Metal Active Gas (MAG) welding is a versatile and widely used welding process that combines the benefits of Gas Metal Arc Welding (GMAW) with the use of an active shielding gas. This guide aims to provide a comprehensive overview of MAG welding, covering its fundamental concepts, key knowledge areas, and practical applications. Whether you are a novice welder or an experienced professional, this guide will serve as a valuable resource for understanding and mastering MAG welding.
Fundament of MAG Welding
What is MAG Welding
MAG welding is a type of arc welding process that uses a continuously fed consumable wire electrode and an active shielding gas to protect the weld pool from atmospheric contamination. The active gas, typically a mixture of argon, carbon dioxide, and sometimes oxygen, reacts with the molten metal to influence the weld’s mechanical properties and appearance.
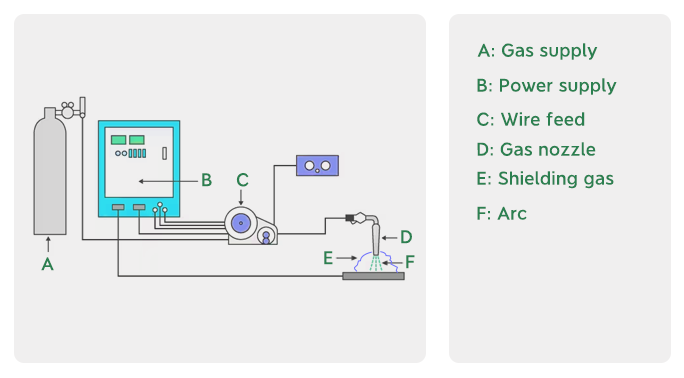
Differences Between MAG and MIG Welding
While MAG welding is often confused with Metal Inert Gas (MIG) welding, the key difference lies in the type of shielding gas used. MIG welding employs inert gases like argon or helium, which do not react with the weld pool. In contrast, MAG welding uses active gases that can chemically interact with the molten metal, affecting the weld’s characteristics.
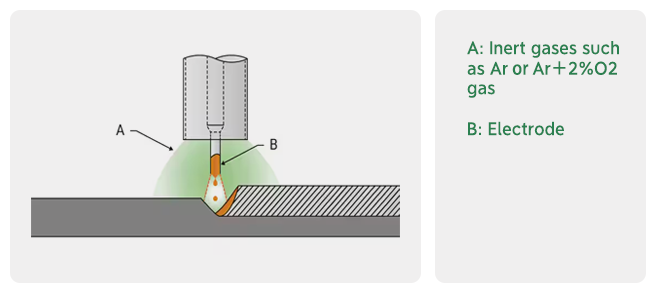
Advantages of MAG Welding
- Versatility: Suitable for welding a wide range of materials, including carbon steel, stainless steel, and some aluminum alloys.
- High Deposition Rates: Allows for faster welding speeds and higher productivity.
- Good Weld Quality: Produces strong, clean welds with minimal spatter.
- Ease of Automation: It can be easily automated and used in robotic welding systems.
Limitations of MAG Welding
- Gas Sensitivity: The choice of shielding gas can significantly impact weld quality, requiring careful selection.
- Equipment Cost: Initial setup costs can be higher compared to other welding processes.
- Skill Requirement: Requires a certain level of skill and experience to achieve optimal results.
Key Knowledge Areas in MAG Welding
Shielding Gases in MAG Welding
The choice of shielding gas is critical in MAG welding, as it directly affects the weld’s mechanical properties, penetration, and appearance. Common shielding gas mixtures include:
- Argon-CO2 Mixtures: Typically 75% argon and 25% CO2, which provides a good balance between weld quality and cost.
- Argon-Oxygen Mixtures: Often used for stainless steel welding, with oxygen content ranging from 1% to 5%.
- Ternary Mixtures: Combinations of argon, CO2, and oxygen, tailored for specific applications and materials.
Electrode Selection
The electrode used in MAG welding is a consumable wire that serves as both the filler material and the conductor for the welding current. Key considerations for electrode selection include:
- Material Compatibility: The electrode material should match or be compatible with the base metal.
- Diameter: Thicker electrodes are used for higher deposition rates, while thinner electrodes are suitable for finer, more precise welds.
- Coating: Some electrodes are coated with copper to improve conductivity and reduce oxidation.
Welding Parameters
Several parameters must be carefully controlled to achieve optimal weld quality in MAG welding:
- Voltage and Current: These determine the heat input and arc stability. Higher voltages and currents generally result in deeper penetration but may increase spatter.
- Wire Feed Speed: Controls the rate at which the electrode is fed into the weld pool, affecting deposition rate and weld bead geometry.
- Travel Speed: The speed at which the welding torch moves along the joint. Faster travel speeds can reduce heat input but may lead to insufficient penetration.
- Gas Flow Rate: Ensures adequate shielding of the weld pool. Insufficient gas flow can lead to porosity, while excessive flow can cause turbulence and contamination.
Welding Techniques
Different welding techniques can be employed in MAG welding, depending on the application and desired outcome:
- Short Circuit Transfer: Suitable for thin materials and out-of-position welding, characterized by low heat input and minimal spatter.
- Globular Transfer: Involves larger droplets of molten metal, resulting in higher deposition rates but increased spatter.
- Spray Transfer: Produces a fine spray of molten metal droplets, offering high deposition rates and deep penetration, ideal for thick materials.
