Screw, as one of humanity’s earliest mechanical fastening devices, traces its origins to the 3rd century BCE Archimedes’ screw pump. Through 2,300 years of technological evolution, this grooved fastener has become pivotal to industrial systems, currently enabling over 85% of mechanical connections across domains from furniture assembly to aerospace engineering. In this guide, we will explore what screws are, screw head and drive types, and materials and processes.
Overview of Screw
A screw is a small cylindrical or conical metal rod with threads, featuring a slotted head that can be used independently. It is primarily used for connecting or securing objects. A screw uses the principles of physics and mathematics involving the inclined plane, circular rotation, and friction to tighten machinery components effectively.
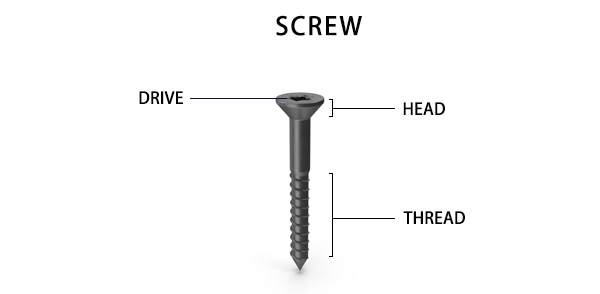
Different Types of Screw Heads
The screw head refers to the top portion of the screw, which can vary in shape and size (e.g., flat, round, or countersunk).
Pan Head
The pan head has a flat, disc-shaped head that provides a large contact area, reducing pressure on the connected material. It’s ideal for applications requiring aesthetic appeal and a smooth surface. The pan head design also enhances the aesthetic appeal of the screw.
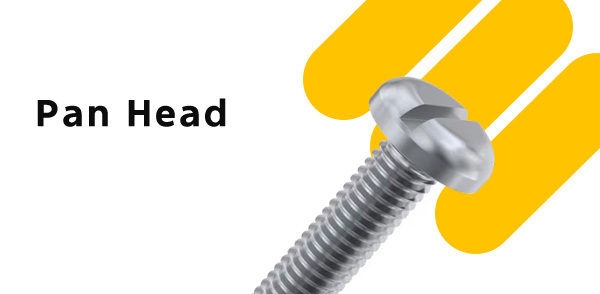
Countersunk Head
The countersunk screw has a slightly recessed head that sits flush with the connected surface of the material. These screws often require countersinking, they are usually processed with a 90° angle in metric variants, and an angle of 100° in aerospace and military applications.
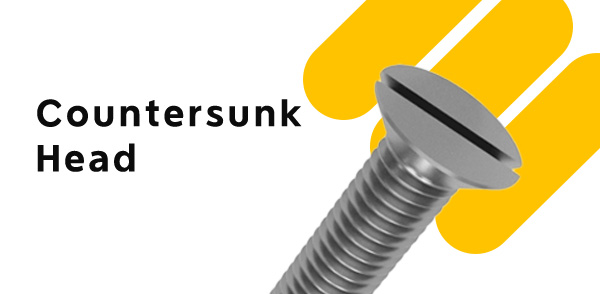
Hexagon Head
The hex head has a six-sided recess, typically tightened or loosened using tools like an Allen wrench or a hex socket. Hex head screw is the most common screw type used in multiple industries.
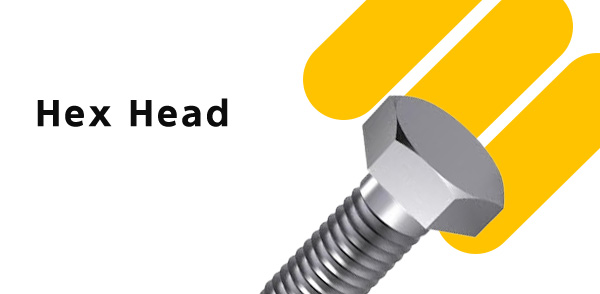
Flange Head
Hex head with flange features an added flat surface on top of the head. This flat surface provides a larger contact area and reduces pressure on the connected materials. The flanged design helps prevent the wrench from slipping.
