Iron forms a vital part of our lives and is, in fact, the backbone of many industries. Iron is used in many ways. It’s in buildings, infrastructure, vehicles, and equipment. The types of iron are diverse and have special properties. Knowing the different types of iron, like pig iron, wrought iron, and cast iron, helps us choose wisely. This article will explore the types of irons and their properties.
What is Iron?
Iron is a chemical element. Its symbol is Fe, from the Latin “ferrum.” It has a crystalline structure. Pure iron is a silvery-white, bright metal. It is dense, with a density of 7.86 g/cm³. It has a melting point of 1539°C. Iron is electrically and thermally conductive.
Iron is one of the most abundant and versatile metals on Earth. It makes up about 5.1% of the Earth’s crust, ranking fourth in abundance after oxygen, silicon, and aluminum. In nature, free iron can be found only in meteorites, and on Earth, iron exists primarily in compound form.
The main iron ores are hematite and magnetite. Hematite has 50-60% iron. Magnetite has over 60% iron. Other important iron ores are limonite and siderite.
Different Types of Iron
Iron exists in various forms, each characterized by unique properties and compositions suitable for specific industrial applications. The main types of iron include pure iron, wrought iron, pig iron, and several variants of cast iron such as gray iron and ductile iron.
Wrought Iron
Wrought iron is an alloy of iron that is characterized by its malleability and ductility. It typically contains a very low carbon content, around 0.1% or less, which contributes to its ability to be easily shaped and welded. Wrought iron is often used in applications requiring high tensile strength and resistance to corrosion, such as in decorative elements and structural applications.
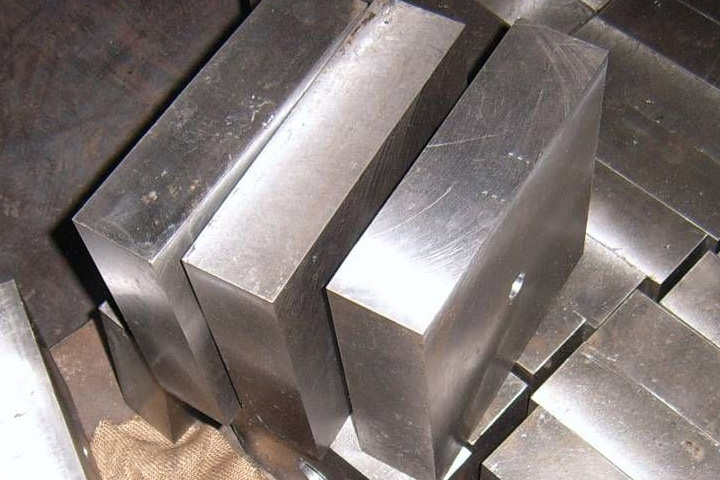
Cast Iron
Cast iron is a group of iron-carbon alloys with a carbon content exceeding 2%. It is produced by melting pig iron and adding elements such as carbon and silicon.
Pure Iron
Pure iron is the most basic form of iron, typically produced through processes that yield a high degree of purity, such as smelting in electric arc furnaces. This form contains approximately 99.8% iron with minimal carbon and manganese content, making it ideal for applications requiring high purity, particularly in electrical applications.
Pig Iron
Pig iron is an intermediate product of smelting iron ore with a high-carbon fuel, typically coke, in a blast furnace. It contains 2% to 4% carbon, along with varying amounts of silicon, manganese, phosphorus, and sulfur. While pig iron itself is too brittle for most applications, it serves as a raw material for producing cast iron and wrought iron.
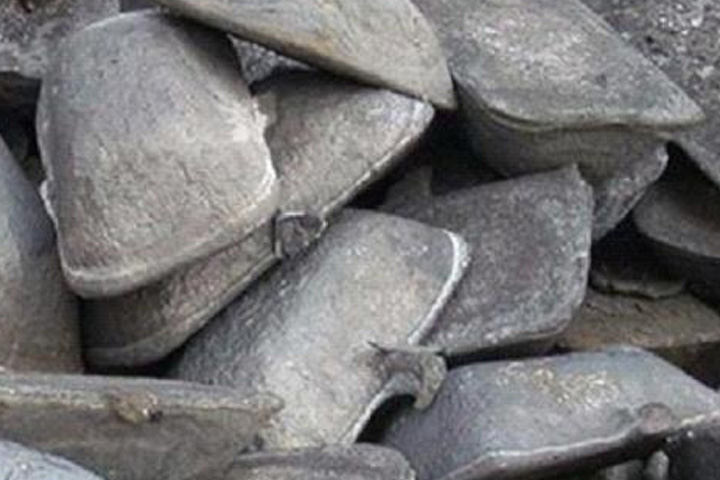
Classification by Composition
The classification of iron by composition is fundamental to understanding its various forms and their applications. This classification can primarily be divided into two categories: cast iron and steel, each with distinct characteristics based on carbon content and other alloying elements.
Cast Iron
Cast iron is characterized by its high carbon content, typically ranging from 2% to 4%. It is known for its excellent casting properties, making it suitable for complex shapes due to its fluidity in the molten state.
Steel
Steel is another vital form of iron, and it can be categorized based on its carbon content:
Low-carbon Steel: This type contains carbon levels ranging from 0.03% to 0.3%. It is known for its ductility and is commonly used in construction and manufacturing.
Medium-carbon Steel: Comprising 0.3% to 0.6% carbon, this steel type offers a balance of strength and ductility, making it suitable for automotive components and machinery.
