Although stainless steel possesses excellent corrosion resistance, it can still rust under certain conditions. By understanding the various types of corrosion that stainless steel may experience, we can take appropriate measures to mitigate damage when corrosion occurs. Below, we will discuss why stainless steel rusts and how to remove rust from stainless steel.
Does Stainless Steel Rust?
In fact, stainless steel can rust under certain conditions. Stainless steel can resist atmospheric oxidation, while also resisting corrosion of media containing acids, alkalis, and salts. Its corrosion resistance varies depending on the alloying composition, usage, and the type of environmental condition. For example, the 304 stainless steel pipe has excellent rust resistance in dry, clean air, but if used in a coastal area with salt-laden mist, it will quickly rust. In contrast, a 316 stainless steel pipe performs well in such environments.
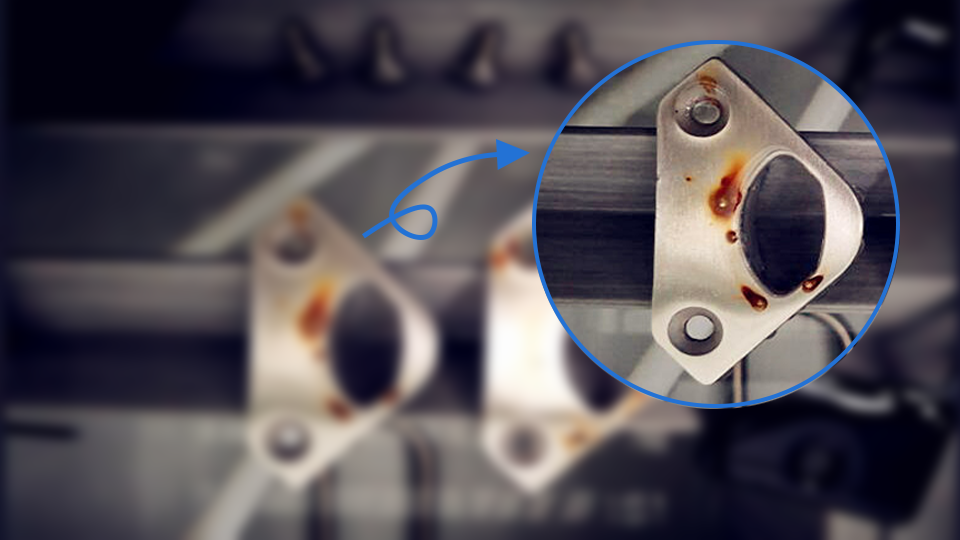
Stainless steel gets its corrosion resistance through a very thin, strong and dense chromium oxide film on its surface. This film prevents the continued penetration of oxygen atoms and further oxidation. Once this thin film is damaged, oxygen atoms from the air or liquid will continue to infiltrate, or iron atoms from the metal will continue to separate, forming iron oxide, and the metal surface will be continually corroded. Many ways can lead to damage to the surface film. They include:
- Dust containing other metal elements or foreign metal particles on the stainless steel surface. In humid air, condensation between the foreign particles and the stainless steel forms a micro-battery system, triggering an electrochemical corrosion that damages the protective film.
- Organic liquids (such as juice from fruits, soup, sputum, etc.) on the stainless steel surface. Organic acids will be formed in the presence of water and oxygen, and over time, these organic acids corrode the metal surface.
- Adhesion of substances containing acids, alkalis, or salts (such as alkaline water from wall treatments or limewater splashes) to the stainless steel surface, causing localized corrosion.
- In polluted air, (such as atmospheres containing large amounts of sulfur compounds, carbon oxides, or nitrogen oxides), Sulfuric acid, nitric acid, or acetic acid droplets will be formed, which can lead to chemical corrosion.
Tips
To ensure that the metal surface remains bright and free from rust, we recommend the following:
- Regularly clean and wipe the decorative stainless steel surfaces. This can remove contaminants and eliminate external factors that may lead to corrosion.
- In coastal areas, use 316 stainless steel for its resistance to seawater corrosion.
- Some stainless steel pipes on the market may not meet the relevant national standards. So it is important to select products from reputable manufacturers carefully.
