Sand Blasting Service
Explore our sand blasting services to create quality parts with a clean, matte finish ready for additional processing.
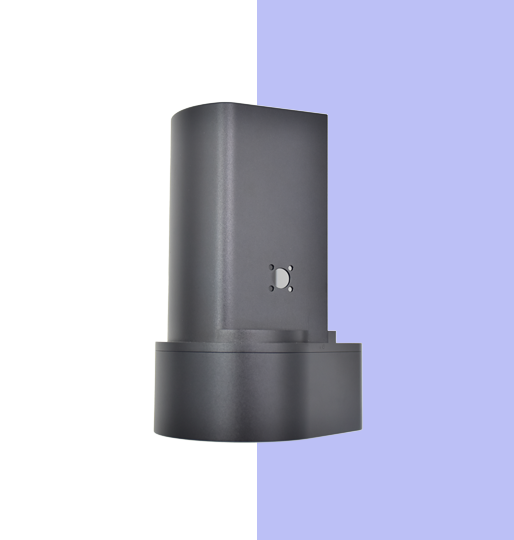
Sand Blasting Specification
Sand blasting is a process in which a metal or surface is cleaned, roughened, or shaped by the action of blasting with abrasive particles such as sand or any other material. The technique uses compressed air or water to force the abrasives at high velocity for the removal of dirt, rust, old paint, and imperfections. It is one of the fastest ways to restore surfaces to give a fresh, smooth, or textured finish.
Materials |
Media |
Colors |
Glossiness |
Surface Texture |
Metals |
Glass beads with grit #80, #100, 1#20, #150 |
White, Black,Clear |
Matte, Glossy |
Matte/Satin |
---|
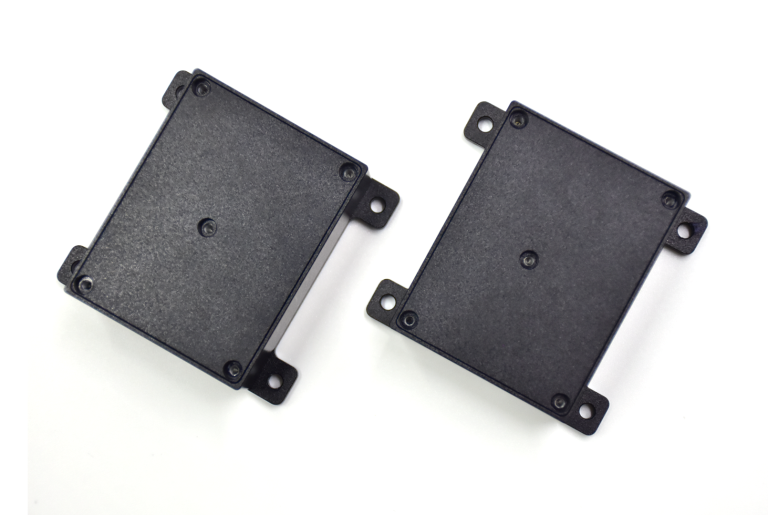
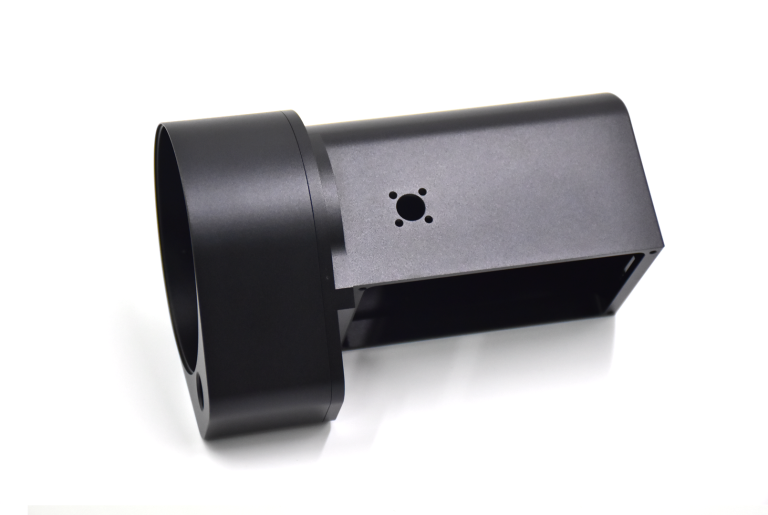