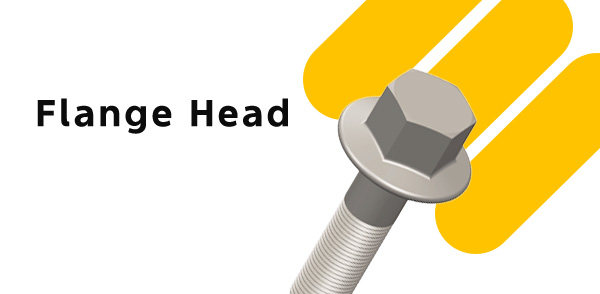
Square Head
The head of this screw is square-shaped which enables the screw to be hammered without slipping off. It is suitable for manual installation or tightening with a tool. The square-headed design also helps improve torque transmission efficiency.
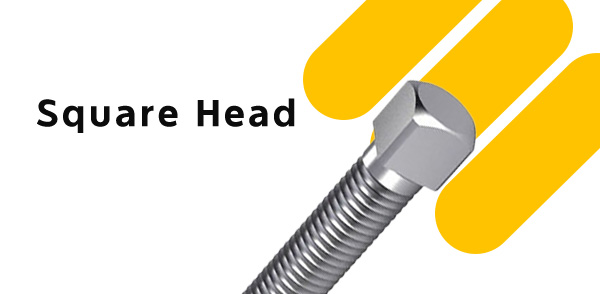
Cheese Head
Cheese head screws feature a cylindrical on the top. This design reduces pressure on the connected material, and it is suitable for a smooth connection.
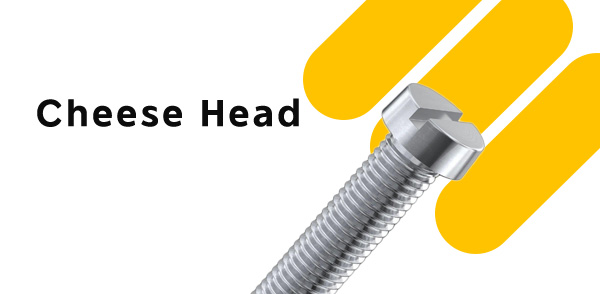
Round Head
Round head screws feature a fully rounded head and offer higher strength for its larger diameter. It is suitable for applications that do not require a significant torque.
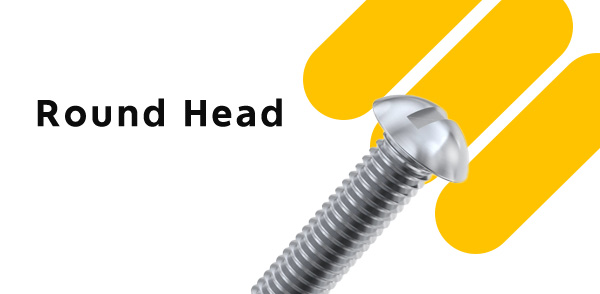
Truss Head
Truss head screws have a low-profile design that minimizes the height of the head. While they are less visible and can be more aesthetically pleasing, they are also more prone to breakage due to their thin structure. These screws can come in both full crown and modified crown designs.

Different Types of Screw Drives
The drive is the recessed or protruding feature on the screw head that allows a tool—typically a screwdriver or drill bit—to turn it. The drive type determines how torque is applied and how securely the tool engages with the screw.
Slotted Drive
The slotted screw drive is the granddaddy of all screw drives. It features a single, straight slot cut across the top, designed to be driven by a flathead screwdriver. It is easy and cheap to manufacture, requiring minimal tooling. Its limitations are also evident, the flat-head screwdriver often slips out due to its moderate torque, especially when the tool is not perfectly aligned, which can strip the screw head and cause significant frustration.
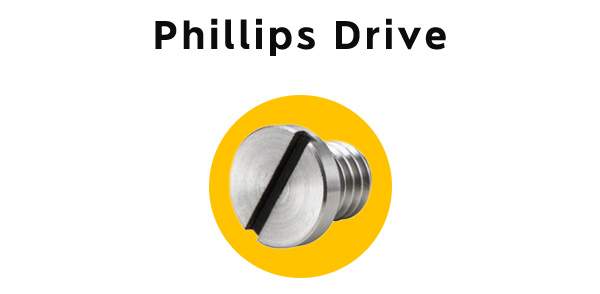
Phillips Drive
The Phillips drive includes a cross-shaped recess that allows for better engagement with the screwdriver, reducing the risk of slippage compared to slotted drives. It is still not perfect, The screwdriver may still slip, damaging either the screw or the tool with high torque.
