Sand blasting is a technique that is commonly used for cleaning, roughening and surface preparation. It uses compressed air to propel abrasive particles at high speed to remove rust, paint and contaminants on part surfaces. This process is vital in manufacturing for proper adhesion of coatings and the long life of materials. This article will explore the working principles, equipment types, common abrasives, and functions of the sand blasting process.
Overview of Sand Blasting
Sand blasting uses compressed air to blast tiny particles at high speeds onto a part’s surface. It is used for cleaning, roughening, removing rust, or stripping paint from the surface of the part. The force of the abrasives changes the physical properties. Sandblasting is very important in many fields, and it serves as a controlled surface finish through mechanical action.
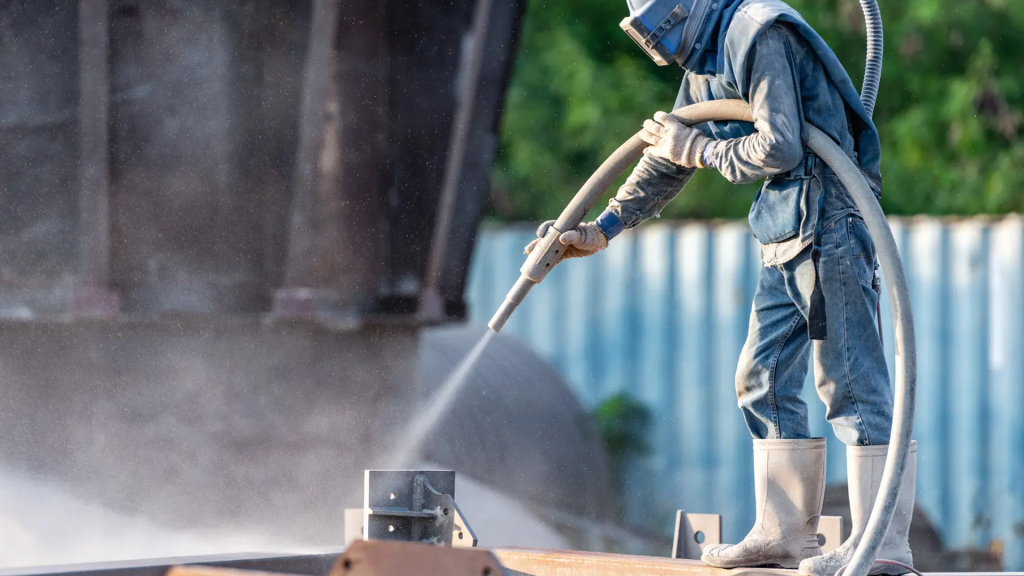
The sand blasting process begins in the 1870s. General Benjamin Chew Tilghman noticed the capability of sand to abrade glass that was used for windows in the desert, and he then obtained a patent. In 1904, An improvement was introduced by Thomas Wesley Pangborn, who added compressed air to the process. This change made the process adaptable and efficient and made it widespread use in various industries.
Steps of Sand Blasting
- Preparation: Make sure to choose the right sandblasting equipment and abrasives, according to the part material, shape, and size. Ensure that all equipment is in working condition, including compressor pressure and the gun nozzle. A safe environment must be ensured such as wearing safety glasses, masks, and protective clothing.
- Fixing the workpiece: Ensure the workpiece is secured on the workbench to avoid movement during blasting. This keeps the process even and accurate. Special fixtures are needed to keep large or oddly shaped pieces in place.
- Setting the equipment: Adjust the settings per the workpiece and goals. This includes air pressure adjustments, distance setting between the gun and the workpiece, the angle of the gun, and the abrasive flow rate. For thin pieces, set a lower pressure to avoid damage. and increase the abrasive flow rate for rough surface.
- Starting blasting: Once everything is ready, the workpiece will be held in the gun and moved with a pre-defined path and speed. Keep the movement smooth to avoid overblasting or underblasting.
- Quality Check: After blasting, inspect the workpiece for cleanliness and roughness. If any areas are not fully treated, do some more blasting on those areas.