Types of Corrosion on Stainless Steel
The following types of stainless steel corrosion are classified based on the destroyed passive film:
Pitting Corrosion: Pitting corrosion is a highly dangerous form of localized corrosion. During the process, small holes form and then rapidly corrode, which can eventually lead to perforation in severe cases.
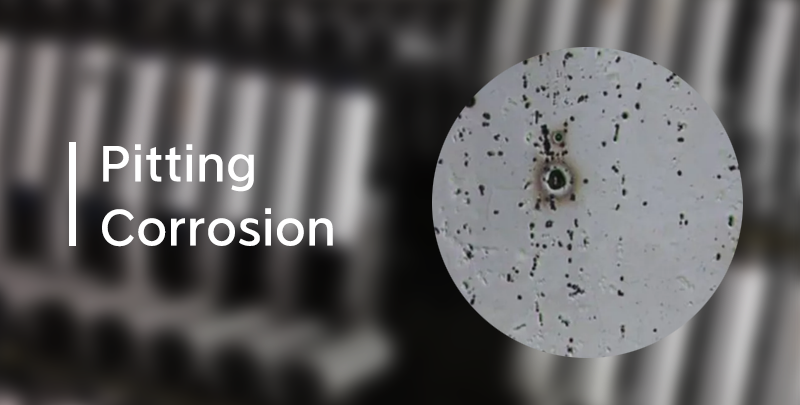
Crevice Corrosion: Stainless steel requires a supply of oxygen to maintain its surface passivation layer. In very tight crevices, oxygen may not always reach the stainless steel surface, making it prone to corrosion.
Stress Corrosion Cracking (SCC): Stress corrosion cracking refers to the damage that occurs when a metal is exposed to a corrosive environment while under tensile stress.
Intergranular Corrosion: Intergranular corrosion occurs due to a lack of chromium at grain boundaries, causing these areas to corrode preferentially and eventually leading to the separation of entire grains from the metal.
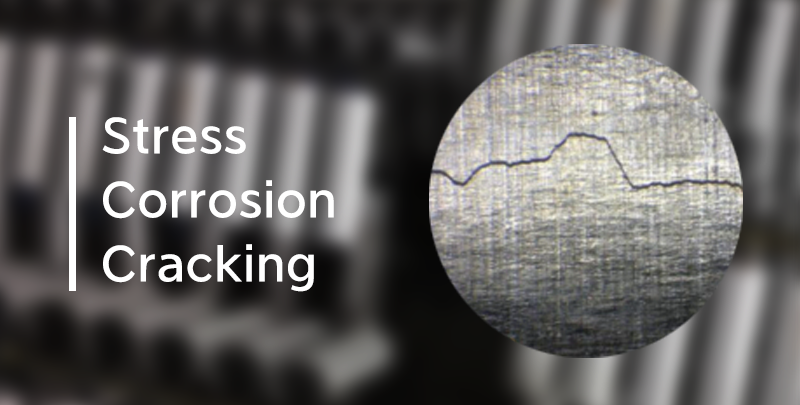
Factors Affecting Stainless Steel Rusting
The main factors affecting the rusting of stainless steel are as follows:
Content of Alloying Elements
When the chromium content in steel reaches 10.5%, it becomes resistant to rust. The higher the chromium and nickel content, the better the corrosion resistance. For example, 304 stainless steel contains 8-10% nickel and 18-20% chromium, which makes it resistant to rust under normal conditions.
Smelting Process of the Manufacturer
A large stainless steel plant is primarily equipped with advanced smelting technology, equipment, and processes to ensure effective control of alloy elements, removal of impurities, and regulation of steel billet cooling temperatures. As a result, product quality is reliable and less prone to rusting. In contrast, smaller steel plants with outdated equipment and processes may struggle to remove impurities during smelting, which increases the possibility of rusting in the stainless steel parts.
External Environment
Stainless steel is less likely to rust in dry, well-ventilated environments. However, in areas with high humidity, continuous rainy weather, or environments with high acidity or alkalinity, rusting is more likely to occur. Even 304 stainless steel can rust if the environment is excessively harsh.