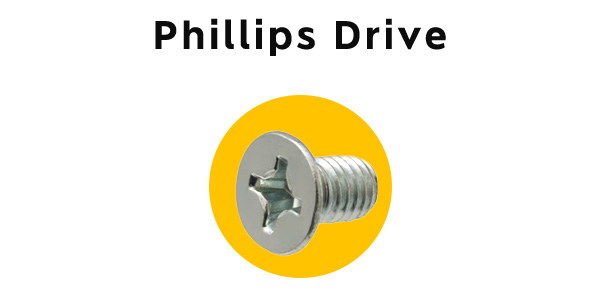
Pozi Drive
It resembles a cross recess on the surface but adds four smaller ribs between the main cross recesses, creating an eight-point engagement with the screwdriver. This design significantly reduces slippage by providing a tighter, more secure fit, allowing for greater torque application without slipping. However, it requires a specific cross recess screwdriver (a regular cross screwdriver can be inserted, but there is a risk of slipping), and it is less common in the US.
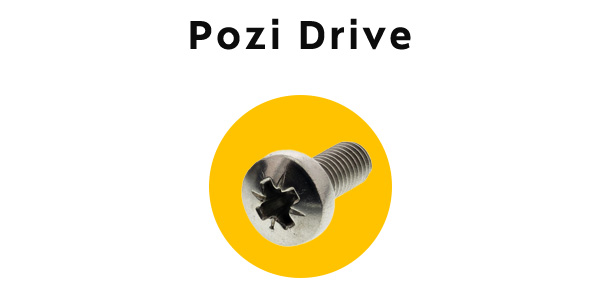
Torx Drive
The head of the Torx socket screw features a unique hexagonal recess with rounded corners at each angle, requiring a Torx screwdriver for use. This design not only offers excellent tool retention but also allows for the transmission of high torque while effectively preventing damage to the screw head.
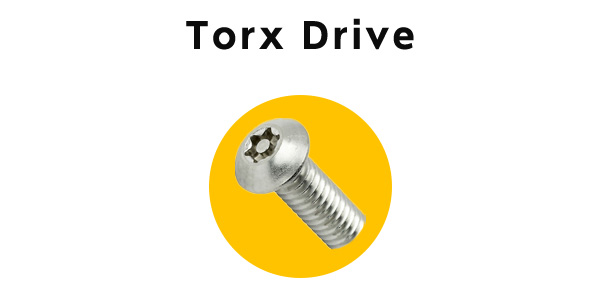
Hex Drive
Hexagonal socket screws have a hexagonal recessed head that requires a hex wrench or hex screwdriver for operation. This design provides significant torque while effectively preventing damage to the screw head.

Robertson/Square Drive
The Robertson drive features a simple square-shaped recess. It provides excellent torque transmission with almost no slippage due to its deep and straight walls that securely grip the screwdriver. You can even operate it with one hand because the screw stays on the screwdriver.
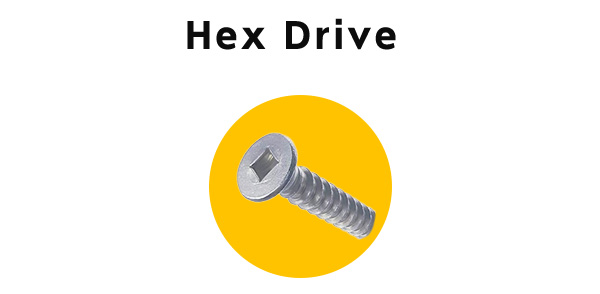
Different Types of Screw Thread
Screw threads vary depending on the standards they follow. Here are the main types:
International Metric Thread System
This is the standard thread system adopted by the China National Standard. It features a flat crest for easier machining and a rounded root to enhance thread strength. The thread angle is 60 degrees, and its specifications are denoted with an “M.” Metric threads come in two varieties: coarse and fine. For example, “M8*1.25” indicates a metric thread (M) with a nominal diameter of 8 mm and a pitch of 1.25 mm. Additional details can be found in the “GB/T 70.1-2008 Hexagon Socket Cap Screws” standard and its referenced documents.
