Introduction to Urethane Casting
Urethane casting, a process rooted in pouring liquid polyurethane resin into a mold and allowing it to solidify, offers a versatile method for creating parts with intricate details and complex geometries. The process commences with the fabrication of a master pattern, which is typically manufactured by 3D printing or CNC machining, around the master a mold is constructed using materials such as silicone or urethane rubber. Subsequently, the liquid resin is poured into the mold, which undergoes curing to take the shape of the desired part. Urethane casting is an efficient solution for producing small to medium-sized batches of parts, delivering flexibility and cost-effectiveness compared to other manufacturing techniques.
Comparison with Injection Molding
While injection molding excels in high-volume manufacturing, it demands substantial upfront investment in tooling, making it less feasible for smaller runs. On the other hand, Urethane casting offers a more cost-effective alternative for such production scales, enabling the creation of parts with comparable intricacy and surface finish. Moreover, urethane casting facilitates rapid iterations and modifications, making it an optimal choice for prototyping and small-batch production where flexibility and agility are paramount.
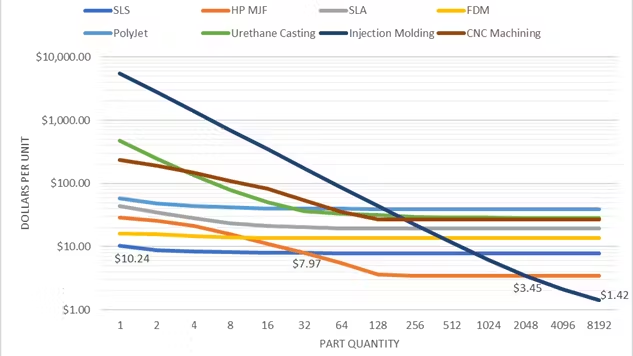
credit from Xometry
Urethane Casting Process
The urethane casting process can be broken down into the following steps:
- Acquire a master pattern either through CNC machining or Stereolithography (SLA) 3D printing.
- Submerge the master pattern into a container filled with liquid silicone to form a mold.
- Cut the fully solidified silicone mold into two halves and remove the master pattern from within.
- Pour urethane into the silicone mold and allow it to solidify, forming the casting. The silicone mold can be reused approximately 20 times before requiring replacement.
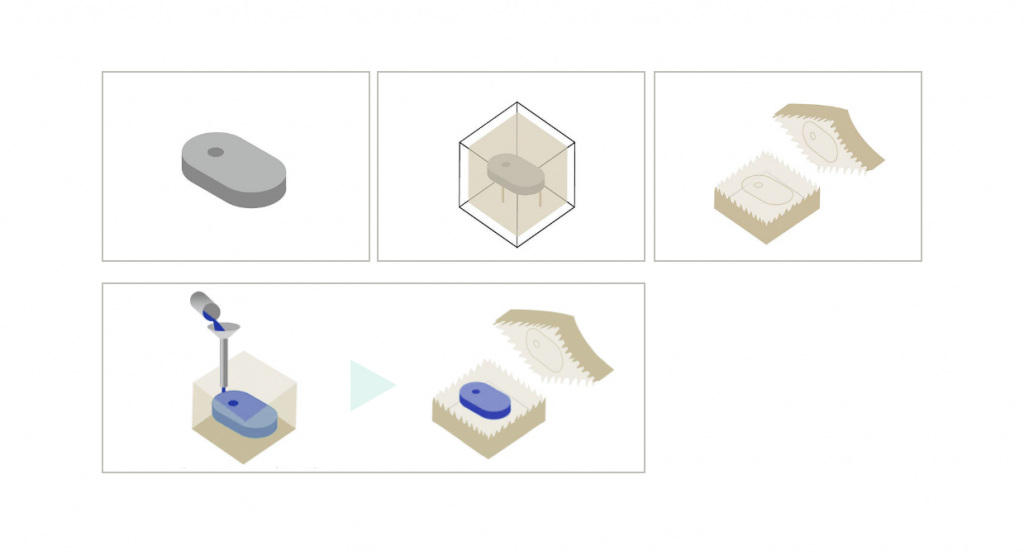
Urethane Casting Materials
Polyurethane resins are polymers with a wide range of properties and use. We offer a variety of polyurethane casting materials to suit your application:
- ABS-like
- Acrylic-Like
- Nylon-like material
- PC-like
- PP-like
- Rubber-Like
- Clear Rubber-Like
Advantages of Urethane Casting
Cost-Effectiveness: Urethane casting is particularly cost-effective for low production runs. It requires less initial investment in tooling compared to processes like injection molding, making it accessible for prototyping and small-scale production.
Flexibility in Material Selection: Urethane casting allows for the use of a wide range of materials with varying properties, including hardness, flexibility, and color. This versatility enables manufacturers to tailor parts to specific requirements, such as mechanical strength or aesthetic appearance.
Complex Geometry and Fine Detailing: The process reproduces intricate details and complex geometries with high precision. It can capture fine surface textures and features, making it suitable for producing parts with intricate designs or functional prototypes with precise specifications.