How to Remove Rust from Stainless Steel
Once you have a little or a bigger spot on your stainless steel parts, these tried and true methods will get your stainless steel gleaming again.
Passivation
A chemical method involves using an acid pickling paste or sprays to passivate the rusted areas, forming a chromium oxide film that restores the corrosion resistance. After acid pickling, it is crucial to rinse thoroughly with clean water to remove all contaminants and acid residues. Afterward, re-polish the surface using polishing equipment and seal it with polishing wax. For areas with light rust spots, a mixture of 1:1 gasoline and motor oil can be used with a clean cloth to wipe off the rust.
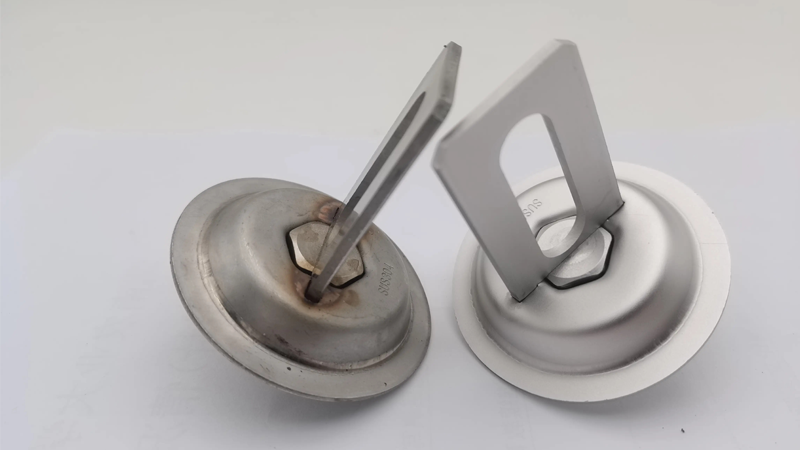
Sand blasting
Sand blasting with glass or ceramic beads can be used for cleaning, pitting, brushing, and polishing. Mechanical methods may remove previously cleaned material, polishing compounds, or abrasive materials, which could cause contamination. All forms of contamination, especially foreign iron particles, can act as sources of corrosion, particularly in humid environments. Therefore, mechanical cleaning should ideally be done under dry conditions. While mechanical cleaning can only address surface contamination, it does not alter the inherent corrosion resistance of the material. It is recommended to re-polish the surface with polishing equipment and seal it with polishing wax after mechanical cleaning.
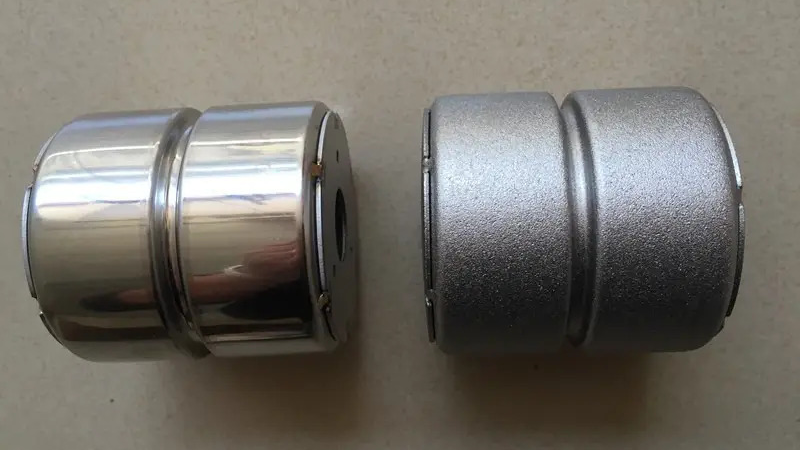
Types of Stainless Steel
Stainless steel is commonly classified based on its metallurgical structure. Generally, there are 3 main types of stainless steel: austenitic, ferritic, and martensitic stainless steels. Based on these three basic metallurgical structures, there are also variations developed for specific needs, such as duplex stainless steel, precipitation-hardening stainless steel, and high-alloy steel with less than 50% iron content.
