Cast aluminum offers advantages such as high strength, excellent corrosion resistance, and ease of machinability, which makes it a favored choice across industries such as automotive, aerospace, electronics, and consumer goods. In this article, we will discuss cast aluminum’s composition, manufacturing processes, properties, applications, quality control, and emerging trends.
What is Cast Aluminum?
Cast aluminum alloys are aluminum-based alloys made into shape by some kind of casting process. Unlike wrought aluminum, which is shaped by mechanical processes, such as rolling or extrusion, cast aluminum is melted and poured into molds, then cooled and shaped into the desired shape. The casting process allows for the creation of very complex geometries that are difficult to produce by any other methods.
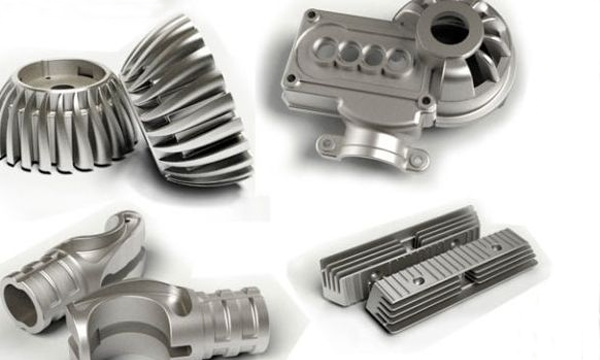
Composition of Cast Aluminum Alloys
Cast aluminum alloys consist primarily of aluminum (Al) together with one or more alloying elements, such as silicon (Si), copper (Cu), magnesium (Mg), zinc (Zn), and manganese (Mn).
These elements are added as alloying elements to enhance specific characteristics.
Elements | Effects |
Silicon (Si) | Improves fluidity, reduces shrinkage, and enhances wear resistance. |
Copper (Cu) | Increases strength and hardness but may reduce corrosion resistance. |
Magnesium (Mg) | Enhances strength and corrosion resistance, especially in marine environments. |
Zinc(Zn) | Improves castability and strength, often used in high-strength alloys. |
Manganese(Mn) | Improves toughness and resistance to cracking. |
Types of Cast Aluminum
The classification of cast aluminum alloys is based mostly on the elemental nature of the principal alloying elements, which, in turn, decisively influence the alloy’s properties. There are four major categories: A1-Si, Al-Mg, Al-Cu, and Al-Zn. Each has its characteristics and suitability for various jobs in several industries.
Aluminum-Silicon Alloys (Al-Si)
Aluminum-silicon alloys are some of the most prominently used cast aluminum alloys in manufacturing because of their extraordinary casting properties and good wear resistance. These alloys contain silicon between 10% to 25% and low density, having low coefficients of thermal expansion and high specific strength. These properties made them apt for components such as engine blocks, cylinder heads, and wheels.
Examples of Grades: A356, A360, A413
Aluminum-Magnesium Alloys (Al-Mg)
Al-Mg alloys remain significant because of their corrosion resistance, moderate-high strength, and good weldability. With magnesium content typically varying between 0.5-12%, enhanced mechanical properties are displayed by these alloys, which find usage in aerospace applications in search of high-strength-lightweight materials like marine structures, aircraft landing gears, and food and beverage packaging.
Aluminum-Copper Alloys (Al-Cu)
AI-Cu alloys possess good strength and excellent machinability for their copper contents, generally ranging from 2-10%. The major applications of these are aerospace, automotive, and structural engineering.
Example of Grades: A295
Aluminum-Zinc Alloys (Al-Zn)
AI-Zn alloys are known for their higher strengths, especially when heat-treated. Given their high performance, Al-Zn alloys are widely used in aerospace manufacturing applications.
Example of Grades: A712.2
Common cast aluminum alloys
A356: An automotive and aerospace material having good ductility and strength.
A360: Well known for its castability, strength, and corrosion resistance, it is commonly used in automotive parts such as wheels and engine components.
A380: Well regarded for being fluid and pressure-tight, it is largely used for die casting.
A390: A versatile material with higher strength, greater hardness, and better corrosion resistance.
A413: An alloy with good castability and remarkable pressure tightness; an alternative to A380.
ADC12: A widely-used alloy in Asia for die casting with good mechanical properties and castability.
Processes of Cast Aluminum
The melting operation is the first step in the production of cast aluminum. This involves melting raw materials, typically primary aluminum, recycled aluminum, and alloying elements. The melting process occurs in furnaces with 700°C to 800°C. Key considerations during melting include:
Oxidation prevention. Aluminum oxidizes readily upon exposure to air, forming a layer of aluminum oxide (Al2O3). Inert gases or fluxing agents are employed to reduce oxidation.
Alloy homogeneity. Using a proper way of mixing alloying elements ensures that uniform composition and properties are obtained.
There are numerous methods of casting for the production of cast aluminum parts, all with their advantages and disadvantages.
Sand Casting
This sand-casting process is one of the oldest and most versatile in aluminum casting. It is performed by making a permanent mold from a sand mixture and pouring molten metal into this mold. The method works quite well for larger, more complex aluminum parts and allows flexibility as regards the size and shape of the part.
