Selecting the appropriate printing technique can greatly influence the quality of the final result. When considering pad printing vs silk screening, it’s essential to understand their distinct characteristics. Pad printing is essential for irregular geometries, while silk screen offers more color choices. This article will compare these printing technologies from multiple areas to help you make an informed decision.
What is Pad Printing?
Pad printing uses a steel gravure plate etched with the desired text or pattern and a curved silicone rubber pad to transform ink from the plate to the surface of the plastic part, printing the text or pattern.

There are four steps to the pad printing process:
1. Use a brush to evenly apply the ink to the steel plate.
2. Use a special scraper to remove excess ink.
3. Move the print head to the steel plate to pick up the ink from the pattern.
4. Move the print head to the product and press to transfer the pattern onto the surface.
Advantages of Pad Printing
The advantages of pad printing include:
Suitable for curved surface printing: The elastic silicone rubber print head is ideal for printing on substrates with complex shapes, including secondary and tertiary curved surfaces, as well as concave and convex surfaces beyond flat ones.
Capable of fine detail: It can print intricate graphics and text as thin as 0.05 mm.
Stable and continuous printing: Its printing accuracy remains consistent even during long print runs.
Eliminates drying process: It supports continuous multi-color printing without requiring a separate drying stage.
Material compatibility: Pad printing works on various materials, such as plastics, metals, glass, ceramics, leather, and bakelite. It allows accurate single-color, two-color, or multi-color prints.
Adaptable to delicate objects: It can perform soft-contact printing on delicate items like fruits, cakes, and eggs, as well as fragile objects such as ceramics and glass.
Easy to learn and reliable: The process is straightforward, with no particularly complex or advanced techniques required, making it simple to adopt.
Make Your Idea Take Shape!
What is Silk Screening?
Silk screen printing is a process where ink passes through certain holes in the screen and onto the printed material while the remaining holes are blocked. When the ink is under pressure and applied at a certain angle, it passes through the screen, printing the pattern onto the surface below.
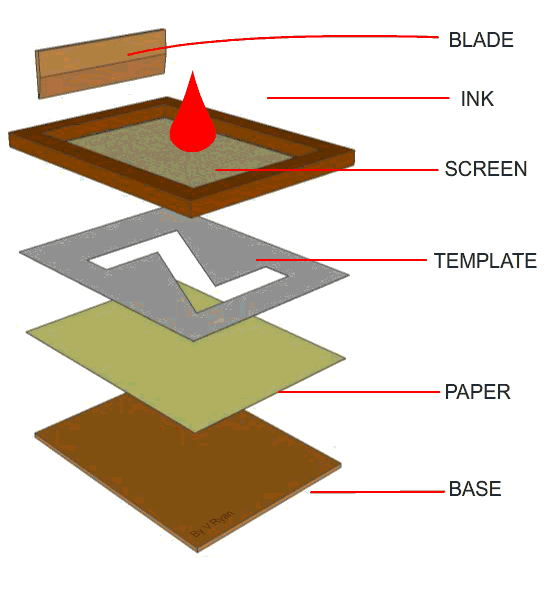
The silk screening can be divided into four steps:
1. Place the screen on the screen printer and secure it.
2. Apply the ink evenly on the screen and make sure the mesh holes are filled.
3. Use a scraper to press the ink through the mesh holes in the image area onto the printed object.
4. After printing, place the printed object in the drying equipment to dry the ink and adhere to the surface.
Advantages of Silk Screening
The advantages of silk screen printing include:
Material compatibility: Since the printing plate is made of silicone rubber which is soft and flexible, allowing printing on both flat or curved, hard or soft, large or small. In addition, it can also be used on fragile and deformable substrates due to low pressure.
Thick ink layer: when using white ink to cover the base color, ordinary methods may require 3 to 4 prints, while silk screen printing can achieve this in one pass. The thickness of the ink layer generally ranges from 5 microns to 100 microns.
Strong three-dimensional effect: The thick ink layer produces a realistic, textured effect, much better than offset printing for replicating prints and paintings.
Good light resistance: After adding light-resistant pigments and fluorescent pigments, the printed pattern can maintain its gloss permanently without being affected by temperature or sunlight.
Abundant applicable inks: Silkscreen printing works with water-based, oil-based, solvent-based, etc., and even slurry, paste, and powder.
