle | ±1° |
Bending Radius
The minimum bend radius can vary depending on the materials. When the radius is less than recommended, it can lead to material flow in soft material and fracturing in hard material. To ensure bending strength, the bending radius of sheet metal should be greater than the minimum bending radius of the material. the following table shows the minimum bending radius of various sheet metal materials. t represents the thickness of sheet metal.
Materials | Soft Condition | Hard Condition |
Aluminum alloys | 0 | 6t |
Bronze | 0 | 4t |
Brass | 0 | 2t |
Stainless steel | 0.5t | 6t |
Low-carbon steel | 0.5t | 4t |
Titanium alloy | 2.6t | 4t |
The standards of each manufacturer may be different. It is recommended that the standard be reasonably chosen based on the actual situation.
Bending Height
The bending height should be at least twice the thickness of the sheet metal plus the bending radius, that is, H ≥ 2T + R. If the bending height is too small, the sheet metal will easily deform during bending, and it will be difficult to get the ideal shape and dimensional accuracy.
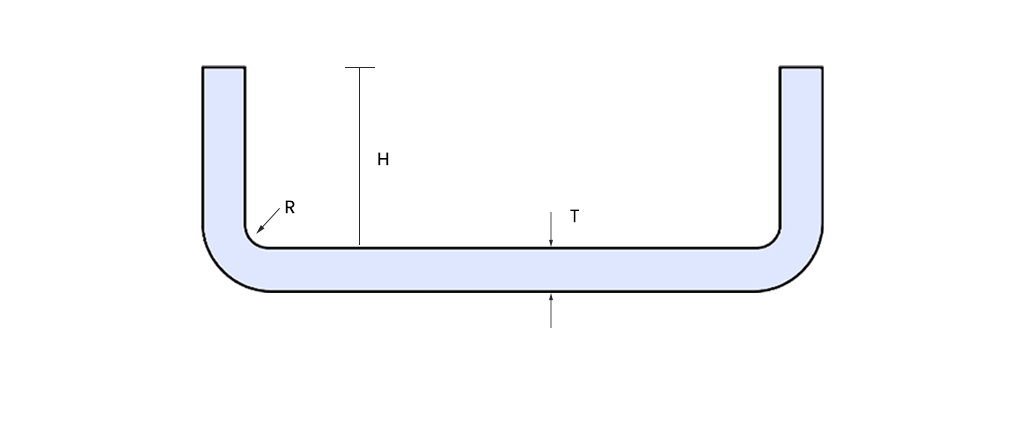
Bending Allowance
If you are bent sheet steel the neutral axis is shifted toward the inner surface that is bent. The K-factor represents the relationship between the location of the neutral axis (t) about the thickness of the material (MT) which is used to determine your bend’s allowance(K-factor= t/MT). The ideal K-factor ranges from 0.3mm to 0.5mm.
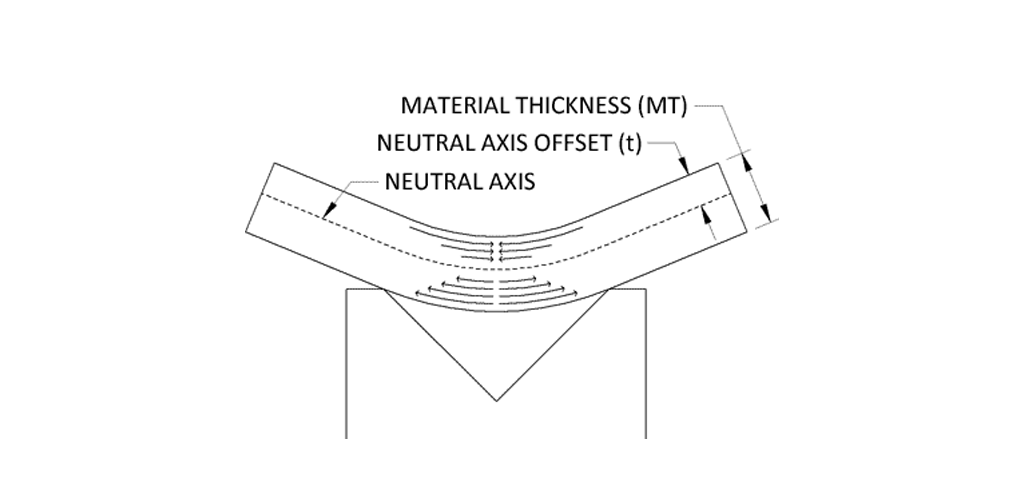
Bending Relief
When a bend is too close to the surface on the adjacent edge, the material tends to break. To avoid tearing, bend relief should be cut in the component. The length of the relief must be larger than the radius of the bend, and the width should be at least equal to the material’s thickness.