Austenitic Stainless Steel: The matrix is primarily composed of austenite, which has a face-centered cubic crystal structure (FCC phase), and is non-magnetic. Austenitic stainless steel can be strengthened by cold working.
Ferritic Stainless Steel: The matrix is primarily composed of ferrite, which has a body-centered cubic crystal structure (BCC phase) and is magnetic. Ferritic stainless steel cannot be hardened by heat treatment but can be slightly strengthened by cold working.
Martensitic Stainless Steel: The matrix is primarily composed of martensite, which can have a body-centered cubic or cubic crystal structure, and is magnetic. Martensitic stainless steel can be hardened and its mechanical properties adjusted through heat treatment.
In general, aside from the alloying elements, austenitic stainless steel has the best corrosion resistance. Ferritic stainless steel is suitable for environments with lower corrosion risk. Martensitic stainless steel and precipitation-hardening stainless steel are ideal for environments with mild corrosion and when high strength or hardness is required.
Table 1. Comparison of Stainless Steel Corrosion Resistance
Types | Austenitic Stainless Steel | Martensitic Stainless Steel | Ferritic Stainless Steel |
Atmospheric corrosion resistance | Good | General | Good |
Acid corrosion resistance | Good | General | Good |
Crevice corrosion resistance | Good | General | Good |
Stress corrosion resistance | General | General | Good |
Common Stainless Steel Grades
Some commonly used grades of stainless steel include:
304 Stainless Steel
This is one of the most widely used austenitic stainless steels, suitable for manufacturing deep-drawn components, acid-resistant pipelines, containers, structural parts, and various types of instruments. It can also be used for producing non-magnetic, low-temperature equipment and parts.
304L Stainless Steel
Developed to address the serious intergranular corrosion tendency of 304 stainless steel caused by Cr23C6 precipitation, 304L is an ultra-low carbon austenitic stainless steel. It has significantly better intergranular corrosion resistance compared to 304 stainless steel in its sensitized state. Aside from its slightly lower strength, its other properties are similar to 321 stainless steel. It is mainly used for manufacturing corrosion-resistant equipment and parts that require welding but cannot undergo solution treatment afterward, and can be used to make various types of instruments.
316 Stainless Steel
Based on 10Cr18Ni12 steel, with added molybdenum to enhance its resistance to reducing media and pitting corrosion. It has superior corrosion resistance compared to 304 stainless steel in seawater and various other media, making it primarily suitable for pitting-resistant materials.
316L Stainless Steel
An ultra-low carbon steel with excellent resistance to sensitized intergranular corrosion. It is suitable for manufacturing thick-section welded components and equipment, such as corrosion-resistant materials in petrochemical equipment.
17-4PH Stainless Steel
A martensitic precipitation-hardening stainless steel, with a hardness of HRC44, offering high strength, hardness, and corrosion resistance. It cannot be used at temperatures higher than 300°C. It has good corrosion resistance in both atmospheric conditions and dilute acids or salts, similar to 304 and 430 stainless steel. It is used in manufacturing offshore platforms, turbine blades, valve cores, valve seats, sleeves, and valve stems.
Put Your Custom Parts into Production Today!
Conclusion
Although stainless steel is known for its excellent corrosion resistance, it can still rust under certain environmental conditions. Understanding the above factors that lead to rusting, such as the alloy composition, and external contaminants can help prevent corrosion and extend the lifespan of stainless steel components.
By selecting high-quality stainless steel from reputable manufacturers, regularly inspecting the material, and applying technologies such as passivation and sandblasting, we can maintain the corrosion resistance of their stainless steel parts.
About SogaWorks
SogaWorks is an all-in-one online platform for custom mechanical parts, connecting over 1,000 top-tier factories to serve startups and major companies. We offer flexible manufacturing solutions for rapid prototyping, small-volume testing, and large-scale production with services like CNC machining, 3D printing, sheet metal fabrication, urethane casting, and injection molding. With our AI-powered quoting engine, SogaWorks can deliver quotes in 5 seconds, match the best capacity, and track every step. This cuts delivery times and boosts product quality.