What is Weathering Steel?
Weathering steel, also known as atmospheric corrosion-resistant steel, is a low-alloy, high-strength steel that incorporates small amounts of alloying elements to enhance its resistance to corrosion in atmospheric conditions. Its corrosion resistance is 2 to 8 times greater than that of ordinary carbon steel, with the protective effect becoming more pronounced over time. Beyond its excellent weather resistance, weathering steel boasts superior mechanical properties and weldability, making it widely applicable in railway vehicles, bridges, and shipping containers.
Unlike stainless steel, weathering steel is not immune to rusting. Initially, it corrodes similarly to ordinary carbon steel, but its behavior diverges over time. After a period of rusting, trace elements such as copper (Cu) and phosphorus (P) accumulate on the steel’s surface, forming a dense, amorphous rust layer. This layer bonds tightly to the base metal, acting as a barrier that partially shields it from moisture and harmful ions in the atmosphere, thereby preventing further corrosion.
Weathering steel can be used with coatings, left uncoated, or subjected to stabilization treatments, with coating requirements identical to those for ordinary carbon steel. A standout advantage is its ability to be used uncoated, eliminating the need for paint. In areas with minimal air pollution or moderate humidity, weathering steel can be exposed directly to the atmosphere without painting. Typically, after about a year, the rust layer stabilizes, halting further corrosion and developing an aesthetically pleasing chocolate-brown hue. Free from issues like paint aging, this steel requires no maintenance coatings, significantly reducing upkeep costs and avoiding losses associated with painting-related disruptions.
Development History
Since the early 20th century, countries such as the United States, Germany, the United Kingdom, and Japan have conducted extensive research on weathering steel. As early as 1916, scientists in Europe and the U.S. discovered that copper enhances steel’s corrosion resistance in atmospheric conditions. That same year, the American Society for Testing and Materials (ASTM) initiated studies on atmospheric corrosion. Researchers like C.P. Larrabee compiled corrosion data, identified patterns, and explored underlying mechanisms. In the 1930s, U.S. Steel Corporation developed Corten steel—a high-strength, copper-bearing, low-alloy steel with superior corrosion resistance. By the 1960s, Corten steel was being used unpainted in buildings and bridges, with the most common variants being the high-phosphorus, copper-chromium-nickel Corten A series and the chromium-manganese-copper Corten B series. Weathering steel gained widespread adoption in Europe and Japan as well. Today, it is treated as a standard steel type internationally, with detailed specifications governing its development, application, and design. Table 1 outlines the key milestones in the global development of weathering steel.
In China, research on weathering steel and atmospheric exposure testing began in the 1960s. In 1965, the 09MnCuPTi weathering steel was successfully trial-produced, leading to the creation of China’s first weathering steel railway freight car. The National Science and Technology Commission and the Natural Science Foundation of China established a nationwide network of environmental corrosion test stations, initiating a 20-year, five-cycle data collection effort in 1983. Leveraging China’s resource advantages, researchers developed several steel grades, including Ansteel’s 08CuPVRE series, Wuhan Steel’s 09CuPTi series, Jinan Steel’s 09MnNb, Shanghai No. 3 Steel Plant’s 10CrMoAl, and 10CrCuSiV.
Grades of Weathering Steel
Below is an overview of some prominent weathering steel grades, including international standards and examples from key producers like those in the United States, Japan, and China.
Corten Steel (United States)
Corten steel, developed by U.S. Steel Corporation in the 1930s, is one of the most well-known weathering steel brands. It is divided into two primary series:
Corten A
- Composition: High phosphorus (P: 0.07%–0.15%), copper (Cu: 0.25%–0.55%), chromium (Cr: 0.5%–1.25%), nickel (Ni: 0.65% max), and traces of other elements like silicon (Si).
- Characteristics: Excellent corrosion resistance due to the high phosphorus content, which promotes a dense protective rust layer. It also offers good weldability and mechanical strength.