Large format: The maximum printing area of silk screen printing can reach 3*4 m or even larger. General offset printing, relief printing, and other methods are far inferior to silk screen printing in terms of printing area.
Pad Printing vs. Silk Screening: What’s the Difference
Although pad printing and screen printing have many similarities, such as the inks for these technologies are usually universal. However, there are still many differences in the characteristics between them.
Principle
Pad printing transfers the pattern engraved on the steel plate to the workpiece through the rubber head, which is similar to using a stamp. Silk screen printing uses pressure to push the ink from the screen onto the surface to form a pattern or text. Pad printing is more flexible and suitable for various complex curved surfaces, while silk screen printing is more suitable for flat surfaces.
Printing area
Pad printing is limited for large-area printing. Silk screening can handle a larger printing area, and the screen can be recycled at a lower price. Therefore, silk screen printing is more suitable for large-scale printing tasks.
Flexibility in shape
Pad printing is more flexible in product shape. Whether it is a flat surface, a curved surface, or a complex wavy surface, pad printing can handle them as long as the rubber head can be deformed to reach. Silk screening is more restricted to flat or relatively regular curved surfaces.
Multi-color printing
The pad printing machine supports up to 12 colors and can print multi-color patterns at one time at a lower cost. Silk screen printing can also achieve multi-color printing, but the equipment cost is higher, especially the multi-color silk screen printing machine is very expensive.
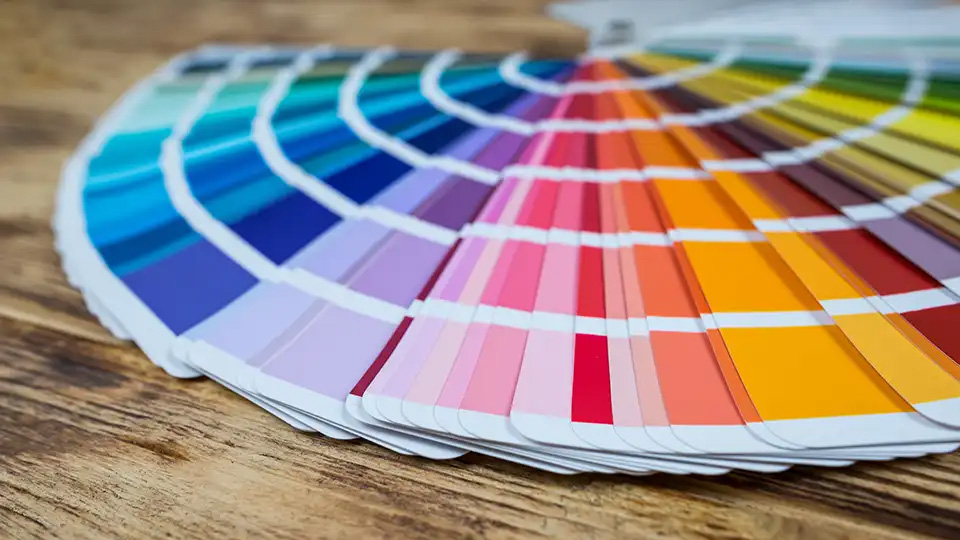
Ink layer thickness
Pad printing offers a thinner ink layer, but its color expression is excellent and the tech can be used on almost any surface. Silk screen printing offers a thicker ink layer, and the pattern has a strong three-dimensional effect.
Equipment maintenance
Pad printing machines have higher maintenance costs. Pad printing equipment usually contains multiple precision components such as etched steel plates, silicone heads, etc. These components will wear or age after long-term use and affect the printing quality. Therefore, pad printing equipment requires regular maintenance, including cleaning, lubrication, and tightening. Comprehensive maintenance every three months can significantly reduce the failure rate and improve printing efficiency. Screen printing equipment maintenance is simpler. Screen printing equipment mainly consists of a screen, scraper, ink tank, and other components. The screen is a key component and it will become clogged or worn after long-term use, so it needs to be cleaned and replaced regularly. It is generally recommended to conduct a comprehensive cleaning of the screen after every 5,000 square meters of printing and decide whether to replace it based on wear and tear.
Applications
Pad printing is widely used in industries such as electronic products, toys, and cosmetic packaging. More than 80% of high-end electronic products use pad printing to print logos and patterns. This is because pad printing can accurately reproduce patterns and maintain high accuracy even on complex curved and irregular surfaces. Similarly, in the field of toy and cosmetic packaging, pad printing technology is also widely used due to its high precision and durability. Silk screen printing has more advantages in occasions where large-area, flat printing is required. The advertising industry is one of the main application areas of silk screen printing technology, especially outdoor billboards and posters.