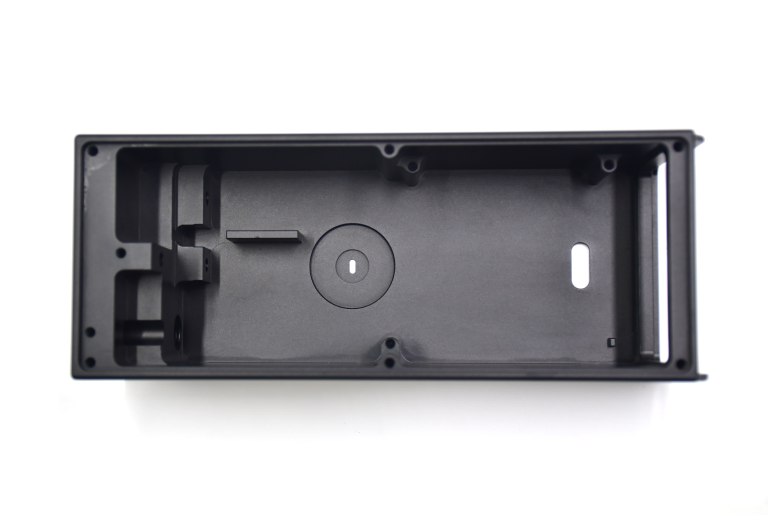
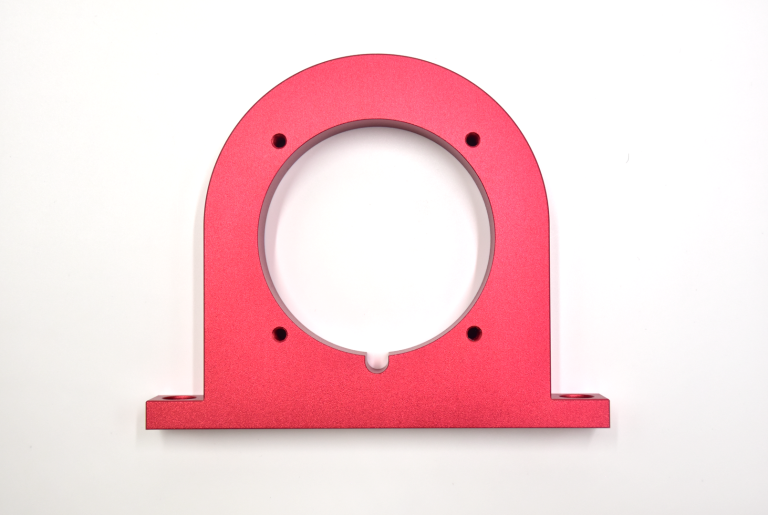
Advantages
- Efficient removal of contaminants such as rust, paint, and scale
- Sand blasting surface has the ideal texture for secondary preparation processes like painting, coating, or bonding.
- It is an environmentally friendly surface finishing option using non-toxic blasting media.
Notes
- Sand blasting may not be suitable for preparing smooth surfaces.
- The outcomes of the product improve sequentially with the use of sandblasting grades #80,#100, #120, #150
Sand Blasting Finish
Sand blasting smoothes metals by blasting them with abrasive glass beads propelled at high pressure from the orifice of a blasting tool. The coarser, larger beads leave a grainy, matte finish, whereas smaller beads provide a satin finish. For most hard metals, this will be a good treatment for polishing and deburring after machining.