- Pulsed Spray Transfer: Combines the benefits of spray transfer with reduced heat input, making it suitable for a wide range of materials and thicknesses.
Joint Design and Preparation
Proper joint design and preparation are essential for achieving strong, defect-free welds:
- Joint Types: Common joint types include butt joints, lap joints, T-joints, and corner joints.
- Edge Preparation: Beveling or chamfering the edges of thicker materials can improve penetration and weld quality.
- Cleaning: Removing rust, oil, and other contaminants from the joint area is crucial to prevent defects like porosity and inclusions.
Safety Considerations
MAG welding involves several safety hazards that must be addressed to protect the welder and ensure a safe working environment:
- Electrical Hazards: Proper grounding and insulation are essential to prevent electric shock.
- Fumes and Gases: Adequate ventilation and respiratory protection are necessary to avoid inhalation of harmful welding fumes and gases.
- UV Radiation: Welding produces intense ultraviolet (UV) radiation, requiring the use of appropriate protective gear, such as welding helmets with UV filters.
- Fire Hazards: Flammable materials should be kept away from the welding area, and fire extinguishers should be readily available.
Applications of MAG Welding
Automotive Industry
MAG welding is widely used in the automotive industry for manufacturing vehicle frames, body panels, and exhaust systems. Its high deposition rates and ability to weld thin materials make it ideal for mass production.
Construction and Infrastructure
In construction, MAG welding is employed for structural steelwork, pipelines, and heavy equipment. Its versatility and ability to produce strong, durable welds are essential for ensuring the integrity of large-scale structures.
Manufacturing and Fabrication
MAG welding is a staple in manufacturing and fabrication shops, where it is used to produce a wide range of products, from machinery components to consumer goods. Its adaptability to different materials and thicknesses makes it a valuable tool for custom fabrication.
Shipbuilding
The shipbuilding industry relies on MAG welding for constructing hulls, decks, and other critical components. The process’s ability to handle thick materials and produce high-quality welds is crucial for ensuring the safety and durability of ships.
Repair and Maintenance
MAG welding is also commonly used for repair and maintenance work, such as fixing cracks, reinforcing structures, and replacing worn-out parts. Its portability and ease of use make it a practical choice for on-site repairs.
Troubleshooting Common Issues in MAG Welding
Porosity
Porosity, or the presence of gas pockets in the weld, can weaken the weld and lead to failure. Common causes include:
- Contaminated Base Metal: Ensure the joint area is clean and free of rust, oil, and other contaminants.
- Inadequate Shielding Gas: Check for proper gas flow rates and ensure there are no leaks in the gas supply system.
- Moisture in the Electrode: Store electrodes in a dry environment and use them within their recommended shelf life.
Spatter
Excessive spatter can lead to a messy weld and increased post-weld cleanup. To reduce spatter:
- Optimize Welding Parameters: Adjust voltage, current, and wire feed speed to achieve a stable arc.
- Use the Correct Shielding Gas: Ensure the gas mixture is appropriate for the material and welding conditions.
- Maintain Proper Contact Tip Distance: Keep the contact tip at the correct distance from the workpiece to ensure consistent arc length.
Lack of Fusion
Lack of fusion occurs when the weld metal does not properly bond with the base metal, resulting in weak joints. To prevent this:
- Ensure Proper Joint Preparation: Bevel or chamfer the edges of thicker materials to improve penetration.
- Adjust Welding Parameters: Increase heat input by adjusting voltage, current, or travel speed.
- Maintain Correct Torch Angle: Keep the welding torch at the appropriate angle to ensure proper heat distribution.
Cracking
Cracking can occur due to excessive stress, improper cooling, or incompatible materials. To minimize cracking:
- Preheat the Base Metal: Preheating can reduce thermal stress and prevent cracking in thick or high-carbon materials.
- Use Low-Hydrogen Electrodes: Low-hydrogen electrodes can reduce the risk of hydrogen-induced cracking.
- Control Cooling Rates: Allow the weld to cool gradually to minimize residual stress.
Innovations in MAG Welding
Pulsed MAG Welding
Pulsed MAG welding is an advanced technique that alternates between high and low current levels, allowing for better control over heat input and weld pool dynamics. This technique is particularly useful for welding thin materials, out-of-position welding, and achieving high-quality welds with minimal spatter.
Double-Wire MAG Welding
Double-wire MAG welding involves using two wire electrodes simultaneously, significantly increasing deposition rates and welding speeds. This technique is ideal for high-productivity applications, such as heavy fabrication and shipbuilding.
Hybrid Laser-MAG Welding
Hybrid laser-MAG welding combines the precision of laser welding with the versatility of MAG welding. This innovative technique offers several advantages, including deep penetration, high welding speeds, and reduced heat input, making it suitable for a wide range of applications, from automotive manufacturing to aerospace.
Automated and Robotic MAG Welding
Automation and robotics have revolutionized MAG welding, enabling consistent, high-quality welds with minimal human intervention. Automated MAG welding systems are widely used in industries such as automotive, aerospace, and heavy manufacturing, where precision and repeatability are critical.
Conclusion
MAG welding is a versatile and efficient welding process that offers numerous benefits for a wide range of applications. By understanding the fundamental concepts, key knowledge areas, and practical techniques outlined in this guide, welders can achieve high-quality results and optimize their welding processes. Whether you are working in the automotive industry, construction, manufacturing, or any other field, mastering MAG welding will enhance your skills and contribute to the success of your projects.