Corten B
- Composition: Lower phosphorus (P: ≤0.025%), copper (Cu: 0.20%–0.40%), chromium (Cr: 0.40%–0.65%), manganese (Mn: 0.50%–1.25%), and vanadium (V: 0.02%–0.10%).
- Characteristics: Focuses on higher strength and toughness rather than extreme corrosion resistance. The reduced phosphorus content makes it more suitable for thicker sections.
SPA-H (Japan)
- Standard: JIS G3125 (Japanese Industrial Standard)
- Composition: Copper (Cu: 0.25%–0.60%), phosphorus (P: 0.07%–0.15%), chromium (Cr: 0.30%–1.25%), nickel (Ni: ≤0.65%), silicon (Si: 0.25%–0.75%).
- Characteristics: A high-strength weathering steel with excellent corrosion resistance, designed for welded structures. It forms a stable rust layer quickly, offering durability in humid and industrial environments.
Chinese Weathering Steel Grades
China has developed several weathering steel grades, often tailored to its resource availability and industrial needs:
Q235NH
- Composition: Manganese (Mn: 0.20-0.60%), copper (Cu: ≤0.15%), phosphorus (P: ≤0.03%).
- Characteristics: Yield strength ≥ 235 MPa, tensile strength 360-510 MPa, corrosion resistance is 2-3 times that of common carbon steel, suitable for low-load applications such as building curtain walls and guardrails.
Q295NH
- Composition: C≤0.16%、Mn 0.50-1.00%、Cu 0.20-0.60%、Cr 0.30-0.80%.
- Characteristics: Yield strength ≥ 295 MPa, tensile strength 430-570 MPa, with better weather resistance than Q235NH, commonly used in railway vehicles and general structural components.
Q355NH
- Composition: C≤0.16%、Mn 0.90-1.50%、Cu 0.25-0.55%、Cr 0.30-1.25%.
- Characteristics: Yield strength ≥ 355 MPa, tensile strength 470-630 MPa, elongation ≥ 22%, good weldability, suitable for container and machinery manufacturing.
Q460NH
- Composition: C≤0.18%、Mn 1.00-1.60%、Cu 0.25-0.55%、Cr 0.40-1.25%.
- Characteristics: Yield strength ≥ 460 MPa, tensile strength 570-730 MPa, corrosion resistance is 3-4 times that of plain carbon steel, used for heavy machinery and high-load structures.
Q295GNH
- Composition: C ≤ 0.12%, P 0.07-0.15%, Cu 0.25-0.55%, Cr 0.30-1.25%
- Characteristics: Corrosion resistance is 4-6 times that of plain carbon steel, with a dense rust layer suitable for exposed applications such as sculptures and outdoor facilities.
Q345GNH
- Composition: C ≤ 0.12%, P 0.07-0.15%, Cu 0.25-0.55%, Ni ≤ 0.25%
- Characteristics: Yield strength ≥ 345MPa, tensile strength 490- 630 MPa, excellent resistance to marine atmospheric corrosion, used in coastal buildings and wind turbine towers.
Q460GNH
- Composition: C ≤ 0.12%, P 0.07-0.15%, Cu 0.25-0.55%, Cr 0.50-1.50%
- Characteristics: Yield strength ≥ 460MPa, tensile strength 570- 730 MPa, high phosphorus content accelerates rust layer stabilization, suitable for chemical containers.
Make Your Idea Take Shape!
European Standards (EN 10025-5)
The European standard EN 10025-5 specifies weathering steels under the “S” (structural steel) designation with a “W” for weathering properties:
S355J2W
- Composition: Copper (Cu: 0.25%–0.55%), chromium (Cr: 0.40%–0.80%), phosphorus (P: ≤0.035%), manganese (Mn: 0.50%–1.50%).
- Characteristics: Offers a yield strength of 355 MPa and excellent weathering properties, forming a stable rust layer over time.