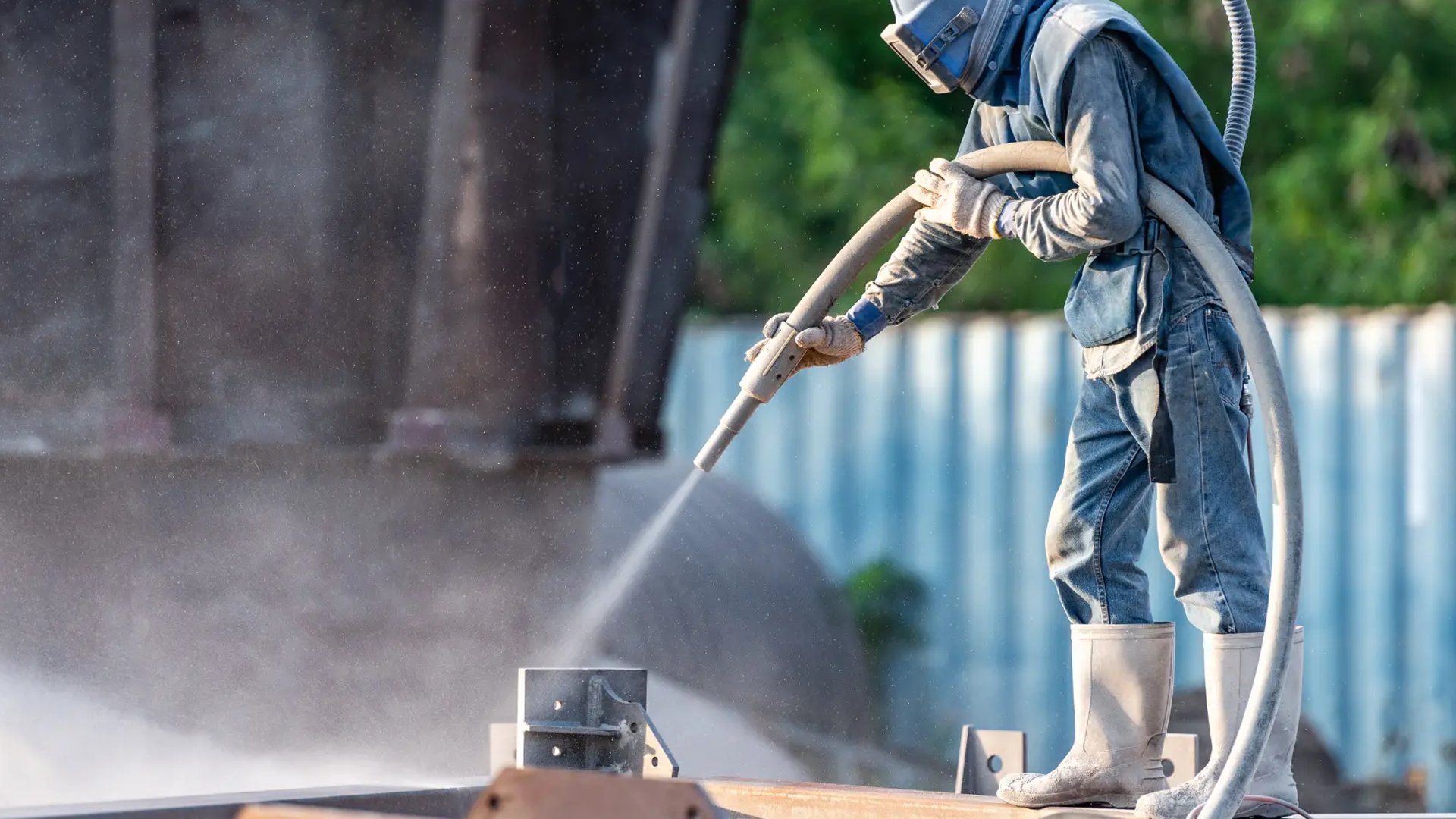
- Plugging threaded/reamed holes not required unless tolerances are very tight, as thickness change is minimal.
- It is better to avoid blasting thin walls since they are prone to deformation.
- Anodizing doesn't require masking by default because it doesn't significantly increase part thickness. If you need specific areas masked or plugged, please specify that in your CAD file.