- Cleaning Up: Once everything is complete, clean up the area, collect any unused abrasives, and store the equipment.
Sandblasting Equipment
According to the abrasive supply method, sandblasting equipment can be divided into 3 types:
Suction Sandblaster
The suction-feed sandblaster operates using compressed air. Because of the high-speed airflow in the spray gun, there is a lower pressure in the gun that causes abrasives to be sucked in through a pipe. The abrasives are subjected to a pressurized air beam and propelled toward the surface needing to be treated.
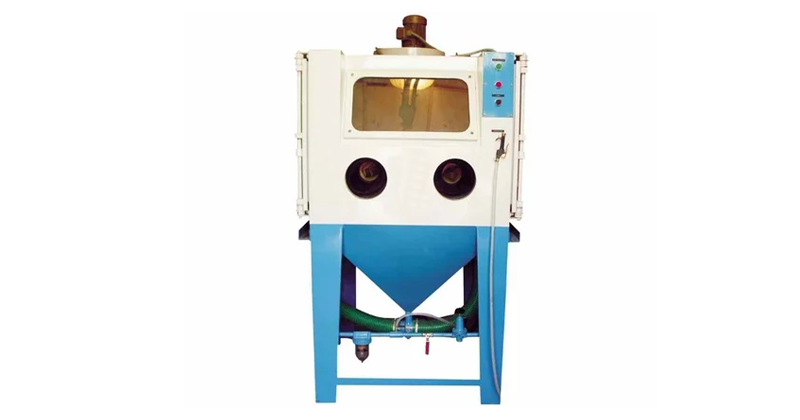
Pressure Sandblaster
The pressure-feed sandblaster also operates using compressed air. In this system, compressed air pressurizes a tank where abrasives are mixed. The abrasives are pushed into the conveying pipe through a valve, then accelerated by the air and sprayed onto the surface. abrasives mixed with air in a tank are pressurized with compressed air pushed through a conveying pipe by a valve and blasted on the surface.
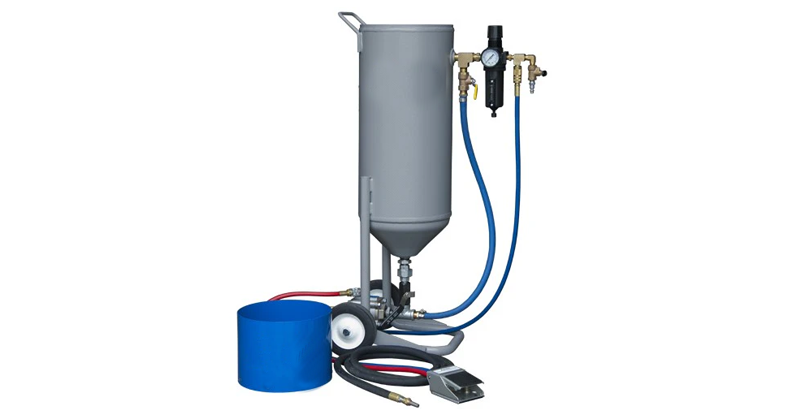
Wet Sandblaster
The wet sandblaster uses a grinding fluid pump to supply a mixture of abrasives and water into the spray gun. Compressed air then accelerates the fluid as it enters the gun and sprays it onto the surface. This method combines abrasives with water to help clean and treat the surface.
A wet sandblaster uses a pump to carry a mixture of water-based abrasives into the blast gun. The air compresses the fluid into the gun, where it is thereafter projected onto a surface requiring treatment.