Advantages: Low cost, suitable for large and complex parts, and flexible design options.
Disadvantages: Compared to other methods, lower dimensional accuracy and surface finish.
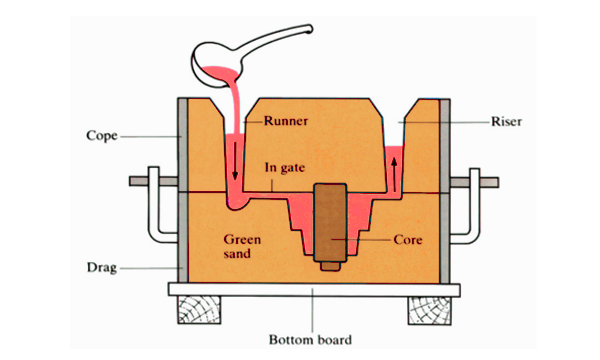
Die Casting
Die casting represents the method of speed and efficiency. The process uses the injection of molten aluminum directly into a die or mold under very high pressure.
Advantages: High production rates, excellent dimensional accuracy, and smooth surface finish.
Disadvantages: High initial tooling costs, limited to smaller casting.
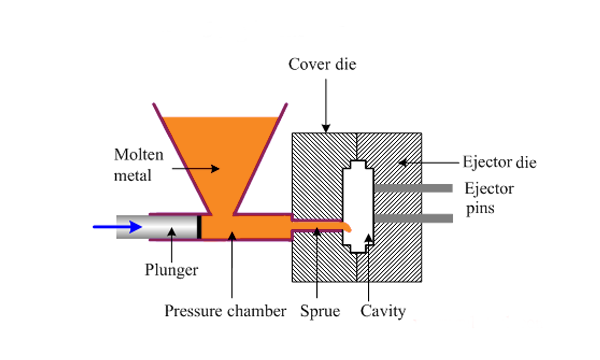
Investment Casting
In investment casting, a wax pattern is coated with a ceramic slurry to produce a mold, heated to melt the wax, and then filled with molten aluminum. It is well-suited in the production of thin-wall aluminum cast parts, with a minimum wall thickness of 0.40mm.
Advantages: High precision, Excellent Surface Finishing, and Potential to generate complex shapes.
Disadvantages: Costly and time-consuming process.
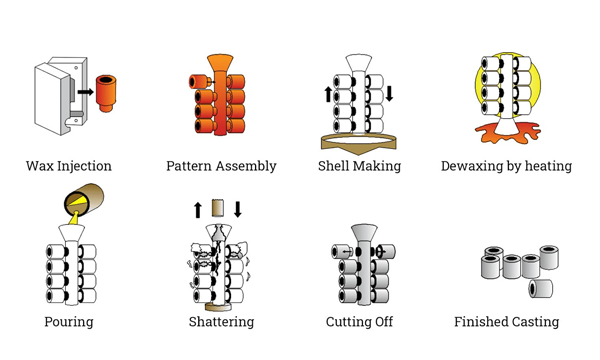
Permanent Mold Casting
The permanent mold casting technique involves using metal molds that can be reused. This process consists of pouring molten aluminum into the permanent mold through gravity or low pressure. This method is suited for moderate volumes of aluminum cast parts.
Advantages: Good surface finish, accurately dimensioned, and faster production time when compared to sand casting.
Disadvantages: Tooling is more expensive and limited to simple geometries.
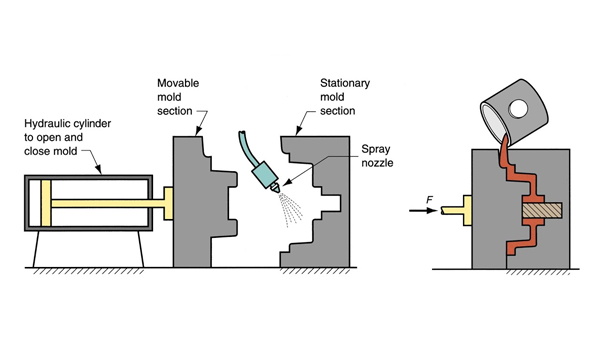
Properties and Advantages of Cast Aluminum
Mechanical properties
Cast aluminum alloys have a range of mechanical properties based on their composition and prevailing heat treatments.
Tensile strength | Yield strength | Elongation | Hardness | Density |
100-565 MPa | 30-525 MPa | 0.5-28% | 25-170 HB | 2.57-2.95 g/cm³ |
Light Weight
Lightweight is another great attribute of cast aluminum, it weighs about 2.57-2.95 g/cm³, making it lightweight compared to materials like cast iron and steel. This lower weight provides it with a high strength-to-weight ratio that is beneficial when both strength and lightweight are required.
Corrosion Resistance
Cast aluminum alloys are covered on the surface with an oxide layer, which forms a protective shield, providing these alloys with excellent corrosion resistance. For this reason, they are used in applications in corrosive and hostile environments such as marine and automotive components.
High Thermal and Electrical Conductivity
Cast aluminum is appropriately processed for heat exchangers, electronic housings, and electrical components since aluminum is also characterized by high thermal and electrical conductivity.