High-carbon Steel: With a carbon content of 0.6% to 2%, high-carbon steel is known for its hardness and strength, commonly used for tools and dies. Additionally, various alloy steels incorporate other elements like nickel, chromium, and manganese to enhance specific properties such as corrosion resistance, toughness, and elasticity.
Classification by Microstructure
The classification of iron by microstructure is a vital aspect of understanding its properties and applications. This classification is primarily based on the shape of graphite and the matrix of the structure, leading to distinct forms of cast iron.
Graphite Shape
Cast irons can be classified according to the shape of the graphite present within their microstructure.
Lamellar (Flake) Graphite (FG): This form is characterized by thin, flaky graphite structures which are often found in gray cast iron, contributing to its good machinability and damping capacity.
Spheroidal (Nodular) Graphite (SG): Also known as ductile iron, this type features rounded graphite nodules, which enhance its tensile strength and ductility, making it suitable for applications requiring significant toughness.
Compacted (Vermicular) Graphite (CG): This classification refers to a structure where the graphite is intermediately shaped between lamellar and spheroidal, providing a combination of properties from both.
Temper Graphite (TG): Formed through a solid-state reaction known as malleabilization, temper graphite exhibits unique mechanical properties that allow for increased flexibility and toughness in the final casting.
Matrix of the Structure
In addition to graphite shape, cast irons are also classified based on the matrix structure, leading to different material characteristics.
Ferritic: Characterized by a matrix primarily composed of ferrite, providing good ductility and corrosion resistance.
Pearlitic: This matrix consists of alternating layers of ferrite and cementite, which enhances strength and hardness.
Austenitic: When the matrix retains austenitic structure, it offers superior corrosion resistance and high-temperature strength.
Martensitic: A martensitic matrix is formed through rapid cooling, resulting in high hardness and strength, suitable for wear-resistant applications.
Bainitic (Austempered): This microstructure is obtained through specific heat treatment processes, providing a combination of strength and ductility. These classifications by microstructure not only aid in understanding the mechanical properties of different cast irons but also influence their suitability for various industrial applications. Each form exhibits unique attributes that can be exploited in design and manufacturing processes, showcasing the versatility of iron as a material.
Cast vs Wrought Iron: Understanding Their Difference
Both cast and wrought irons are iron-carbon alloys. But, they differ in composition and properties.
Composition
Cast iron is an alloy of iron and carbon with a carbon content of more than 2%. Some kinds of cast iron can contain carbon in as high a percentage as 6.67%. Other alloying elements in cast iron include silicon, manganese, phosphorus, and sulfur.
Wrought iron, on the other hand, is a relatively pure form of iron obtained by further refining pig iron. Its carbon content is extremely low, usually less than 0.05%. It is produced by melting pig iron and removing impurities.
Physical Properties
Cast iron has a high carbon content, so it’s hard and brittle with little plasticity. It possesses low toughness and is fragile, though this also adds to its high compressive strength and hardness. Cast iron has medium thermal conductivity. Its thickness lets it store heat during heating.
Make Your Idea Take Shape!
Wrought iron has low carbon content, hence it is soft and ductile. It has lower strength and hardness but is easy to forge and weld. Wrought iron has excellent thermal conductivity. It heats up fast. This is useful for making cookware.
Price
As wrought iron needs more refining processes to remove impurities, it costs more and the price is relatively expensive. On the other hand, cast iron has a simpler refining process and therefore is cheaper in terms of cost.
Applications of Different Types of Iron
Iron is a fundamental material in various industries due to its versatile properties. The applications of different types of iron are categorized based on their specific characteristics, which cater to the needs of various sectors.
Manufacturing and Machinery
Iron’s strength and malleability make it an indispensable material in manufacturing machinery and machine tools. Pure iron, while relatively soft, can be alloyed to enhance its properties, making it suitable for applications that require high durability and performance. Pig iron, though primarily an intermediate product, is critical in the production of cast iron and steel, which are used in a wide array of manufacturing processes.
Automotive Industry
The automotive sector is a significant consumer of iron and steel. The need for lightweight and strong materials has led to advancements in steel alloys, contributing to vehicle safety and fuel efficiency. Iron is also essential for producing various automotive components, including structural elements and battery casings for electric vehicles, showcasing its versatility in this rapidly evolving industry.
Construction Industry
Iron, particularly in the form of steel, is extensively used in the construction industry. Steel, which is primarily composed of iron, is essential for constructing robust building frames, reinforced concrete structures, and various architectural elements. Its high tensile strength makes it suitable for creating safe infrastructures such as skyscrapers and bridges. Additionally, iron is employed in manufacturing fastening materials like nails and screws, which are crucial for assembling and securing building components.
Energy Sector
Iron plays a vital role in the energy sector, particularly in renewable energy infrastructure. Its properties are crucial for constructing components such as wind turbines and solar panels. Innovations in iron-based technologies are anticipated to enhance the efficiency and sustainability of energy production, underscoring the metal’s importance in modern energy systems.
Conclusion
China CNC machining manufacturers use various types of iron. It’s vital to choose the right one to meet specific performance needs. Both types of iron have unique properties. Cast iron is hard and wear-resistant. Wrought iron is ductile. Each is best for different uses. Knowing the properties of different types of iron is key. This includes tensile strength and machinability. It will help you make the right decision. It will ensure your project’s success and longevity.
At SogaWorks, we specialize in rapid prototyping and on-demand manufacturing. Supported by the strong network of high-vetted manufacturing plants, we deliver custom CNC machining services with a broad range of materials including different types of iron, stainless steel, aluminum, and more.