The CNC metal cutting process uses computer-controlled machines to cut and shape metal into desired shapes. There are many applications of the metal-cutting process, each with its specific requirements. We’ll explain the definitions and processes, and help you choose one.
What is CNC Metal Cutting?
CNC metal cutting is a process that uses computer numerical control (CNC) to cut extra materials on metal and then create desired geometries. The process employs a cutter program and codes to direct the cutting tool’s movements, thus reducing human engagement and enhancing precision.
Processes and How They Work
We can categorize the metal cutting processes into two main groups: mechanical and abrasive. Mechanical processes use a cutting tool or force to cut the partial material from metal. In previous articles, we provided a more detailed introduction, and in the following, we will introduce several major abrasive processes:
CNC Laser Cutting
Laser is a thermal manufacturing process. It uses a focused laser beam to cut metal material. The high-power laser beam melts or vaporizes the metal materials, and a computer program guides the laser’s path.
CNC laser cutting is primarily used to cut sheet metal. The metal’s thickness can be up to 25mm. It has broad applications in a variety of industries; for example, automotive companies use it to produce body panels, and medical equipment manufacturers use it for surgical instruments.
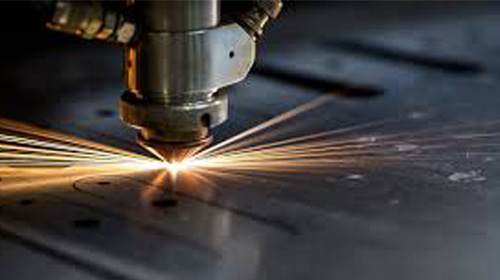
Waterjet Cutting
Waterjet cutting is a cold process that uses highly pressurized water as a cutting tool to remove partial material for metal workpieces. It uses a high-pressure pump to generate a water stream that mixes abrasive particles and water, which is used for cutting the metal. It is contact-free and can make linear, non-linear, and internal cuts in a workpiece.
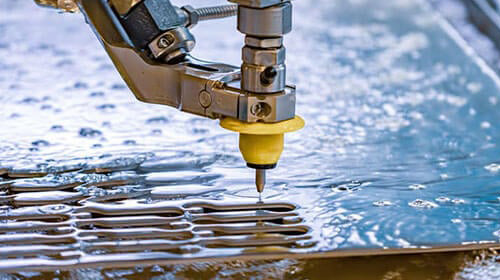
Plasma Cutting
Plasma cutting uses electrically conductive gas to cut metals. It uses the heat generated by the high-temperature plasma arc to melt the metal at the notch of the workpiece and removes the molten metal with the momentum of the high-speed plasma.
Plasma cutting is used primarily to cut metals with electrical conductivity.
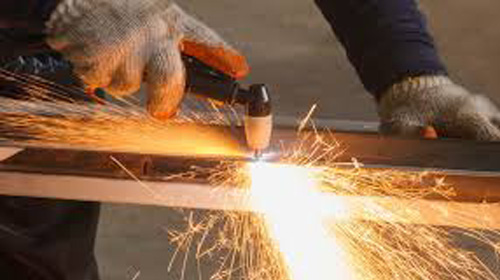
Wire EDM
Wire Electrical Discharge Machining (EDM) uses electrical discharges to cut metals. It uses a thin wire to generate electrical sparks; these sparks erode the metal and turn it into a desired shape. In the cutting process, the metal is submerged in a dielectric fluid.
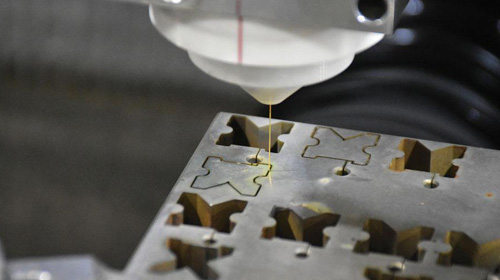
Criteria | Laser cutting | Waterjet cutting | Plasma cutting | Wire EDM |
Cutting tool | Laser beam | Water jet with abrasive | Ionized gas | Electrically charged wire |
Materials | Metals, plastics, wood | Metals, glass | Metals | Metals |
Max. materials thickness | 25mm | 100mm | 30mm | 300mm |
Cutting Speed | High | Moderate | High | Low |
Other Processes
Other metal cutting processes include CNC milling, CNC turning, shearing, punching, drilling, and more. They are mostly mechanical technologies that use sharp cutting tools to cut the metal.
How to Choose A CNC Metal Cutting Process
We’ve covered at least four different types of CNC metal cutting processes above; if you’re not new to the CNC machining industry, you may have learned about a variety of other metal cutting processes. Perhaps you’re wondering how to select the best cutting process for your metal parts. Now, let’s explore 2 key considerations you should be aware of before making your decision.
Characteristics of material. Every cutting process has some limitations. Laser cutting is mostly useful for metal plates with thicknesses up to 30mm, and it is less effective on highly reflective metals such as copper and aluminum. Similarly, plasma cutting and wire EDM are mostly appropriate for metals that possess electrical conductivity. Waterjet cutting has the ability to cut a variety of metals, albeit the resulting surface quality is coarser compared to other methods.
Requirements for precision. Laser cutting can achieve a tolerance of ±0.01mm, however, the accuracy of laser cutting diminishes when cutting heavy metal (thickness exceeding 25mm). Plasma cutting has a tolerance of ±0.2mm, it is less accurate than other methods and not recommended for products that require high precision features. The precision of wire EDM can be regulated to a tolerance of ±0.05mm or even more precise, however, It has a reduced cutting speed. The tolerance range for waterjet cutting is typically between ±0.1mm and ±0.2mm, but the quality of the cut edge is comparatively poorer.
Other factors you should take into considered include budget, tool requirements, delivery time and more.
New Trends in CNC Metal Cutting
Industry 4.0 and the Industrial Internet of Things (IIoT) are revolutionizing the manufacturing sector through the implementation of interconnected machinery and the minimization of human intervention. CNC machines are emerging at the forefront of manufacturing, as advancements in technology such as artificial intelligence and machine learning empower machines to effectively communicate and comprehend processes. Anticipatory maintenance initiatives are being established through the utilization of sensors and real-time data gathering, resulting in enhanced safety measures, reduced expenses, and increased customer contentment. The Industrial Internet of Things (IIoT) facilitates seamless data sharing between Original Equipment Manufacturers (OEMs).
Manufacturers are increasingly prioritizing sustainability by implementing measures to decrease emissions, minimize energy usage, and mitigate waste production. Machine shops are implementing greater levels of automation, placing a high importance on the value of raw materials, and engaging in partnerships with original equipment manufacturers (OEMs) to promote the reuse and recycling of resources.
5-axis and 6-axis CNC machining are increasingly prevalent techniques, enabling more accurate machining, fewer mistakes, and higher cutting speeds. There is an anticipated increase in the incorporation of an additional axis in certain CNC equipment, which will enhance its versatility and efficiency.