American Standard Thread
This thread type has flat crests and roots, offering improved strength. With a 60-degree thread angle, its specifications are based on the number of threads per inch. It’s divided into three categories: coarse (NC), fine (NF), and extra fine (NEF). For instance, “1/2-10NC” refers to a thread with a 1/2-inch outer diameter, 10 threads per inch, and the NC designation.
Unified Thread
Developed collaboratively by the United States, the United Kingdom, and Canada, the Unified Thread standard is widely used for British Imperial threads. It has a 60-degree thread angle and is specified by threads per inch. It’s classified into coarse (UNC), fine (UNF), and extra fine (UNEF). For example, “1/2-10UNC” indicates a 1/2-inch outer diameter, 10 threads per inch, and the UNC category.
Sharp V Thread
This V-shaped thread has sharp crests and roots, making it relatively weak and less common. Its thread angle is 60 degrees.
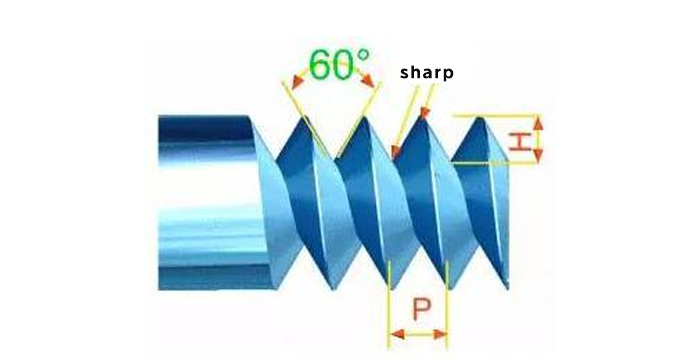
Whitworth Thread
A British Standard thread with a 55-degree angle, denoted by “W.” It’s well-suited for rolling manufacturing processes. For example, “W1/2-10” indicates a 1/2-inch external diameter and 10 threads per inch.
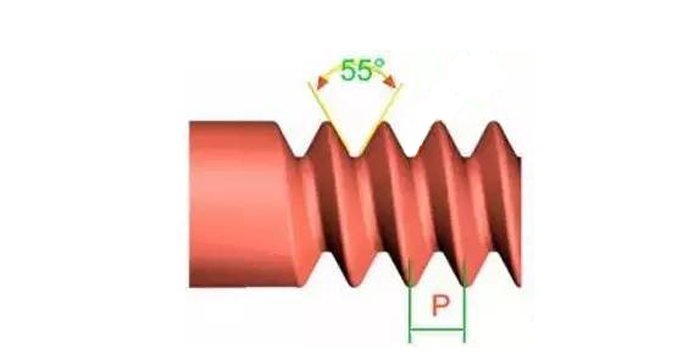
Knuckle Thread
Defined by German DIN standards, this thread is used for applications like light bulb sockets and rubber tubing connections. Its symbol is “Rd.”
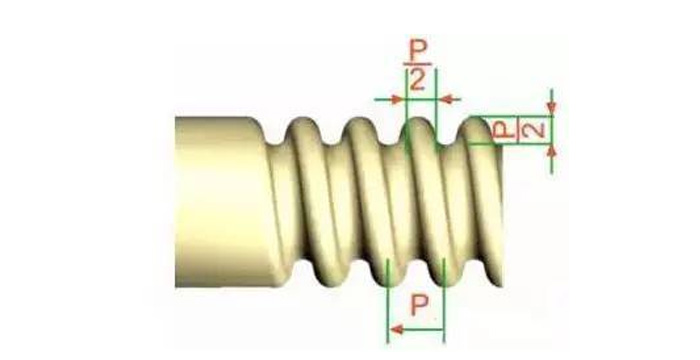
Pipe Thread
This thread is designed to prevent leaks, Pipe threads are commonly used in gas and liquid pipe connections. They have a 55-degree thread angle and come in two forms: straight pipe threads (labeled “P.S.” or “N.P.S.”) and tapered pipe threads (labeled “N.P.T.”), which have a 1:16 taper (equivalent to 3/4 inch per foot).
Square Thread
Square threads offer high transmission efficiency, surpassed only by ball screws. However, they can’t be adjusted with a nut once worn, limiting their use. They’re often found in vise screws and crane mechanisms.