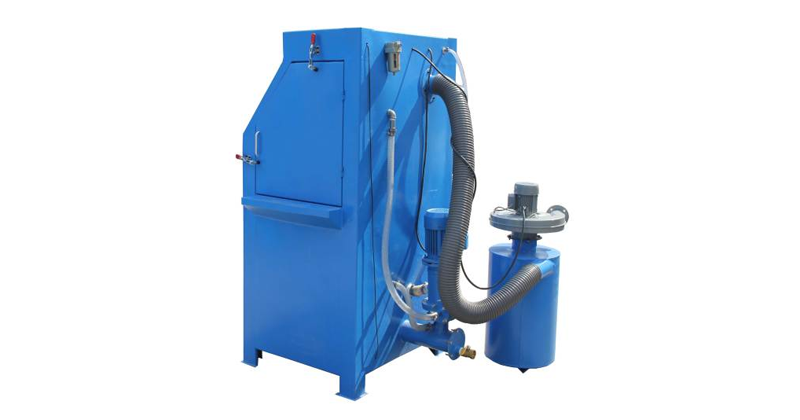
Sand Blasting Media
Aluminum Oxide
The most common abrasive for sand blasting. Aluminum oxide is sharp, durable, and can be reused many times. It comes in different hardness grades and particle sizes, making it suitable for a wide range of projects.
Glass Beads
Glass beads are safe, non-toxic, and free of heavy metals and silica. Their spherical shape helps polish to leave a bright and smooth finish. They can be reused multiple times.
Plastic blasting Media
Plastic media works well for aggressive stripping and will get you consistent results. it can strip paint from metals, plastics, and composites.
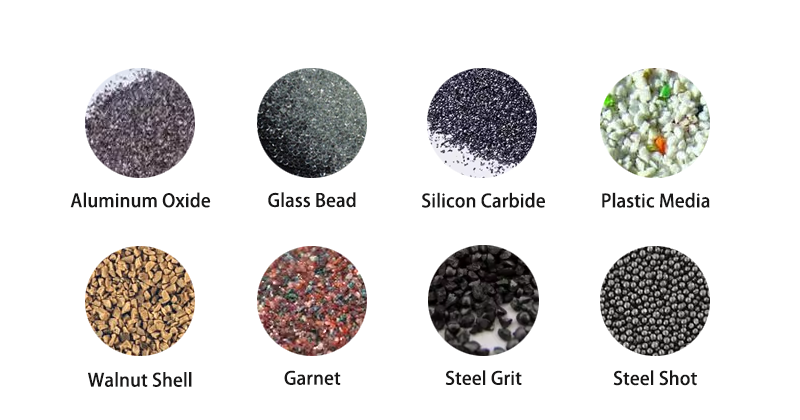
Silicon Carbide
Silicon carbide is the hardest abrasive and cuts quickly. It begins with small pieces and breaks while blasting. This media can be reused and is often used for etching glass and stone or for removing heavy rust.
Garnet
This abrasive is based on the complex silicate mineral garnet, which has high cutting force, uniform grain size and lower dust pollution.
Steel Shot
Steel shot consists of small steel balls used to clean and polish metallic surfaces. It strips off some material, bearing a shiny and smooth surface.
Steel Grit
Steel grit is used for aggressive blasting; it works quickly and can take off a variety of contamination. It is effective for etching into metals as long as the surface can withstand it.
Organic Compounds
Organic abrasives like corn cob and walnut shells are green. Corncob is used for delicate blasting work on wood, while walnut shells offer a more abrasive stripping action.
Sand Blasting Media Comparison Table
Abrasive Type | Hardness | Surface Finish Effect | Primary Applications |
Aluminum Oxide | 9 MH | Rough | Metal rust/oxide removal, deburring, ceramic surface roughening |
Glass Grit | 5-6 MH | Light to medium cleaning | Glass engraving, stone surface treatment, light metal cleaning |
Glass Beads | 5-6 MH | Smooth, matte finish | Stainless steel/aluminum peening, precision part cleaning, decorative matte finishes |
Silicon Carbide | 7 MH | Ultra-fine cutting | Hard materials (ceramics, composites) cutting, semiconductor precision grinding |
Plastic Abrasive | 2-4 MH | Very light cleaning | Delicate materials (plastics, electronics) deburring, aerospace composite cleaning |
Garnet | 7-8 MH | Medium roughness | Stone carving, ship/pipeline anti-corrosion, waterjet cutting |
Steel Shot | 60+ HRC | Smooth, uniform texture | Heavy-duty metal descaling, surface hardening (e.g., automotive parts), shot peening |
Steel Grit | 40-60 HRC | Aggressive cutting | Structural steel rust removal (bridges, ships), concrete surface profiling |
Cleanliness
Cleanliness measures how well impurities are removed from a workpiece after sandblasting. There are two main international standards for cleanliness: the U.S. “SSPC-” standard from 1985, and the Swedish “Sa-” standard from 1976. The Sa- standard has four grades: Sa1, Sa2, Sa2.5, and Sa3, it is commonly used worldwide.
