Pistons are one of the key components in both automotive and industrial engines, with direct effects on performance, efficiency, and durability. The piston machining requires high precision and advanced techniques to be able to achieve the most demanding standards in performance. This article will approach the materials used, machining processes, heat treatment and surface treatments involved in the manufacture of pistons.
What is Piston?
Piston refers to the cylindrical, mechanical element involved in back-and-forth motion within the walls of a cylinder in an engine or a compressor. This part is indispensably necessary to the operation of an internal combustion engine since it is at this point that energy created by the combustion process can be converted into practical mechanical work by the piston through this essential process. A working piston’s mode of operation involves the connecting rod transmitting the force produced by combustion to the crankshaft. The connecting rod makes contact between the piston and the crankshaft. Because it operates under incredibly high pressure apart from being subjected to very stringent restrictions in temperature and friction during its operational process, the design and selection of pistons become crucially very relevant to the overall performance and life in service of applications.
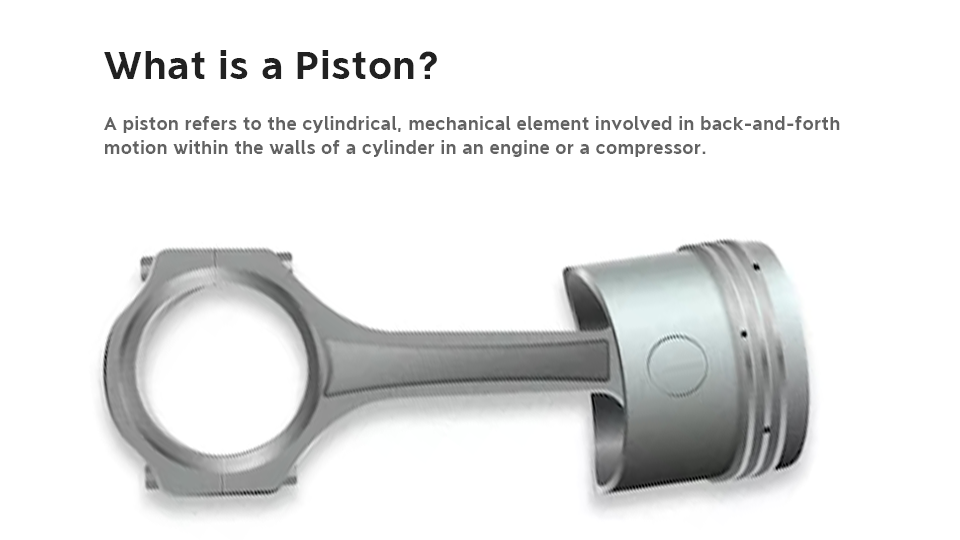
Structure of a Piston
The piston is usually a cylindrical part designed to fit closely inside the walls of a cylinder. Most modern pistons are made from aluminum or iron alloys; these metals are chosen for their strength and lightweight. The main parts of a piston include:
Piston Head: The upper surface of the piston, supporting the pressure exerted by combustion gases. The shape and size of the piston head, in turn, affect the layout of the combustion chamber, therefore affecting fuel efficiency and power output.
Piston Wall: Cylindrical side walls of the piston are designed to resist gas pressure and friction. It has a specified thickness and material composition to permit thermal expansion and prevent deformation at high temperatures.
Piston Rings: These are attached to the piston wall and are conventionally divided into compression rings and oil rings. The compression rings seal the cylinder so that the combustion gases do not escape, and the oil rings regulate the oil film thickness so that no oil can enter the combustion chamber.
Piston Pin: A shaft that connects the piston to the connecting rod, thus facilitating the vertical movement of the piston inside the cylinder, hence converting energy derived from combustion into mechanical motion.
Materials for Piston Machining
The selection of the right material is very critical to ensure optimum piston performance in any given application. The ideal materials used for the pistons must adhere to the following essential requirements:
Thermal stability: Low coefficients of thermal expansion and high resistance to changes in temperature.
Lightweight: Reduced density to minimize forces due to inertia during alternate motion.
High mechanical strength: The constituent material should have high tensile strength, fatigue resistance, and elongation at elevated temperatures.
Wear resistance: It has good wear resistance, corrosion resistance, and low friction under boundary lubricating conditions.
Machinability: It has good castability, ease of cutting, and compatibility with heat treatment processes.
Cost-effectiveness: Materials need to have a proper balance between performance and cost.
The predominant material for modern pistons is aluminum alloys, largely due to their excellent characteristics and advantages. The most frequent types of such alloys are:
Aluminum-copper alloys (e.g., Y Alloy): High fatigue strength and good machinability, but with high density and thermal expansion coefficients; hence, not so frequently used in the modern era.
Hypoeutectic aluminum-silicon alloys: These special alloys, containing about 8.5 to 10.5 percent silicon, are particularly suitable for application in low-load gasoline engines, where their characteristics can be fully exploited. While these alloys do exhibit very good castability, being capable of being cast into a variety of shapes without too much trouble, their general use is somewhat limited by the problems their higher thermal expansion characteristics present.
Eutectic aluminum-silicon alloys: These contain ~12% silicon and are extensively used in gasoline and diesel engines. They have low thermal expansion, excellent wear resistance, and good casting properties but lower thermal conductivity and machinability.
Hypereutectic aluminum-silicon alloys: With a high content of 18% to 23% silicon, these specialized alloys assume excellent properties with outstanding resistance to heat and wear development over time. However, despite their favorable characteristics, they imply very serious challenges in both machining and casting processes. These alloys are, therefore, especially suitable in applications experiencing high loads, particularly in advanced engine designs and functionalities.
