Aluminum Anodizing Services
Explore our Type II and Type III anodizing services to improve your aluminum parts’ performance and visual appearance.
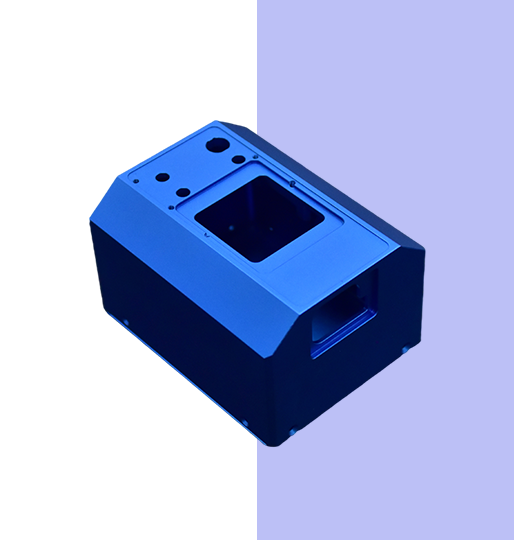
Aluminum Anodizing Specification
Anodizing offers more than durability and corrosion resistance to aluminum, it is an aesthetic finish that comes in various colors. We provide two types of anodizing: Type II and Type III. Check out our specifications below to make the best choice for your aluminum finishing needs.
Types |
Materials |
Colors |
Glossiness |
Thickness |
---|---|---|---|---|
Type II Anodizing |
Aluminum |
Clear, Black, Red, Blue, Purple, Custom |
Matte, Glossy |
8 - 12μm |
Type III Anodizing |
Aluminum |
Clear,Black |
Matte |
35 - 50μm |
Anodizing Type II Color Options
Type II anodizing allows for a custom choice of color selection so that you can tailor your aluminum finishes to meet your design specifications. The colors listed below are just a few examples of the standard options we provide. If you have a specific color you’re looking for, please reach out to our customer reps. We’re dedicated to helping you achieve your goals through custom solutions.
Anodizing Process
In anodizing, the surface of aluminum is increased by generating a strong oxide layer through an electrochemical process. In this process, the aluminum part is dipped in an acidic bath, usually made from sulfuric or chromic acid, while an electric current is passed through it. The part is attached to the anode, while the cathode attracts the positive ions, hence initiating a reaction that pulls the oxygen ions toward the aluminum surface.
This reaction makes the aluminum part porous, allowing it to bond with oxygen and develop a thick oxide layer. It gives excellent resistance against corrosion and wear, besides generally enhancing aesthetics.