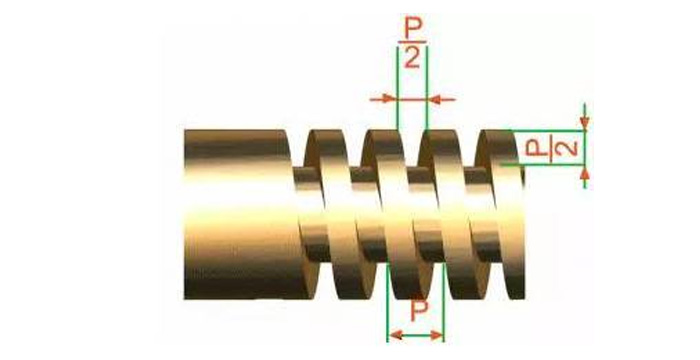
Trapezoidal Thread
With slightly lower transmission efficiency than square threads, trapezoidal threads have the advantage of being adjustable with a nut after wear. The metric version has a 30-degree thread angle, while the imperial version has a 29-degree angle. They’re commonly used for lathe lead screws and are designated with “Tr.”
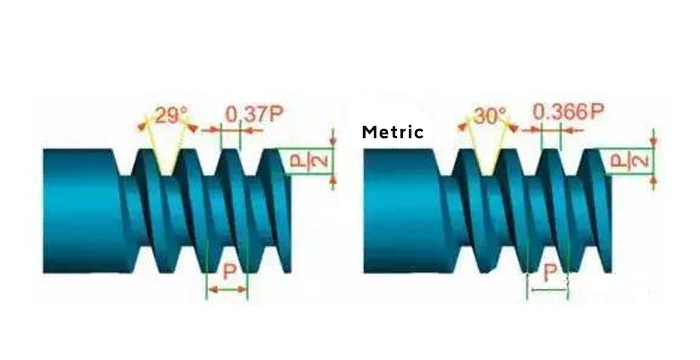
Buttress Thread
Also called a trapezoidal thread, this type is designed for unidirectional force transmission. It’s used in applications like screw jacks and presses, and its symbol is “Bu.”
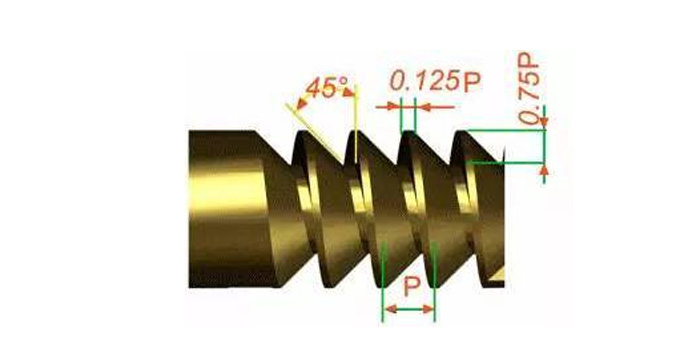
Precision and Strength of Screws
Screws are widely used for their precision and strength. In terms of precision, standard screws can be categorized into three grades—A, B, and C, which are based on their manufacturing accuracy, grades A and B are precision screws and grade C is coarse screws. For connection screws used in steel structures, grade C screws are generally used unless otherwise specified. There are significant differences in the manufacturing processes for screws of different precision grades. The shanks of grades A and B Screws are machined on the CNC lathes for smooth surfaces and precise dimensions. Their material performance grade is 8.8, but due to the complex manufacturing and installation process, they are expensive and rarely used in practice. Grade C screws are made from unprocessed round bars, which have less precise dimensions, and their material performance grade is either 4.6 or 4.8. They deform significantly during shear connections, but they are easy to install and have low production costs.
Carbon steel and alloy steel screws are classified into over ten grades in terms of strength, such as 3.6, 4.6, 4.8, 5.6, 6.8, 8.8, 9.8, 10.9, and 12.9. Screws with grades 8.8 and above are made from low-carbon alloy steel or medium-carbon steel and undergo heat treatment (quenching and tempering).
Make Your Idea Take Shape!
Materials for Screws
The common materials for manufacturing the screws include: Carbon steel, stainless steel, and copper.