Piston Blank Forming Methods
Die Casting
Die casting is the most common method for the production of aluminum piston blanks, where molten aluminum is poured into a metal mold. It has advantages in high dimensional accuracy and cost efficiency. However, defects such as thermal cracks and porosity may occur.
Forging
The forged pistons are used in high-performance engines. The process gives fine grain structures, high strength, and excellent thermal conductivity. The hypereutectic alloys cannot, however, be forged because of their brittle nature. It calls for very careful control of forging and heat treatment parameters to relieve all the residual stresses.
Liquid Metal Forging
A hybrid technique that uses aspects of both casting and forging is liquid metal forging, which involves pouring molten metal into a specially designed die. After the metal is poured, pressure is applied to assist in the solidification of the material in the die. This yields an innovative way of making dense structures with very minimal casting defects and hence a very effective process. In view of its numerous benefits, liquid metal forging is being widely adopted in the manufacture of advanced piston components.
Put Your Custom Parts into Production Today!
Heat Treatment in Machining of Pistons
The heat treatment process significantly raises the mechanical and thermal properties of pistons and, hence, makes them more efficient and durable. The usual steps involved in the treatment process are:
- Aging treatment: The piston should be heated to 220°C for 5 h or 205°C for 7-9 h in order to stabilize dimensions and improve hardness.
- T6 treatment: Solution treatment at 500°C for 4-6 hours followed by aging at 190°C for 8 hours to improve strength and hardness.
- T7 treatment: Same as T6 but at higher aging temperatures to stabilize a balance between strength and ductility.
Machining Processes for Piston
In the mass production of pistons, automated machining lines are used for efficiency and greater output. These involve the operations of:
Precision CNC machining: CNC machines are among the most important tools in the carrying out of fundamental operations such as skirt profiling. This operation usually calls for an elliptical or a barrel-shaped design since such a shape is mandatory in ensuring optimal performance in the final product.
Specialized equipment: Special and dedicated machinery is designed to handle expertly non-cylindrical features, including pinholes and complex internal geometries. This attention to detail ensures that tight tolerances are maintained throughout the process.
Weight balancing: All pistons used in the engine are precisely weight-matched for correct engine balance and optimum performance. It is, of course, done within a given tolerance level; permitted variation is ±2 grams for light vehicles and ±4 grams for heavy-duty engines.
Surface Finish for Piston Machining
Surface treatments can bring enhanced piston durability and performance:
Tin or Lead plating: Provides excellent anti-friction properties and shortens break-in periods.
Graphite coating: It is applied in cases of high loads to decrease wear and tear, and it enhances lubrication.
Anodizing: This is a process that forms a protective oxide layer about 0.1 millimeters thick, greatly increasing thermal resistance.
Ceramic coating: Applied to piston crowns to resist extreme temperatures and reduce heat transfer.
Composite inserts: Materials such as ceramic fibers or foamed metals have been used to significantly enhance thermal insulation while simultaneously coping with high temperatures and reduced expansion.
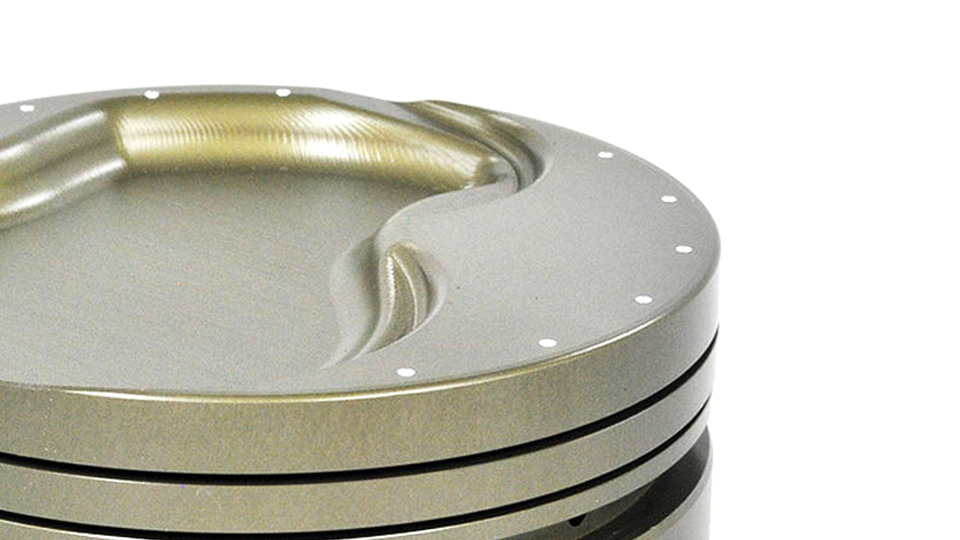
Conclusion
Piston machining is a highly complex and sophisticated process that perfectly blends advanced materials, precision manufacturing techniques, and state-of-the-art surface treatments for optimum performance. Innovations in materials science, especially the development of hypereutectic alloys, combined with advanced manufacturing processes like liquid metal forging, ensure that pistons are capable of meeting the ever-increasing and demanding requirements presented by modern engine designs. The manufacturers, through the use of state-of-the-art technologies such as CNC machining, can achieve an unrivaled level of precision, outstanding efficiency, and exceptional reliability throughout the entire piston production process.