S355K2W
- Composition: Similar to S355J2W, with slightly adjusted alloying for improved toughness (K2 indicates higher impact resistance).
- Characteristics: Enhanced low-temperature performance alongside corrosion resistance.
ASTM Standards (United States)
The ASTM provides specifications for weathering steels, often overlapping with Corten grades:
ASTM A588
- Grades: A588 Grade A, B, C, K
- Composition: Varies by grade; typically Cu: 0.25%–0.40%, Cr: 0.40%–0.70%, Ni: ≤0.50%, P: ≤0.04%, with vanadium or niobium in some grades.
- Characteristics: High-strength, low-alloy steel with a minimum yield strength of 345 MPa. Grade K includes additional elements for superior corrosion resistance.
ASTM A242
- Composition: Copper (Cu: 0.20% min), chromium (Cr: 0.50%–1.25%), phosphorus (P: ≤0.15%).
- Characteristics: One of the earliest weathering steel standards, offering good corrosion resistance for thinner sections.
Key Features Across Grades
Corrosion Resistance: All grades develop a protective rust patina that slows further corrosion, with variations depending on alloy content (e.g., higher P in Corten A, higher Cr in S355J2W).
Mechanical Properties: Yield strengths typically range from 235 MPa (e.g., SPA-H) to 355 MPa (e.g., S355J2W, A588), with some grades optimized for toughness or weldability.
Customization: Grades like China’s 08CuPVRE incorporate rare earths, while others like 10CrMoAl target specific environments (e.g., industrial atmospheres).
Mechanical Properties of Weathering Steel
The mechanical properties of weathering steel, detailed in the following table, are comparable to those of high-carbon or low-alloy steel. However, weathering steel is required to exhibit good cold-working performance.
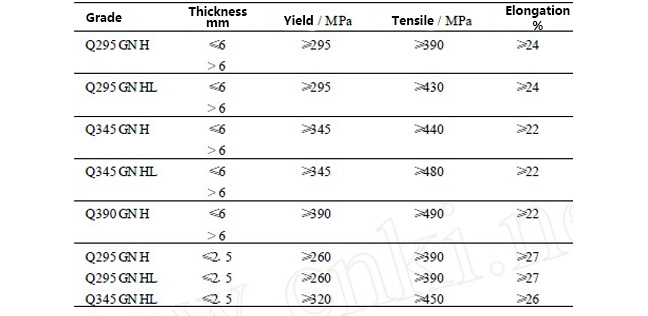
The microstructure of weathering steel typically consists of ferrite and pearlite. Oxide inclusion levels must not exceed Grade 2, sulfide inclusions should not surpass Grade 2.5, and grain size should be no coarser than Grade 7.
Alloying Elements of Weathering Steel
Compared to ordinary carbon steel, weathering steel offers superior resistance to atmospheric corrosion due to alloying elements that reduce the conductivity of the rust layer and impede the rapid growth of corrosion products. Its corrosion resistance becomes evident after prolonged exposure. Alloying elements that enhance atmospheric corrosion resistance must: (1) have higher solubility in iron than in the rust layer, (2) form a solid solution with iron, and (3) increase the steel’s electrochemical potential. Studies indicate varying effects of different alloying elements on weathering performance.
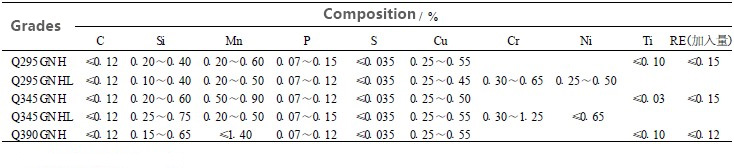
Carbon
Carbon negatively impacts atmospheric corrosion resistance and affects weldability, cold brittleness, and stamping properties. Typically, its mass fraction in weathering steel is limited to below 0.12%.