Sa1 Grade – This is the lowest level, like the U.S. SSPC-SP7 grade. It involves simple manual brushing and sandpaper grinding. The coating protection is only slightly better than no treatment. For Sa1, the surface should be free of visible oil, grease, rust, and paint, but minor contamination may remain.
Sa2 Grade – Equals to the U.S. SSPC-SP6 grade. This level uses sandblasting, the basic cleaning method. The workpiece surface should be free of visible grease, dirt, rust, and paint, but defects may cover up to 33% of the surface. Slight rust and paint in dents are acceptable.
Sa2.5 Grade – This is a used standard in the industry, known as near-white cleaning. It’s often used as an acceptance standard. The surface should have no more than 5% defects, such as small shadows or slight discoloration, rust, or paint defects.
Sa3 Grade – The highest level, equal to the U.S. SSPC-SP5 grade, also called white cleaning. The surface must be completely clean, with no defects, rust, or paint allowed. There can be no shadows or discoloration at all.
Sand Blasting Roughness
The sand blasting grains impact and bounce outward. This impact creates indentations on the surface of a few thousandths of an inch, which is called the basic pattern. The rebound will make some surfaces protrude a few thousandths of an inch outward. The lower parts are called “valleys” and the higher parts are called “peaks”. Each sand grain impacting the surface will create a “valley” and a “peak”, which is the reason for the formation of roughness. It is expressed in MILL (mil), and one mil is 1/1000 second.
Why is Sand Blasting Necessary?
Sand blasting uses high-speed sand flow to process the part surface so that the workpiece surface gets a certain degree of cleanliness and roughness, the process improves the mechanical properties and aesthetic appearance of the workpiece.
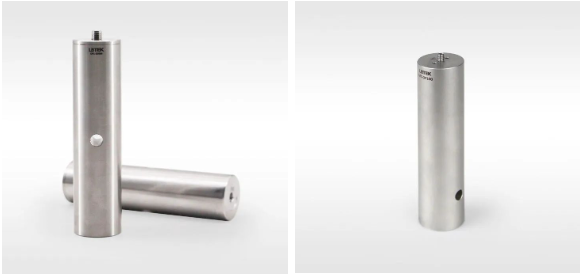
Pre-treatment of Coatings or Plating Layers
Sand blasting removes impurities like dirt, grease, and oxides from surfaces. It leaves a uniform, rough texture that improves the bond between parts and their coatings or electroplating. Different abrasives create varying levels of roughness to suit different needs.
Cleaning and Polishing of Rough Surfaces
Sand blasting cleans dirt such as oil and rust from castings, forgings, and heat-treated parts. It also polishes the surfaces, making them smoother and more visually appealing. The process reveals a consistent metallic color, enhancing the workpiece’s appearance.
Deburring and Surface Aesthetics
Sandblasting removes small burrs from workpieces, making the surfaces flat and safe. It also creates rounded edges where surfaces meet, improving the workpiece’s overall look.
Improving Mechanical Properties
Sand blasting creates a uniform, fine texture on parts, allowing lubricating oil to be stored on the surface. This improves lubrication, reduces noise, and extends the lifespan of machinery.
Stress Relief
Sandblasting reduces stress on a workpiece’s surface by hitting it with abrasive pellets. This strengthens the surface and is commonly used for parts like springs, tools, and aircraft blades.