The thickness and properties of the oxide layer depend on the type of anodizing applied. Type II anodizing produces a thin, 8-12 micron oxide layer and provides moderate protection with a smooth finish. On the other hand, Type III anodizing will produce a much thicker oxide layer, 35-50 microns, which has greater durability due to its higher resistance against wear and corrosion.
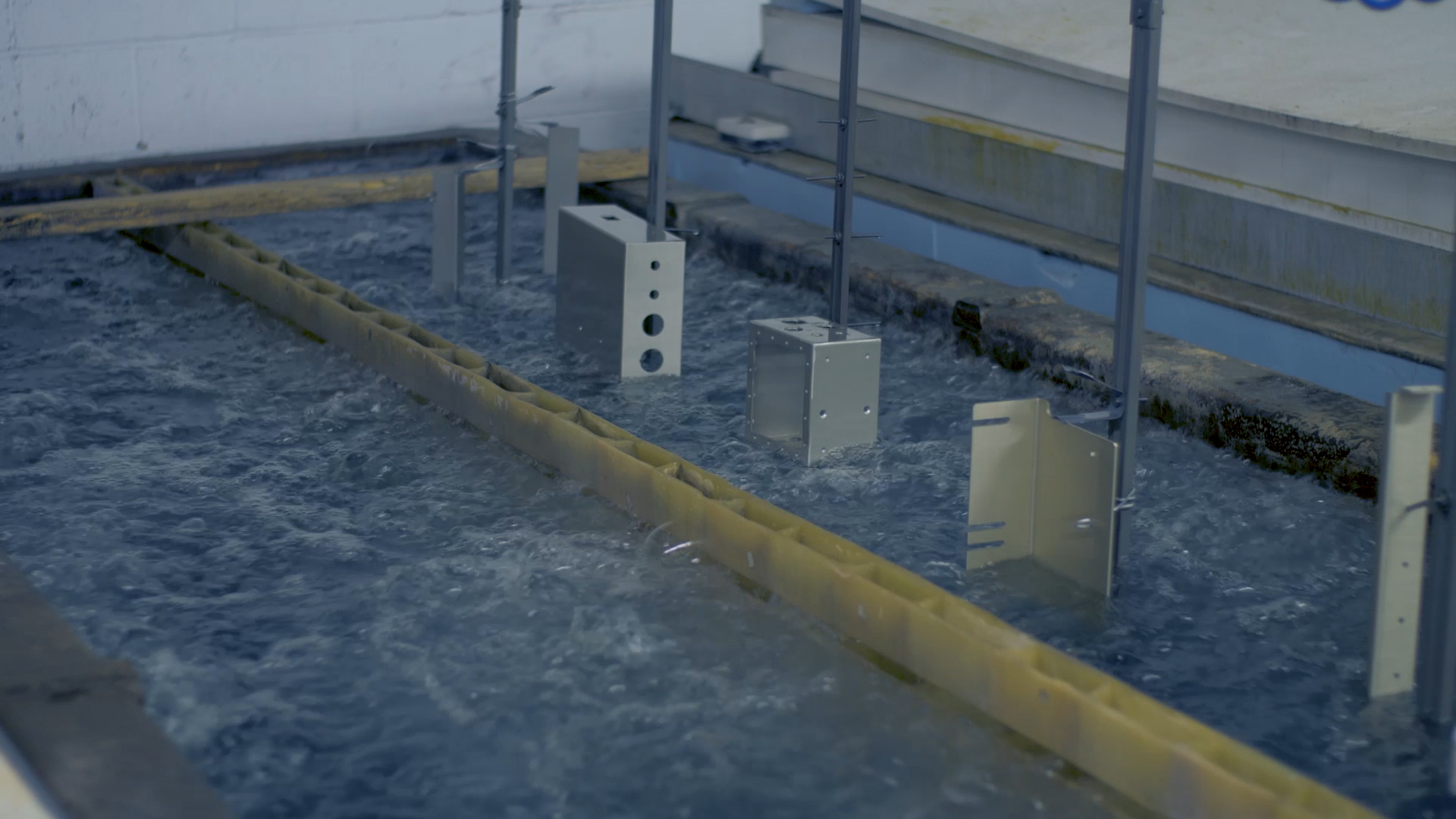
Advantages
- High corrosion resistance
- Improvement in aesthetic appeal
- Suitable for parts with tight tolerance
- Improved surface hardness than raw aluminum
Notes
- Parts should be properly finished before treatment as anodizing does not mask pre-existing surface defects
- The final color may vary based on the alloy grades
- Anodized parts requires specific handling to avoid scratching or damaging the finish
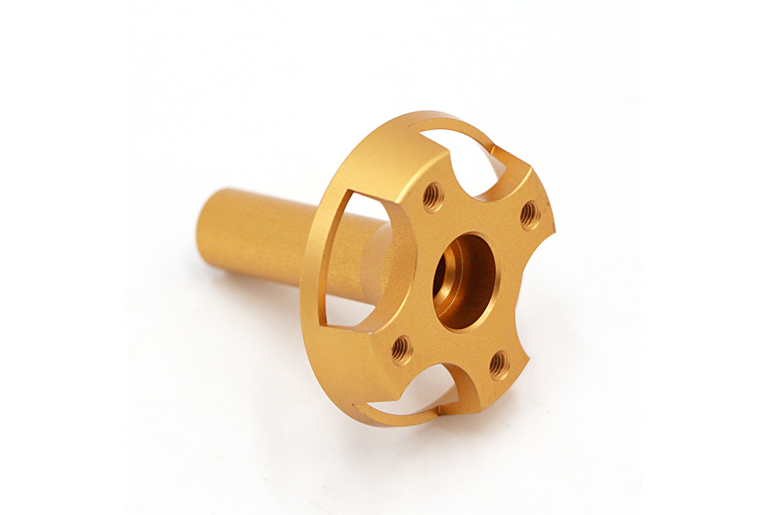
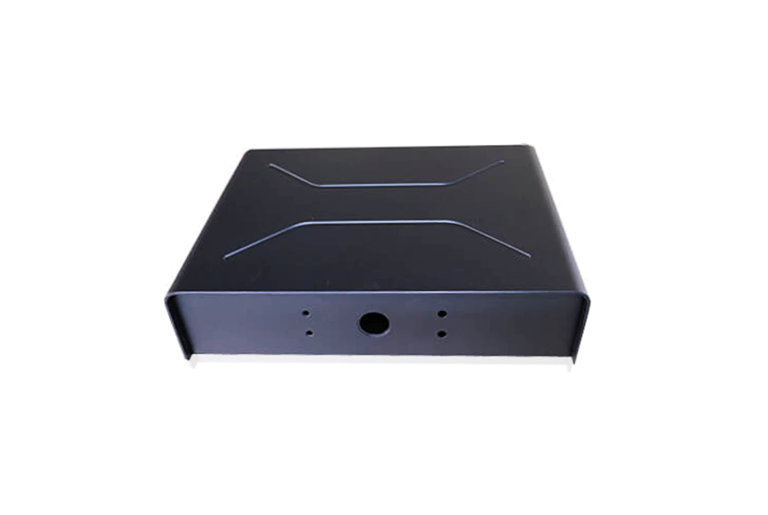
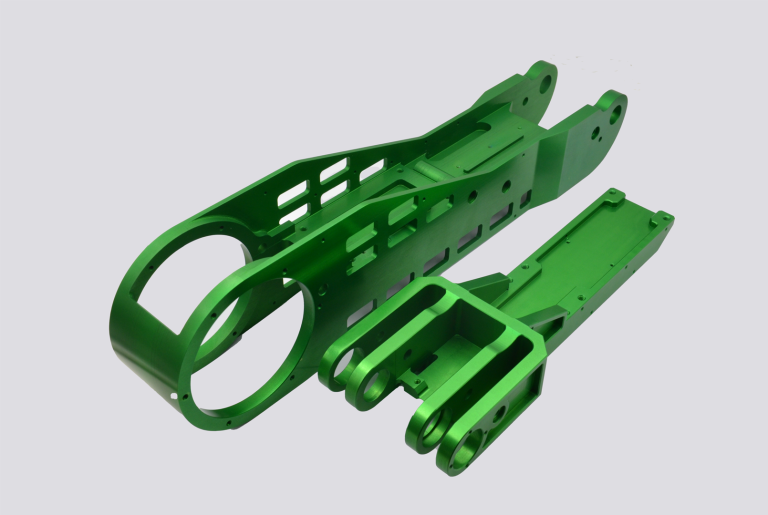
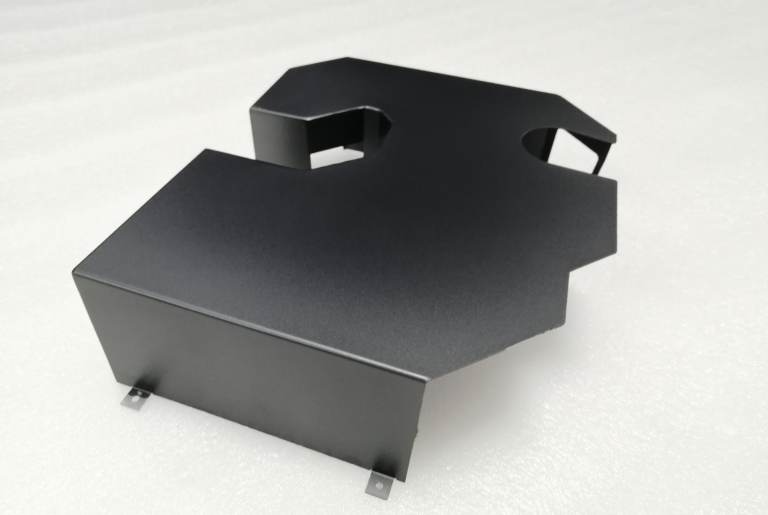

- Anodizing holds parts on jigs or racks, which can scratch untreated areas. If you have areas that need to be scratch-free, send in a drawing and we will follow our cosmetic procedure.
- Anodizing insulates your parts, making them less conductive.
- Anodizing does not require masking by default because it does not significantly increase the thickness of the part. Please note in your CAD file if you have areas that should be masked or plugged.
- Type III anodizing can add considerable thickness to your part's surface. To preserve critical surfaces, we recommend plugging or masking threaded/reamed holes and other vital areas.
Anodizing Design Considerations
What are the differences between anodizing and powder coating?