Thermal conductivity: 87-233 W/m·K
Electrical conductivity: 21-45 %
High Quality
Cast aluminum alloys provide good dimensional accuracy and surface finish. The dimensional tolerance normally ranges from IT6 to IT7, and in certain cases, can reach IT4. The surface roughness is commonly in the range of Ra 5 to Ra 8, which reduces their requirement for further post-processing. It should also be noted that cast aluminum alloys provide higher strengths and hardness than sand-cast parts, strength is normally enhanced by over 25% to 30%, while elongation is reduced by about 70%. The mechanical properties, although there is a drop in elongation, are still suitable for many applications. Moreover, aluminum casting can mold thin-walled and complex parts, such as zinc alloy castings, having a minimum wall thickness of 0.3mm, and aluminum castings having a minimum of 0.5mm; the production has casting holes with diameters as small as 0.7mm, and the threads have a minimum pitch of as low as 0.75mm.
Economic Benefits
Because of the great accuracy and surface finish of cast aluminum parts, they generally require no or only slight additional machining operations. Such improvement pertains to the utilization of metals, reduction of extensive machining equipment, and labor savings. Besides, cast aluminum parts are relatively cheaper due to the efficiency of the casting process.
Quality Control in Cast Aluminum Manufacturing
Defect Detection
Porosity, shrinkage, cracks, and inclusions are a few defects that may occur while casting aluminum. There are various methods used to detect defects, which include:
- Visual Inspection: Observing surface defects.
- X-ray and CT Scans: Detecting internal defects.
- Ultrasonic Testing: Measuring internal soundness and thickness.
- Dye Penetrant Inspection: Those for revealing surface cracks.
Dimensional Accuracy
Accuracy in casting is very critical, essentially for the correct functioning and fitting. Various techniques such as coordinate measuring machines (CMM) and laser scanning systems are used to ensure dimensional accuracy.
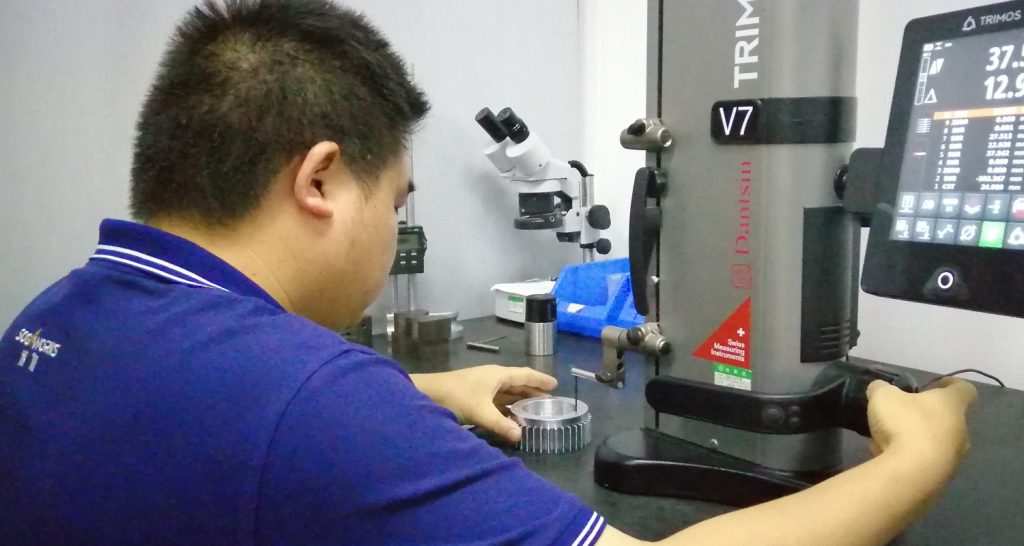
Surface Finish
Surface finish is obtained by anodizing, polishing, and coating. Anodizing is a commonly used surface treatment that increases corrosion resistance and enhances appearance.
Future Trends in Cast Aluminum Manufacturing
Additive Manufacturing
Metal 3D printing is gaining popularity at a fast pace, providing an efficient and fast way of constructing complex geometries while wasting little material. It is exceedingly good for prototyping and small batches.
Sustainable Manufacturing
Metal has a much longer lifespan and the recycling process of aluminum requires only around 5% of energy and hence comes across to be more environment-friendly. Industries are focusing successfully on closed-loop recycling systems for waste minimization.
Advanced Alloys
Research is still in progress to synthesize the new cast aluminum alloys possessing superior properties like higher tensile strength, improved thermal conductivity, and corrosion resistance.
Conclusion
Cast aluminum is one of the most critical materials in modern-day manufacturing, giving a mix of lightness, strength, and versatility sought by many industries. Understanding cast aluminum’s composition, manufacturing process, properties, and applications enables manufacturers to make use of cast aluminum in a way that lends itself to the creation of innovative, high-performance products. As the industry evolves, advancements in lightweight, additive manufacturing, and sustainability will expand the horizons of cast aluminum even further. This guide has been a repository of information for anyone wishing to gain a deeper knowledge of cast aluminum and its position in the manufacturing environment.