Pad printing vs. silk screening: Make the choice
To make the best choice between pad printing and silk screening, you need to consider the following factors:
Cost
The equipment cost of pad printing is higher, especially high-precision automated pad printing equipment. However, for large-scale production, it can improve efficiency and reduce labor costs. The pad printing plate has low production cost and fast replacement, which is suitable for small batch and multi-variety production. There are many types of pad printing inks, and the cost of special effect inks is relatively high, but the overall usage is small and accounts for a small proportion of the cost.
The price range of screen printing equipment is wide, and the cost of manual equipment is low and suitable for small-scale production. The production cost of screen printing is high and needs to be replaced regularly, but for the long-term mass production of the same pattern, the cost can be shared. The price of screen printing ink varies depending on the type and quality. The price of ordinary ink is low, and the cost of special ink increases.
Production efficiency
Pad printing has a high degree of automation, and advanced equipment can be printed at high speed and automatically, such as in the electronic product assembly line with other equipment to improve production efficiency. The pad printing plate can be replaced quickly, which is suitable for small batch production and can respond quickly to changes in market demand. It is efficient when printing small-sized products and can print multiple small products at the same time.
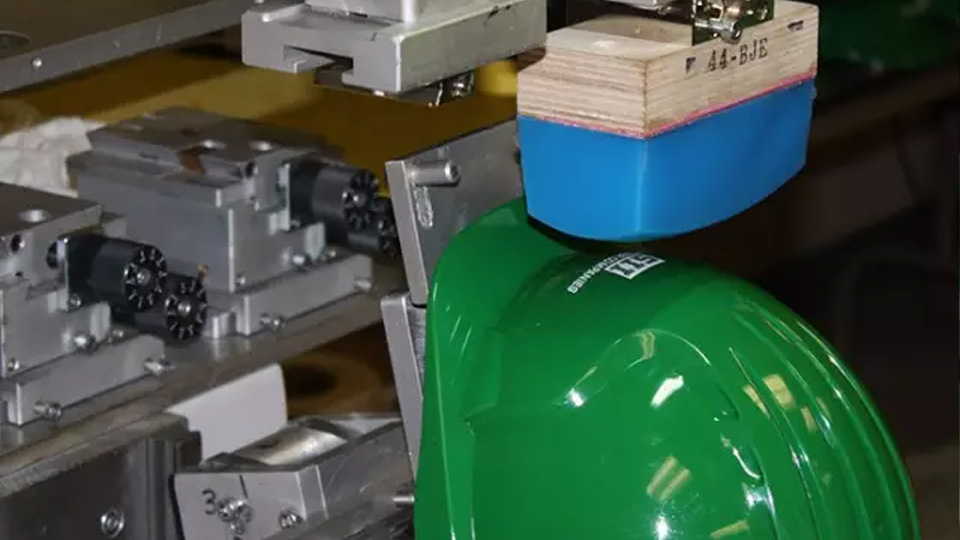
Screen printing has a large single printing area and is efficient in large-area printing such as large advertising posters. Manual screen printing is flexible and suitable for special shapes or small batches of products. Although it is inefficient, it can meet personalized needs. The combination of multi-color screen printing screens can print multiple color patterns at one time, reducing processes and improving efficiency.
Comptible product types
Pad printing is suitable for irregular-shaped products, such as spherical and cylindrical sports water bottles, thermos cups, etc., and can be evenly printed on curved surfaces. It is also suitable for small-sized precision products, such as electronic components, watch parts, etc., and can add logos and decorations without affecting performance.
Screen printing is suitable for flat products, such as paper, plastic cards, metal sheets, etc., and can achieve large-area uniform printing. It is also suitable for large products, such as billboards, car body advertisements, etc., and can be printed by splicing screens or large equipment. For special material products, such as glass, ceramics, wood, etc., good adhesion and printing effects can be achieved through suitable inks and processes.
Conclusion
When deciding between pad printing and silkscreen, it’s crucial to understand their key differences. Pad printing is more suitable for intricate designs on irregular surfaces, while silkscreen offers abundant colors for flat materials. Evaluate your project’s specific needs, such as design complexity and cost analysis, to make an informed choice.