Quick Turnaround Time: Urethane casting offers relatively fast turnaround times compared to traditional manufacturing methods. Once the mold is prepared, parts can be produced rapidly, enabling quick iterations during the prototyping and development phase.
Design Tips for Urethane Casting
Tolerance
Urethane casting typically allows tolerances of around ± 0.015” or ± 0.003 per inch, with tighter tolerances available on a case-by-case basis.
A typical shrinkage rate of +0.15% occurs due to the thermal expansion of the urethane casting material and the silicone mold.
Wall Thickness
Parts should have a minimum wall thickness of 0.040” (1mm), although thinner walls down to 0.020” (0.5mm) can be achieved for small components.
Consistent wall thickness is encouraged to minimize shrinkage and deformation during curing.
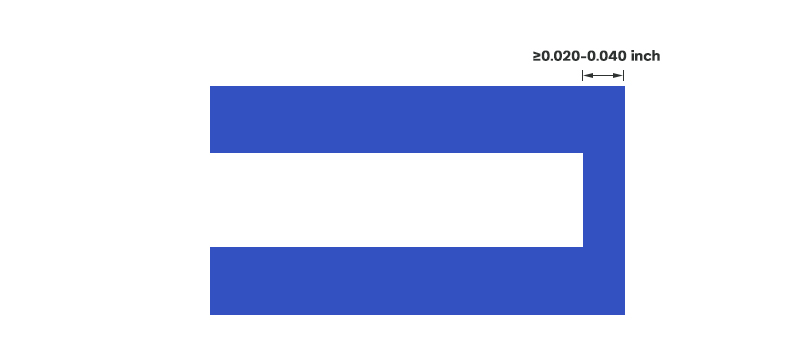
Draft
Draft angles of 3-5 degrees can reduce strain on molds and extend their lifespan.
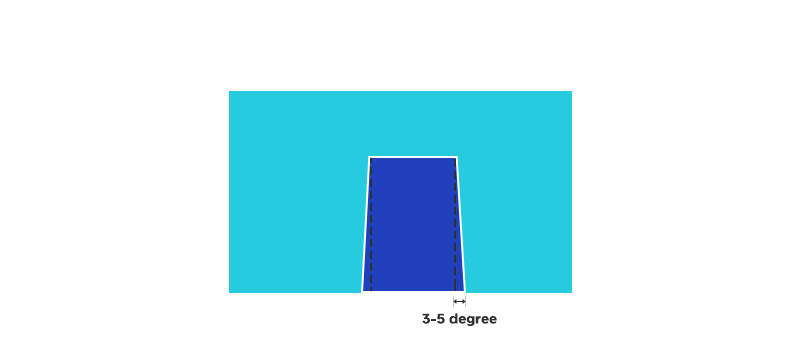
Ribs
Ribs should be oriented for maximum bending stiffness, with a height no more than three times their width.
The width of the rib where it meets the part wall should be between 40-60% of the wall thickness.
Interior corners should have a fillet radius of at least 25% of the part’s wall thickness for maximum strength.
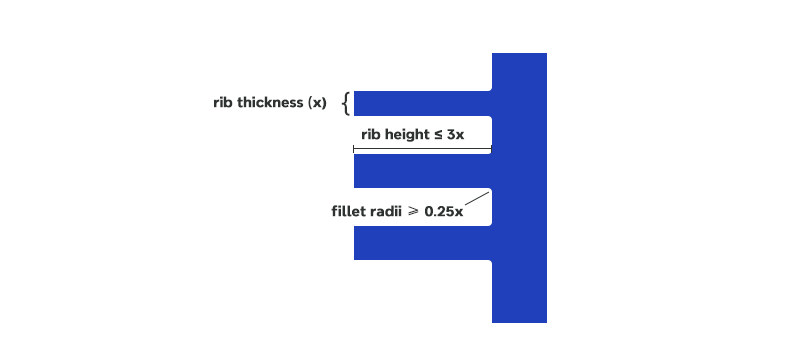
Bosses
Bosses facilitate the attachment of mating parts and should have a base radius of about 25% of the part’s wall thickness.
Interior boss corners should use a 0.060” (1.5mm) fillet radius to minimize thickness and reduce the likelihood of sinks.
Bosses should be no more than 60% of the nominal wall thickness to minimize shrinkage.
Applications of Urethane Casting
Low Volume Production: Urethane casting is an ideal choice for quickly and cost-effectively producing high-quality plastic prototypes, especially in cases of low production volumes where traditional tooling is not feasible.
Engineering Testing: Urethane casting, coupled with cost-effective tooling, simplifies engineering validation and design changes, making it easier and more economical. This also allows for functional testing and necessary certifications before mass production.
Aesthetic Models: Urethane castings can produce a variety of colors, textures, and finishes to achieve aesthetic cohesion. To determine the optimal colors for the final product, creating a silicone mold to produce multiple castings, each with different designs, facilitates internal discussions during meetings.
Advanced Prototype Production: Urethane castings are highly suitable for consumer testing and user evaluation due to their functionality and quality. The casting process allows for rapid changes for further testing or market deployment.