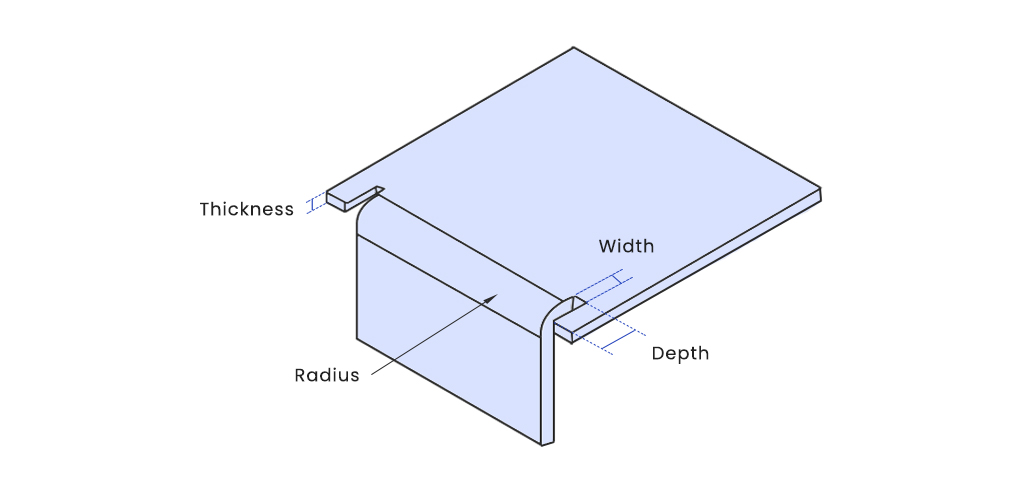
Curl Features
Curling is the process of adding a hollow circular roll on the edge of a sheet. Curls are generally employed to eliminate sharp edge and ensure that they are safe to handle. It is suggested that:
- The outside radius of a curl should be at least 2x the thickness of the material.
- The size of the hole must be at minimum equal to the curl’s radius plus the thickness of the material derived from the curly feature.
- A bend must be at least equal to the diameter of the curl plus 6 times the thickness of the material of the curl feature.
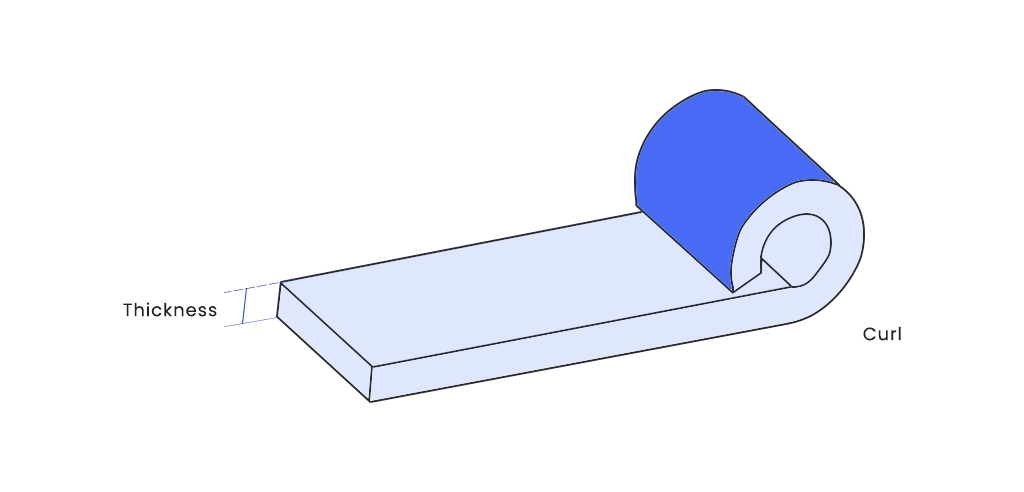
Hems Features
Hems are folds that are re-attached to the metal, made into the shape of a U shape. Hem features are typically utilized to give strength to the piece and also to join parts. The three major kinds of hems that industrial and design professionals should be aware of include open Hem, closed, as well as teardrop-shaped hem.