Carbon Steel Screw
This is the basic type of steel used for screws. It offers good tensile strength and durability, However, carbon steel is prone to rust, so it’s often coated or treated (e.g., with zinc plating) to improve corrosion resistance. Carbon steel grades for screws include:
- Low-carbon steel: Q235(GB),1008,1015, 1018(AISI)
- Medium-carbon steel: 45# steel(GB), 1035, 1045(AISI)
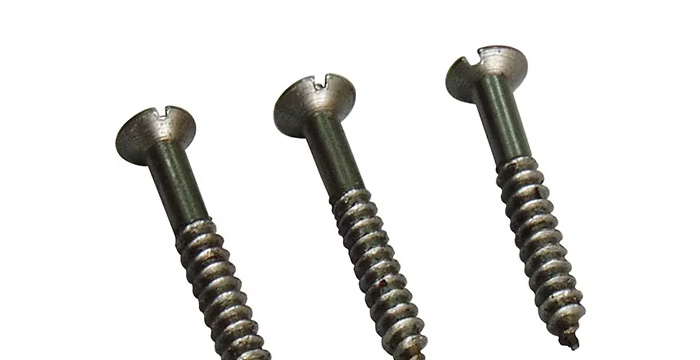
Stainless Steel Screw
Stainless steel contains chromium (at least 10-12%) and often nickel. It’s a popular choice for screws used in outdoor settings, marine environments, or medical equipment where rust prevention is critical. Stainless steel is more expensive than carbon steel. Stainless steel grades for screws include:
- Austenite stainless steel: 304, 316, 316L
- Martensite stainless steel: 410, 420.
Copper Screw
Pure copper screws are rare but used in specific areas that require excellent electrical or thermal conductivity, such as in electrical grounding systems. Copper is soft and prone to wear, so it’s often alloyed (e.g., into brass) to improve its mechanical properties. Copper alloy grades for screws include: H62, H65, H68.
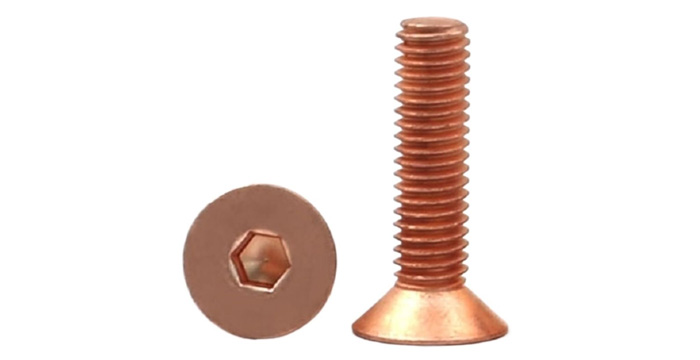
Surface Finishes for Screws
The primary purpose of a surface finish is to protect screws from environmental factors such as moisture, chemicals, and temperature extremes, which can lead to rust, degradation, or failure. Additionally, finishes can reduce friction during installation, enhance torque-tension relationships, and provide a polished look for visible applications.
Zinc Plating
Zinc plating is one of the most popular surface finishes for screws due to its cost-effectiveness and solid corrosion resistance. Applied through electroplating, a thin layer of zinc protects the underlying steel from rust by acting as a sacrificial anode. Variants include clear zinc (shiny finish) and yellow zinc (with added chromate for extra protection). Zinc-plated screws are widely used in construction, automotive, and general-purpose applications, though they may not suffice in highly corrosive environments like coastal areas.
Nickel Plating
Nickel plating offers a bright, attractive finish with good corrosion resistance and wear protection. It’s often used for decorative screws or in applications requiring moderate environmental resistance, such as household hardware or electronics. Nickel-plated screws also resist tarnishing, making them suitable for visible installations.
Black Oxide
Black oxide is a chemical conversion coating that provides a sleek, matte black appearance and mild corrosion resistance. It’s often paired with oil or wax to enhance protection. This finish is popular in firearms, tools, and machinery where aesthetics and low reflectivity are desired, though it’s less effective in highly corrosive conditions.
Finishes | Coating Thickness(μm) | Corrosion Resistance(Neutral Salt Spray Test) | Cost |
Black Oxide | 1 | 1-3 hours | Low |
Nickel Plating | Copper: 0.5-1 Nickel: 2-10 | 10-20 hours | Low |
Zinc Plating | 2-10 | 6-12 hours | Medium |