Copper and Sulfur
Adding 0.2%~0.4% copper significantly enhances corrosion resistance in rural, industrial, or marine atmospheres compared to ordinary carbon steel. Copper notably counteracts the detrimental effects of sulfur, with its effectiveness increasing as sulfur content rises, due to the formation of insoluble sulfides. Reducing residual sulfur to 0.01% elevates carbon steel’s weathering performance to near Corten B levels and general alloy steel to Corten A levels.
Phosphorus
Phosphorus is one of the most effective elements for boosting atmospheric corrosion resistance. It dissolves uniformly in steel, forming a dense protective film on the surface. Optimal corrosion resistance is achieved at 0.08%–0.15% phosphorus content.
Chromium
Chromium forms a dense oxide film on the steel surface, enhancing passivation and slowing rust growth. Typically, chromium content ranges from 0.4%–1.0% (up to 1.3%), with pronounced effects when combined with copper.
Nickel
Nickel, a stable element, positively shifts the steel’s self-corrosion potential, improving stability. Atmospheric exposure tests show that approximately 4% nickel significantly enhances corrosion resistance in coastal environments.
Calcium
Trace amounts of calcium improve overall atmospheric corrosion resistance and prevent rust runoff during use. Calcium forms CaO and CaS, which dissolve in the surface electrolyte film, increasing alkalinity, reducing corrosiveness, and promoting the formation of a dense, protective α-FeOOH rust phase.
Manganese
Opinions on manganese’s effect on corrosion resistance vary. Most researchers agree it enhances resistance to marine atmospheres but has little impact in industrial settings. Manganese content typically ranges from 0.5%–2.0%.
Molybdenum
At 0.4%–0.5%, molybdenum reduces corrosion rates by over 50% in atmospheric conditions, particularly in industrial environments.
Rare Earth Elements
Rare earth elements (RE), added at ≤0.2%, are used in chromium- and nickel-free weathering steels. Highly reactive, they act as deoxidizers and desulfurizers, refining grains, reducing harmful inclusions, and enhancing corrosion resistance by minimizing corrosion initiation sites.
Weathering steel applications
Weathering steel plate not only has good weather resistance, but also has a certain degree of processability. It can be cut, welded, engraved and other processing techniques to meet a variety of complex design requirements. Especially in modern construction and, the application of weathering steel plate has a broad prospect.
Construction
Weathering steels are mainly used in the construction field to manufacture steel structures, bridges, highway guardrails, etc.. Due to its excellent corrosion resistance, weathering steel can greatly extend the service life of these structures, reduce the frequency of maintenance and replacement, and lower maintenance costs. At the same time, the unique appearance of weathering steel can bring a unique aesthetic to the building.
Rail and Transport
In the railway and transport sector, weathering steels are mainly used in the manufacture of railway tracks, vehicles, containers, etc. These facilities are often exposed to harsh environments. These facilities are often exposed to harsh environmental conditions, such as rain, snow, wind, sand, etc. Weathering steels provide excellent corrosion protection to ensure the long-term stable operation of the facilities.
Agriculture
Applications of weathering steel in the agricultural field mainly include agricultural machinery and greenhouse structures. As weathering steel has good corrosion resistance and anti-aging properties, it can adapt to various harsh environmental conditions and provide reliable support and protection for agricultural production and facilities.
Petrochemical field
In the petrochemical industry, weathering steel is mainly used to manufacture storage tanks, pipelines, valves and other facilities. These facilities are often exposed to corrosive media, such as acids, alkalis, salts, etc. Weathering steel can provide good corrosion protection and extend the service life of the facilities.
Conclusion
Weathering steel’s corrosion resistance and cost-effectiveness make it a vital material with enduring relevance. Future research should draw on global expertise while leveraging China’s unique resources and technical strengths. The focus should be on developing high-efficiency, high-quality weathering steels tailored to China’s environmental and regional needs, alongside rapid rust stabilization techniques for surface layers.