- Closed hem: Closed hem is closed tightly with no gaps. The inner diameter should be equal to the thickness of the material(D=T), and the length of the return hem should be at least 6x the thickness of the material(H ≥ 6T).
- Open hem: This hem has a small gap or space that leaves the fold open. The recommended return length should be at least 4x the thickness of the material(H ≥ 4T).
- Tear drop hem: This kind of hem is an elongated teardrop. The inside diameter must be at least equal to the thickness of the material(D=T) and a return length of at least 4x the thickness(H ≥ 4T).
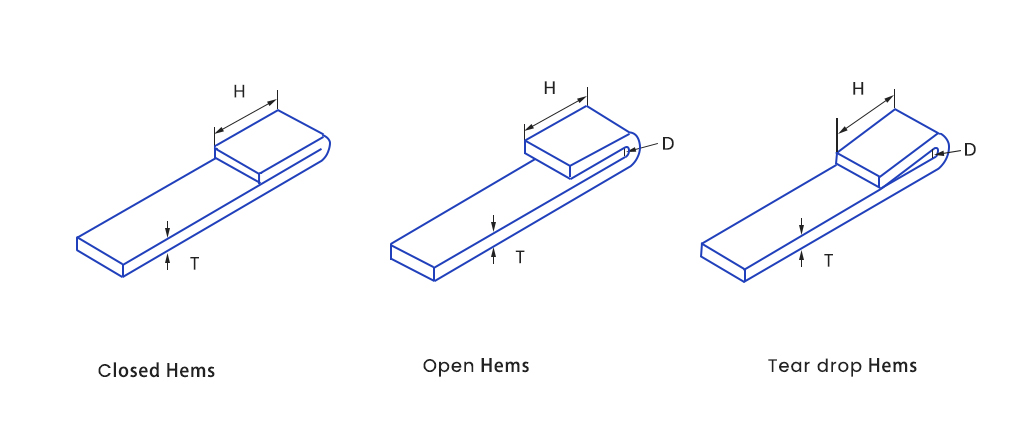
Holes & Slots
Holes or slots placed near bends tend to deform during the bending. To ensure a successful bending result, it is suggested to keep holes from bends by at minimum 2.5x the thickness of the material (T) plus the bend radius (R). When using slots for bending, it’s suggested to place it at least 4x the thickness of the material plus the bend radius away from the bend.
Slots and holes that are too close to the edge of the part can cause an issue related to bulging. It is suggested to leave a gap of at least 2x the thickness of the sheet between the extruded holes and part edge.
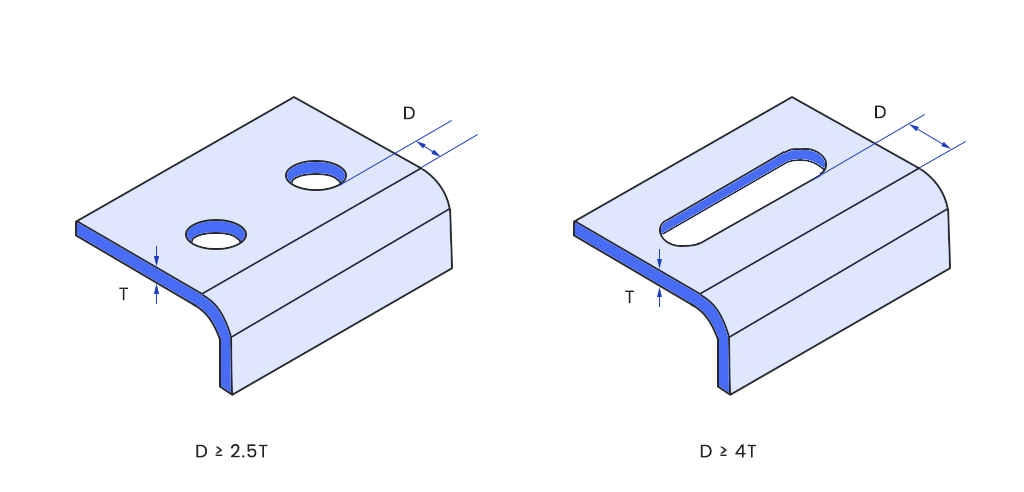
Start Your Sheet Metal Projects
At SogaWorks, we offer high-precision, fast, and quality sheet metal fabrication, forming and bending, services for the creation of sheet metal parts made of aluminum, stainless steel, steel, copper alloys, and many others. To get an instant quote, upload your models on our instant quoting platform.