The anodizing and powder coating processes differ in process, durability, and aesthetic appearance. Anodizing is an electrochemical treatment that enhances corrosion resistance and wear resistance, especially for aluminum, by forming a protective oxide layer. Where powder coating is applied as a thick, colored coating on the surface and gives an even, glossy appearance with a broad range of colors, it is less resilient against scratching and chipping. For a more in-depth look at the differences, read our blog: Finishing Showdown: Anodizing vs Powder Coating
What are the differences between Type II and Type III anodizing?
While both Type II and Type III refer to anodizing of aluminum, they differ in thickness, durability, and application. Generally, Type II anodizing, performed with sulfuric acid, produces an oxide layer of 8-12μm thickness. It is ideal for parts that need a good balance between moderate corrosion resistance and aesthetic finishes. By contrast, Type III, or hard anodizing, is a more aggressive process that builds a much thicker oxide layer, 35-50μm, giving it the best wear resistance and strength for parts exposed to harsh conditions. For further information on which type best suits your needs, check out our comprehensive blog on Type II vs. Type III anodizing.
What metal can be anodized?
Most anodizing is performed on aluminum, in which the process forms a hard, corrosion resistant oxide layer. Other metals that may be anodized are titanium and magnesium, but once more, by far the most common is aluminum.
How do you know if something is anodized?
Electrical conductivity tests are one of the best ways to determine whether the aluminum has been anodized or not. Anodized aluminum becomes an insulating material owing to the non-conductive oxide layer formed at the surface.